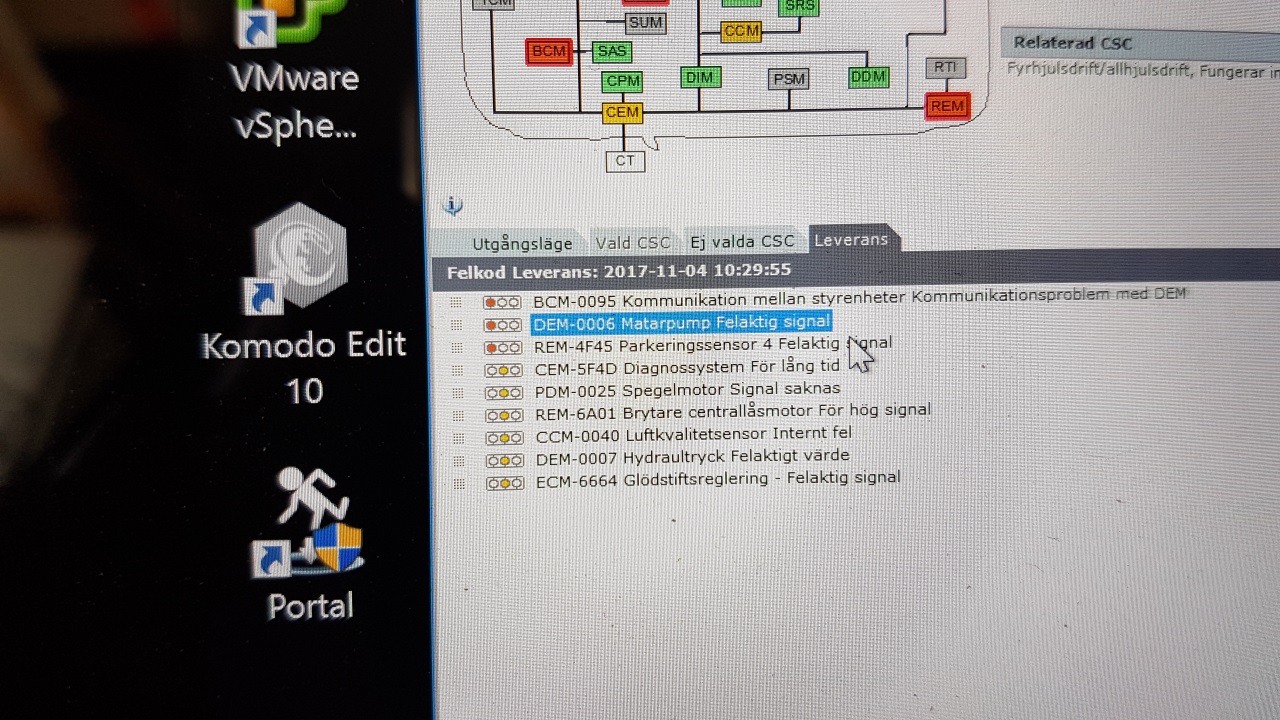
Vi har haft ett felmeddelande i V70:n nu en tid, ”Antisladd Service Erfordras”. Jag har tänkt att det måste bero på att jag råkat förstöra en sensor till ABS-systemet, som mäter hjulens rotationshastighet, när jag jobbat med bromsarna på bilen, men när jag kopplade in verktyget i bilen och fick felmeddelandena:
BCM-0095 och DEM-0006 så förstod jag ganska snabbt att det var någonting annat som var fel. Efter att ha testkört bilen med datorn ikopplad såg jag att jag hade hastighetsangivelser på alla hjulen, så ABS-givarna fungerar som det ska. Dessutom fungerar ABS:en på bilen, men både antispinn- och antisladdfunktionen var ur spel, och fyrhjulsdriften fungerade inte.
Om man läser detaljerna för felet så är den troliga orsaken aningen att kablaget är skadat, eller att styrelektroniken för haldexkopplingen är trasig. Den lilla elektroniklådan är väldigt dyr, så det är inte kul att byta den i onödan.. Som tur är finns det mycket information på google, och efter lite letande kom jag fram till att en orsak till att man får dessa felkoder är att hydraulpumpen som aktiverar haldexkopplingen är trasig. En vanlig kolborstmotor – känns rätt troligt att den kan vara lite sliten efter 32000 mil på bilen.. dessutom är den relativt billig och enkel att testa funktionen på – så sagt och gjort..
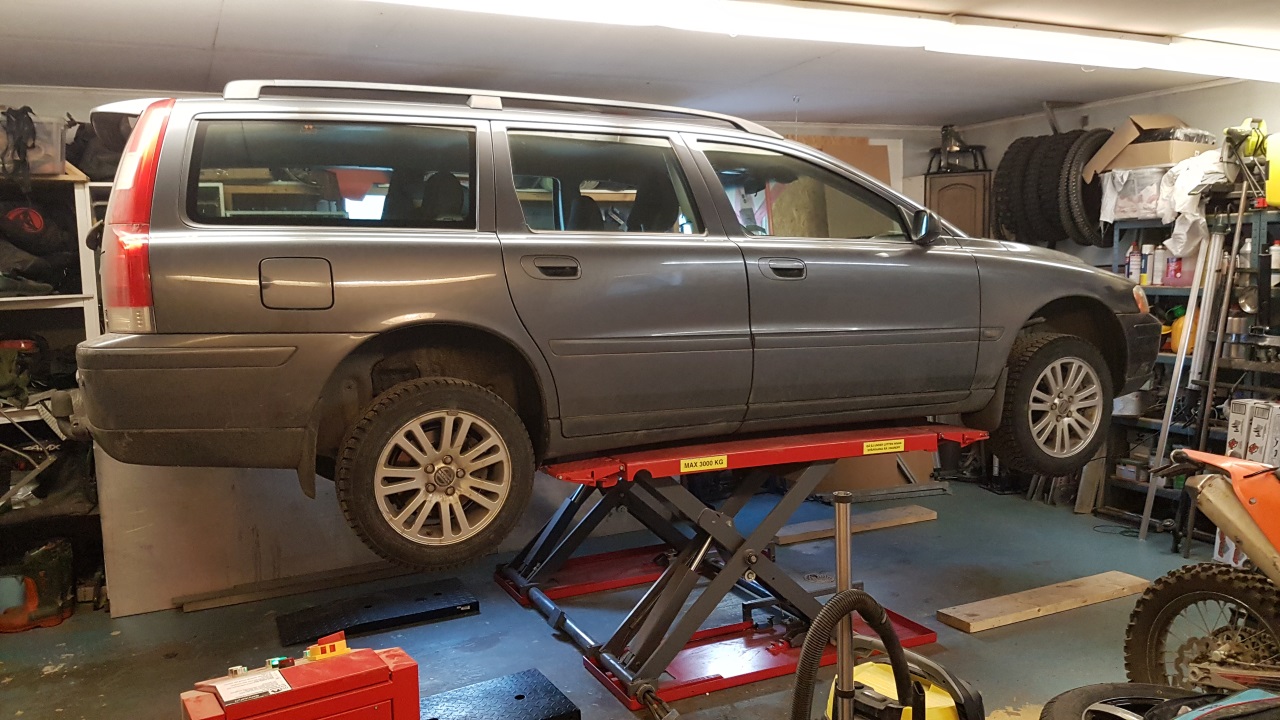
.. upp med bilen på lyften igen. Eftersom att lyften lyfter bilen en meter över golvet så har man rätt gott om plats att komma åt underredet..
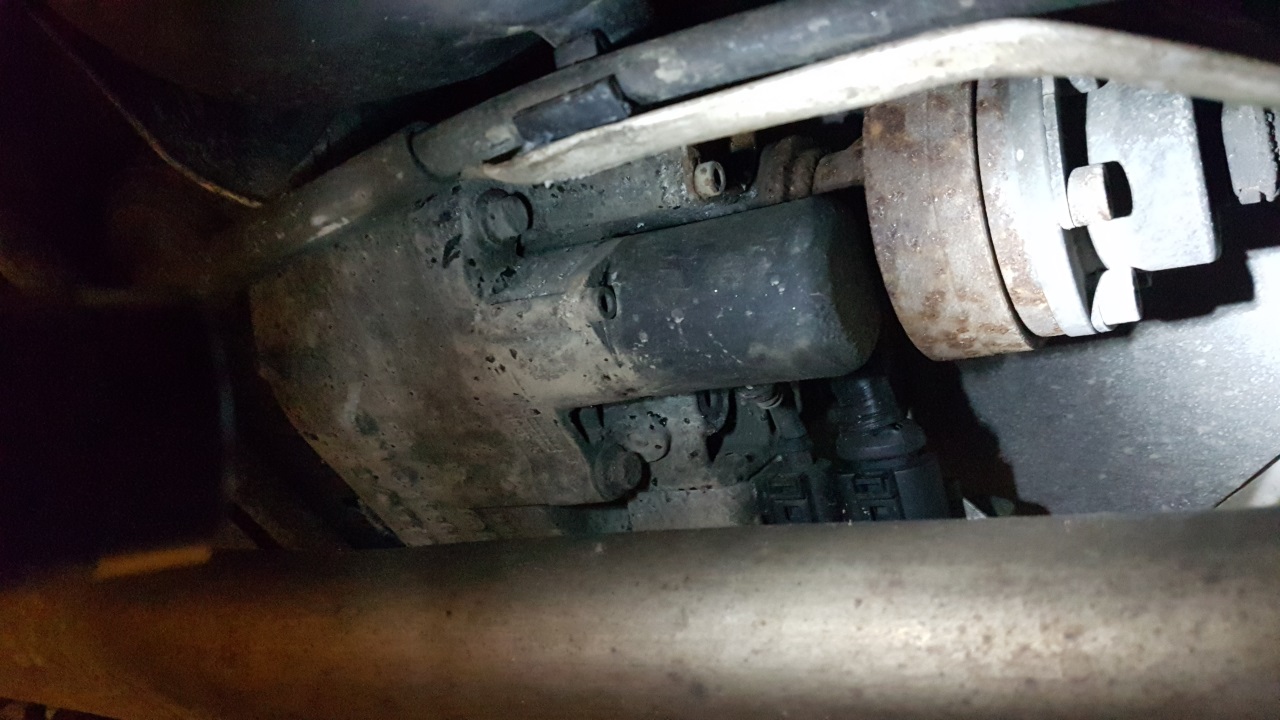
Den lilla svarta klumpen mitt i bilden är pumpen som jag misstänker (hoppas) är boven i dramat.
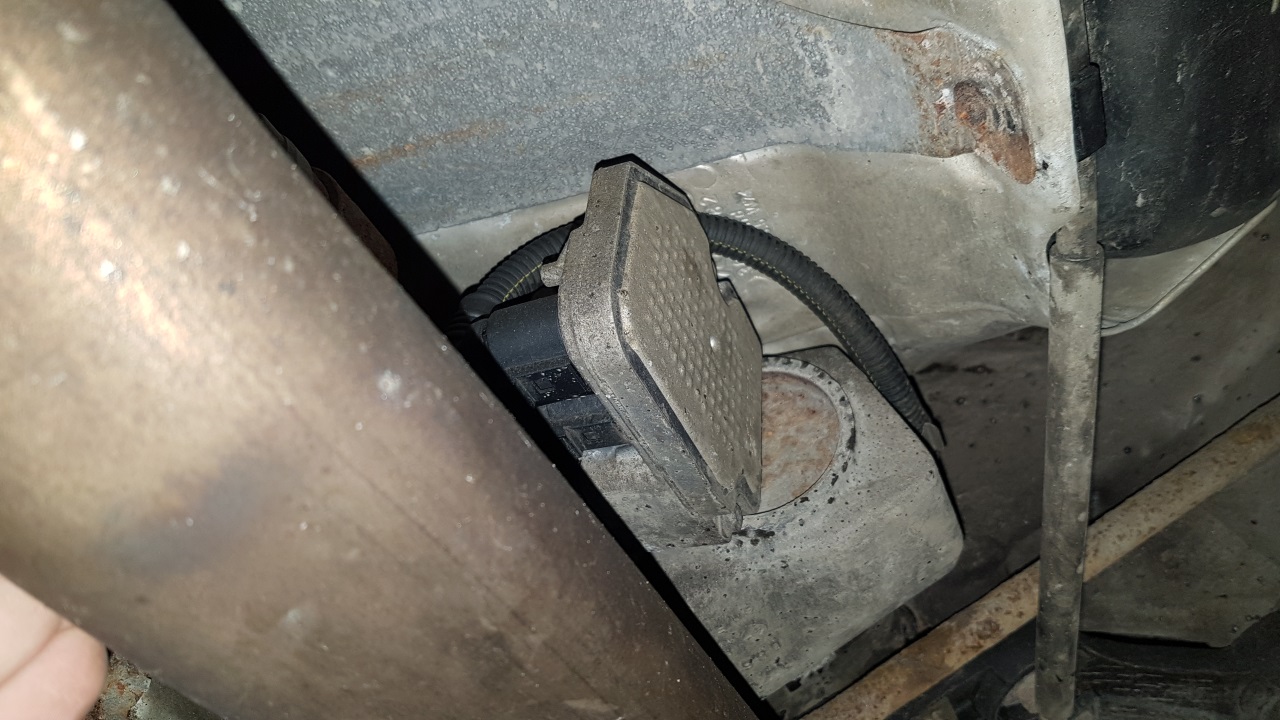
.. på andra sidan haldexen sitter elektronikenheten, som jag hoppas är hel..
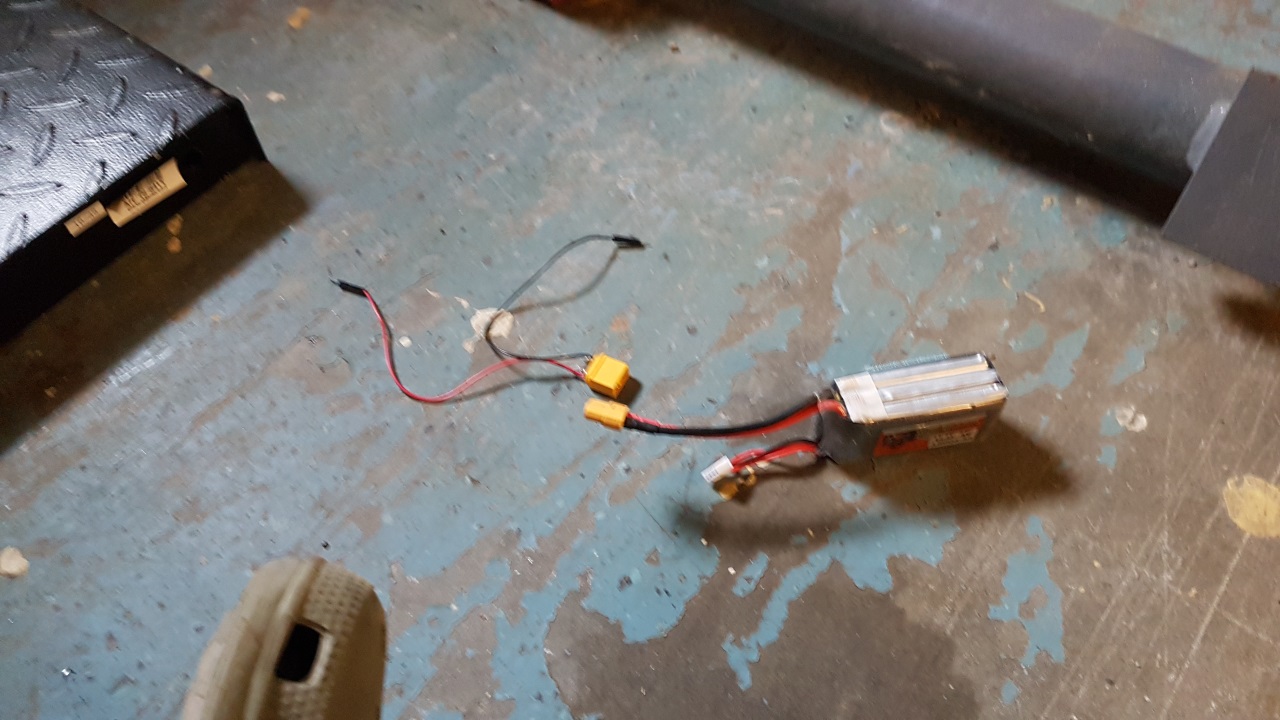
För att testa pumpen lödde jag ihop en liten kabel, som med hjälp av ett 3 cells LiPo-batteri levererar ungefär 12v..
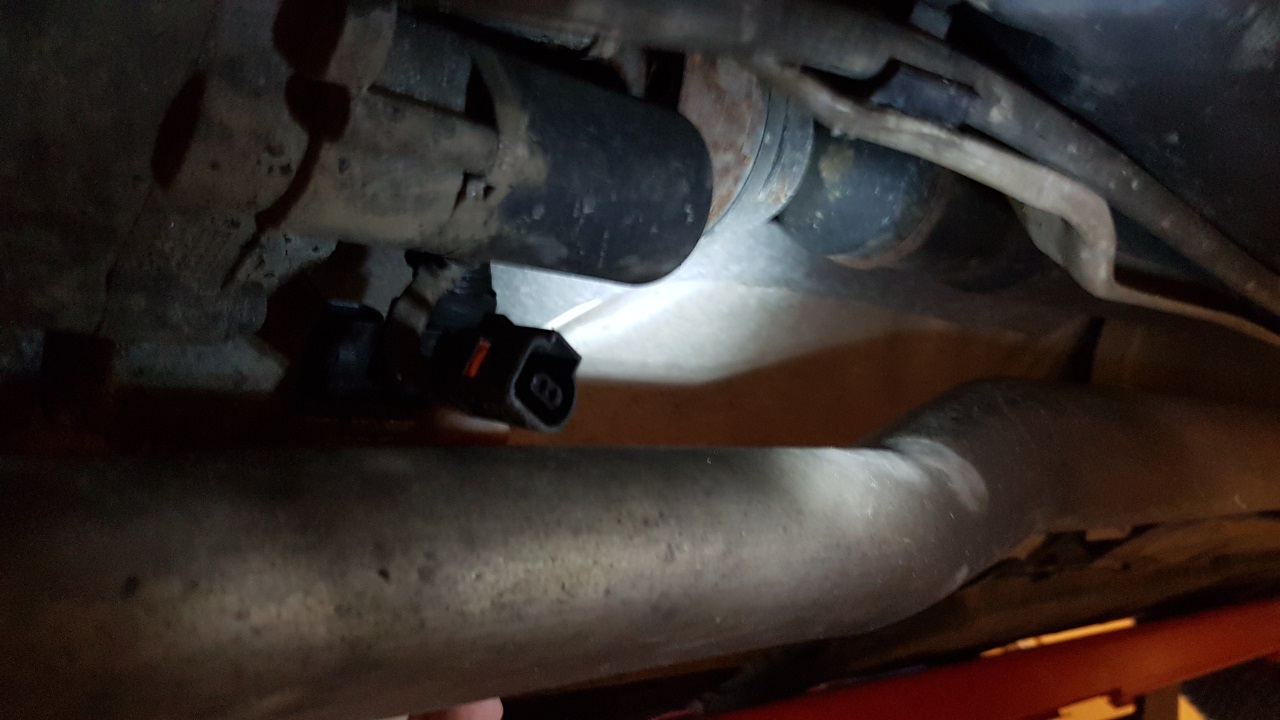
.. och sen är det bara att koppla ur kabeln från pumpen, där den sitter i styrdonet (den med två kablar, inte den med tre) och testa att mata 12v på pinnarna i den. När jag spänningssatte pumpen var den knäpptyst.. troligt fel alltså! Det bekräftade det jag misstänkte när jag såg i datorn att pumpen i snitt drog 0,04A – dvs, den går inte alls.
Att komma åt pumpen underifrån är enkelt, och att lossa pumpen innebär bara att skruva ur två stycken insexskruvar som håller den på plats. Problemet kommer sen, när man inser att man måste dra pumpen 3cm rakt ut för att få loss en, och avståndet till kopplingen för kardanaxeln är bara ett par ynka millimeter. Det innebär att – för att kunna byta pumpen – så måste kardanaxelns bakre infästning bort. För att lossa kardanaxeln så måste avgassystemet ur vägen, så vi börjar där.. Avgassystemet är ordentligt ihoprostat efter 32000 mil, men jag insåg rätt snabbt att jag inte behöver dela på det, det räcker med att skruva loss de plattor som sitter under avgaset, och haka loss gummifästena baktill för att kunna vika avgassystemet ur vägen..
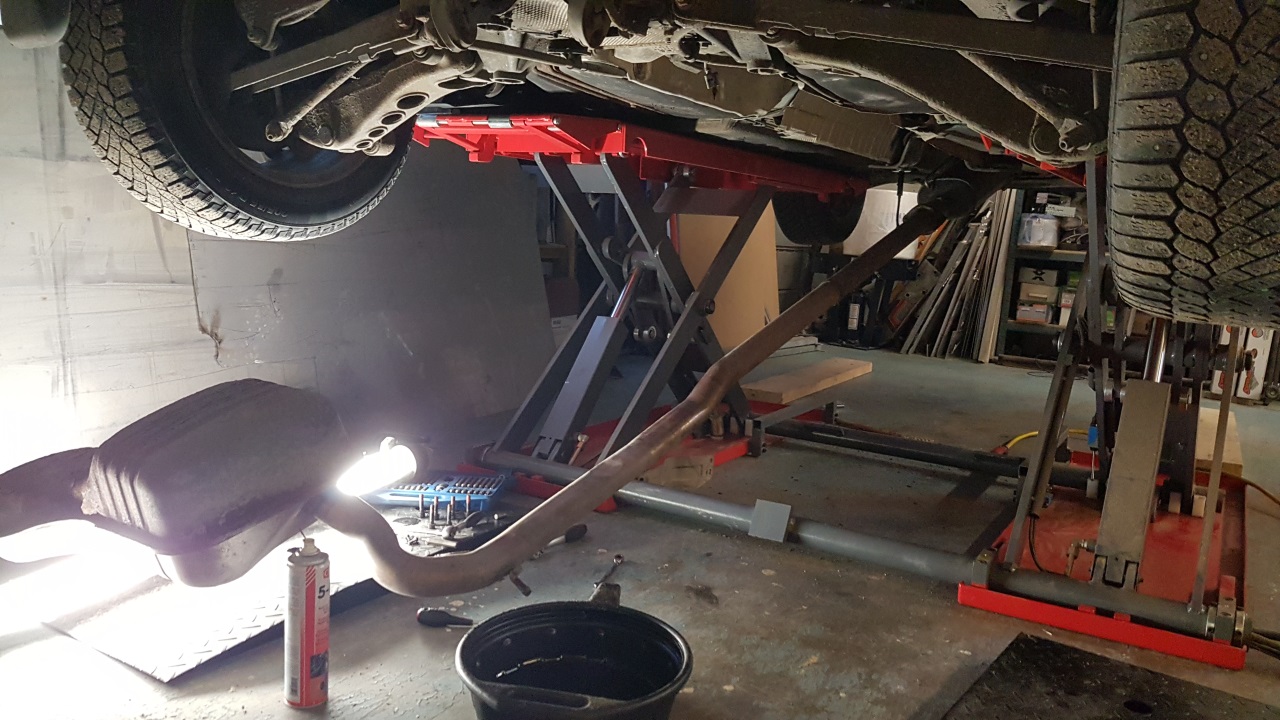
Eftersom att jag är lat så försökte jag självfallet lossa kardanen utan att lossa avgassystemet först, men det fick jag ganska snabbt ge upp, för den platsen finns inte under bilen för att det ska gå.. Att lossa kardanen är relativt enkelt, om man vet hur man gör. Steg ett är att lossa de 6 insexskruvar som håller ihop hela kopplet. Dessa är gänglåsta och sitter rätt ordentligt, men det gick förvånansvärt bra att lossa dem iallafall.
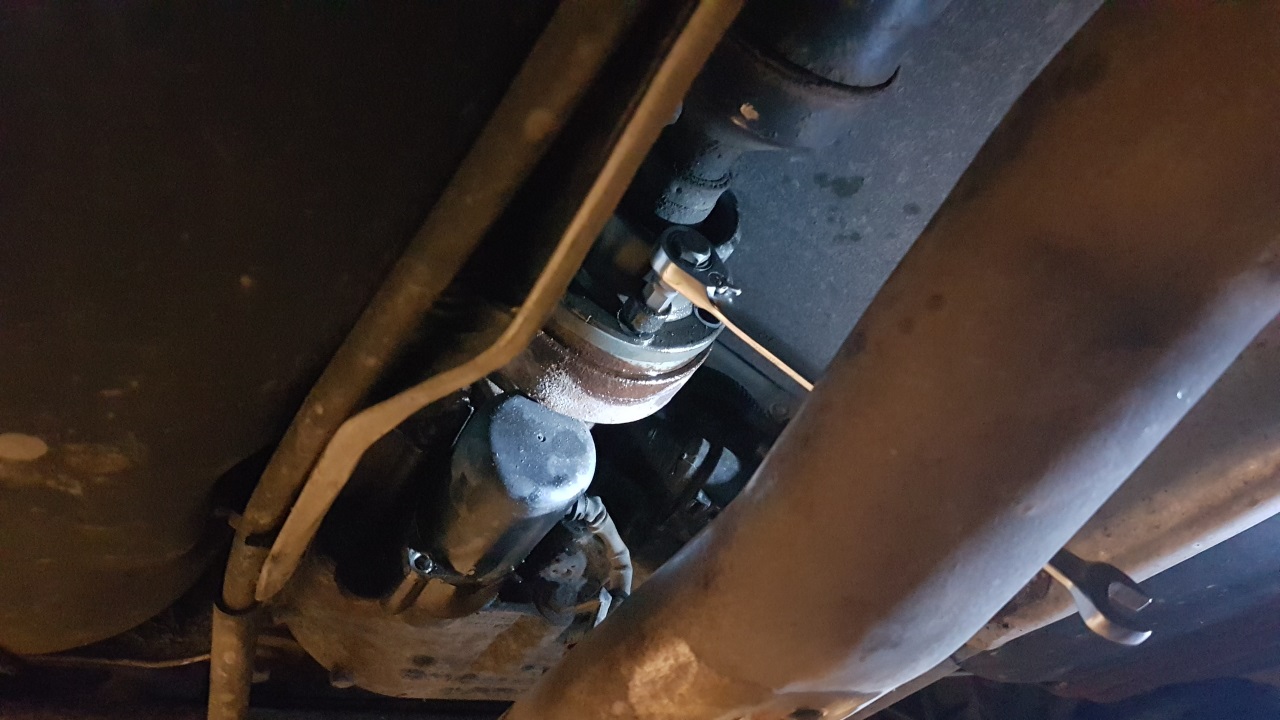
Det är trångt att komma åt runt kardanen, och eftersom att jag lagt min insexnyckelsats på något bra ställe där jag inte hittar den så fick jag lösa det med en insexbits och en 10mm nyckel, men alla sätt är bra.. 😉
Det som händer när man lossar dessa skruvar är att kåpan som håller fettet i kardanknuten på plats lossar. Det är helt omöjligt att få loss kardankoppligen efter detta, men med lite googlande hittade jag information om att det finns ett antal extra gängade hål på baksidan av kardankopplingen där man kan skruva in en M8 skruv för att pressa isär kardanen.. Tyvärr är det extremt ont om plats på baksidan, så efter att ha plockat bort elektronikenheten – vilket bara handlar om att lossa den kvarvarande kabeln, och lossa två insexskruvar – så fick jag tillverka ett par specialverktyg för att kunna komma åt att pressa isär kopplingen.
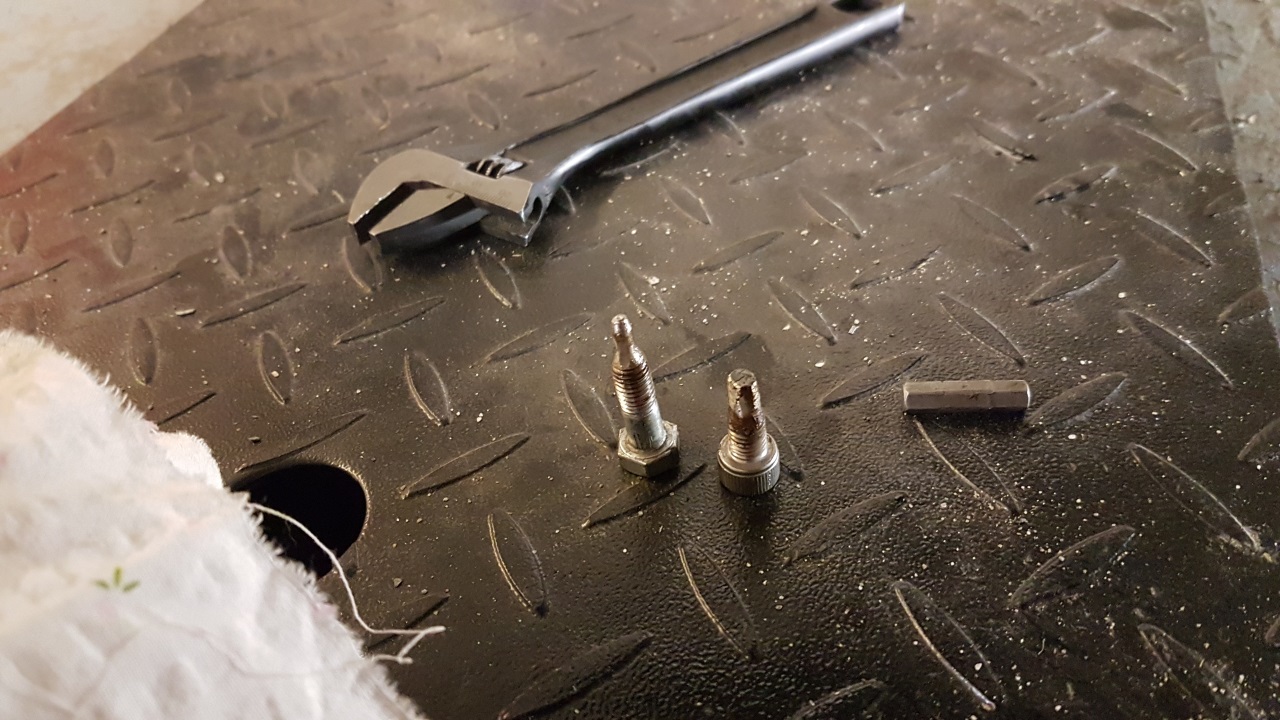
Specialverktyg
Dessa skruvas enkelt in i baksidan på kardankopplingen..
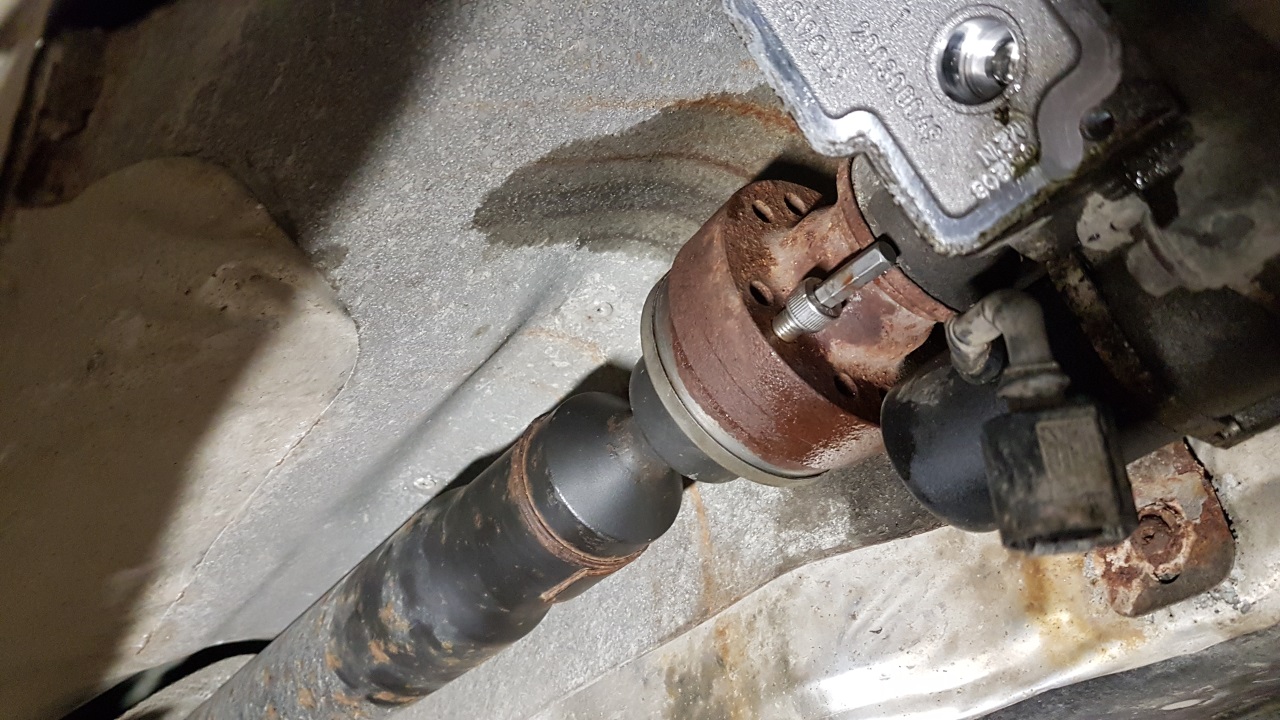
.. och sen våldar man lagom, ser till att inte snedbelasta kopplingen för mycket, och knackar lite försiktigt på knuten tills den hoppar loss. För att kunna vika kardanaxeln ur vägen måste man även lossa lagerfästet på mitten, 4st skruvar mitt under bilen, och för att inte lägga för mycket böjning på värmeskölden som sitter i kardantunneln lossade jag även plåten som sitter längst fram i tunneln – 4 skruvar till.. sen är det bara att plocka ner axeln:
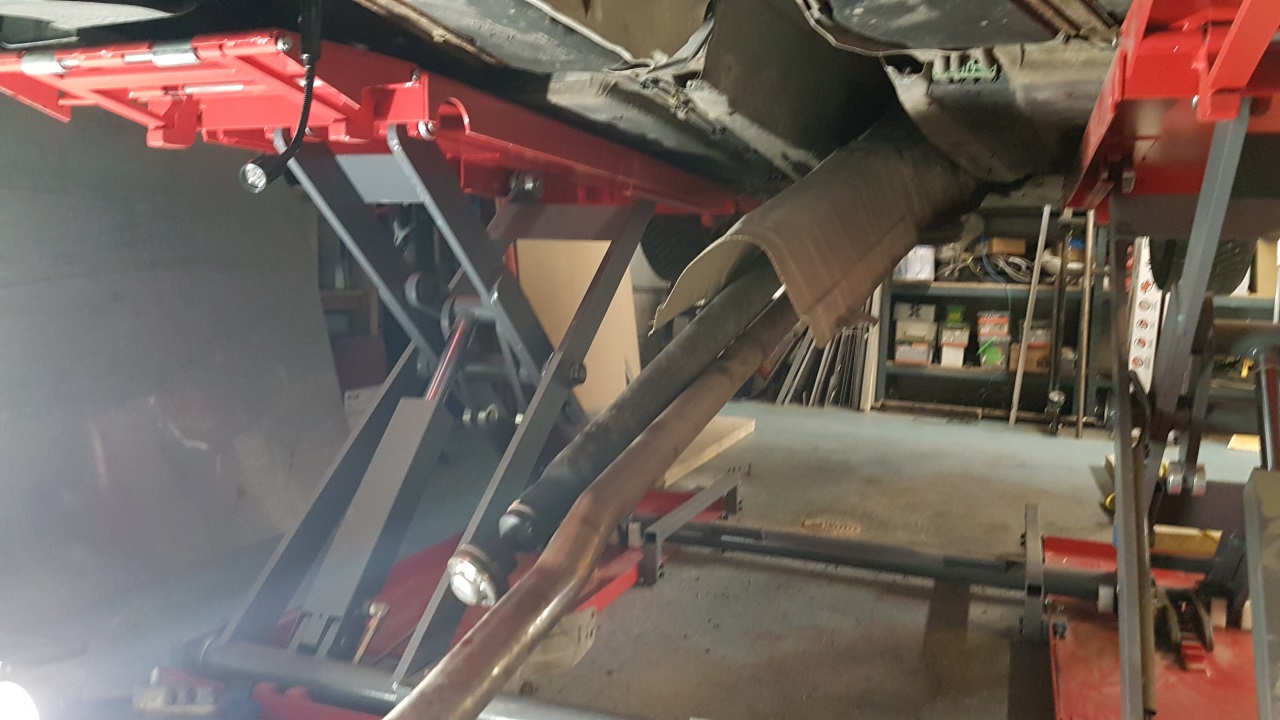
Nu är allt det svåra gjort, i den delen av kopplingen som sitter kvar finns en centrumbult som ska bort..
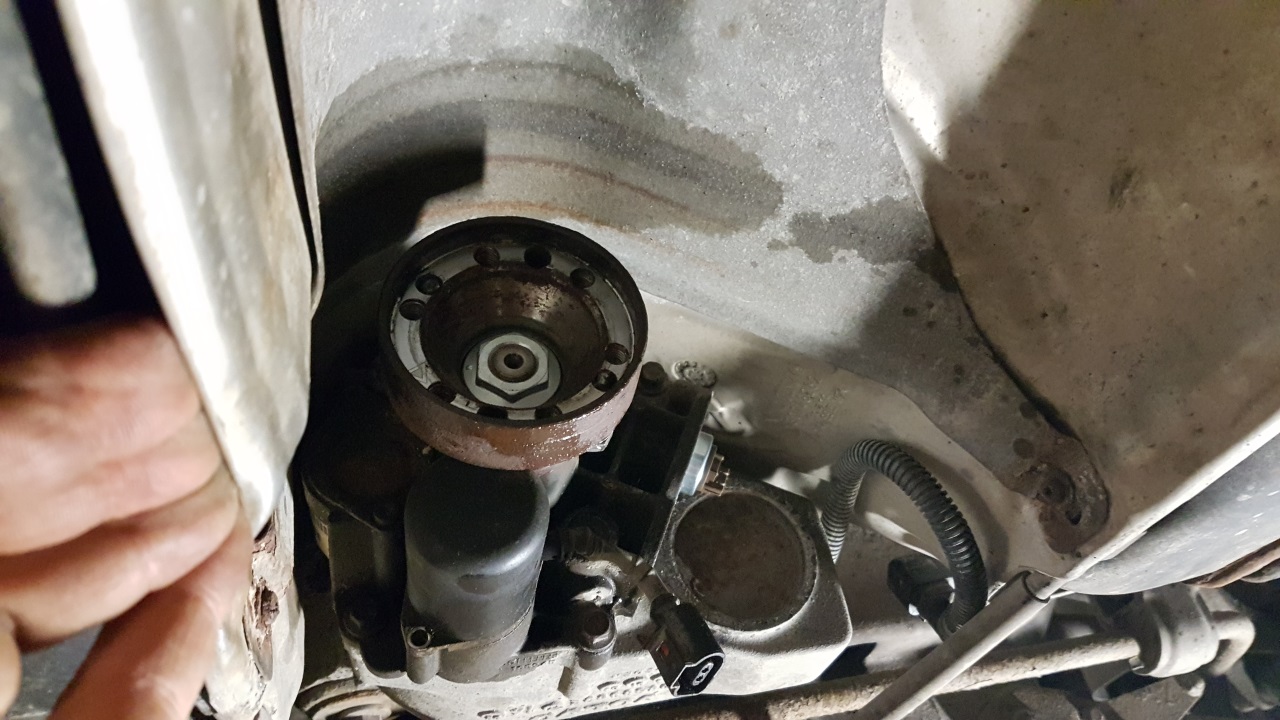
(Mutterpicka funkar jättebra här) .. och sen är det bara att lirka loss flänsen..
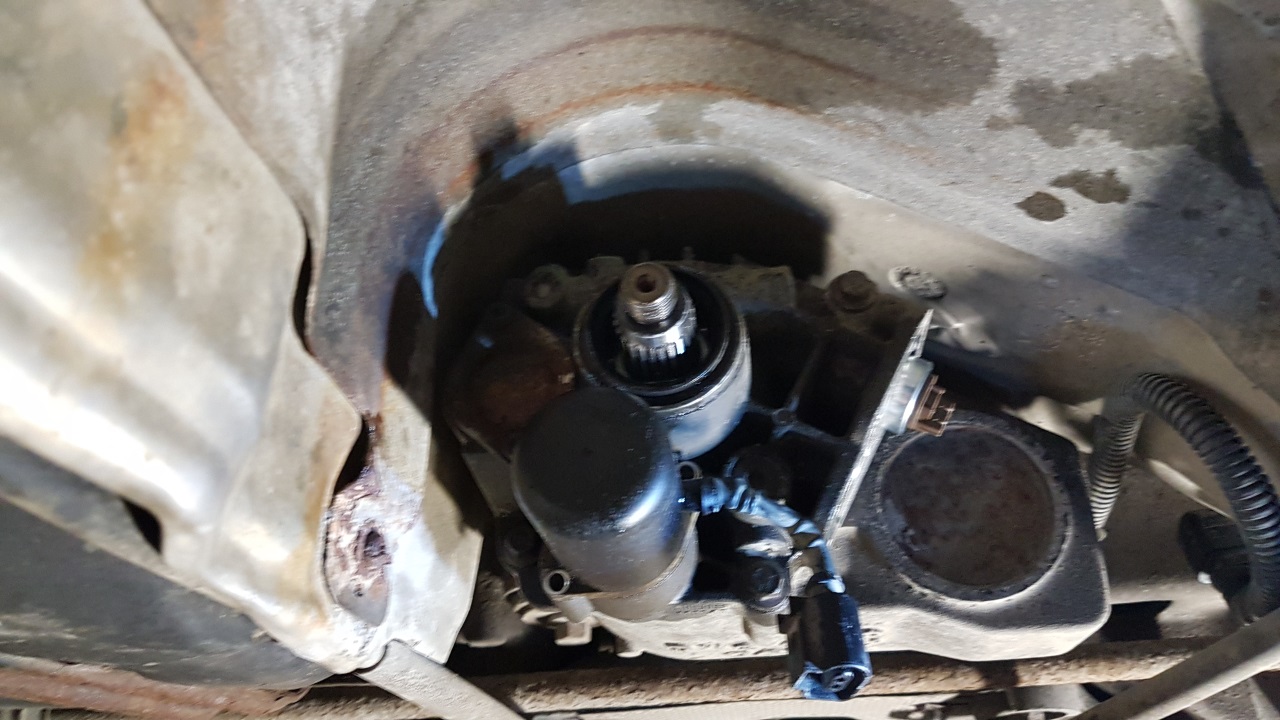
.. och nu kommer vi enkelt åt att byta pumpen!
Här ska man egentligen passa på att byta tätningen som sitter innanför flänsen, men eftersom att jag hittat för dåligt med information om detta på google så hade jag inte den tätningen – så det får bli nästa gång. Däremot tänkte jag passa på att byta filter när man ändå måste dränera växeln på olja..
Nu är det som sagt bara att lossa de två skruvar som håller pumpen, och dra den rätt ut ett par centimeter, så är rivarbetet klart. Här kommer all hydraulolja som finns i kopplingen att rinna ut, så ha ett uppsamlingskärl lämpligt till hands.
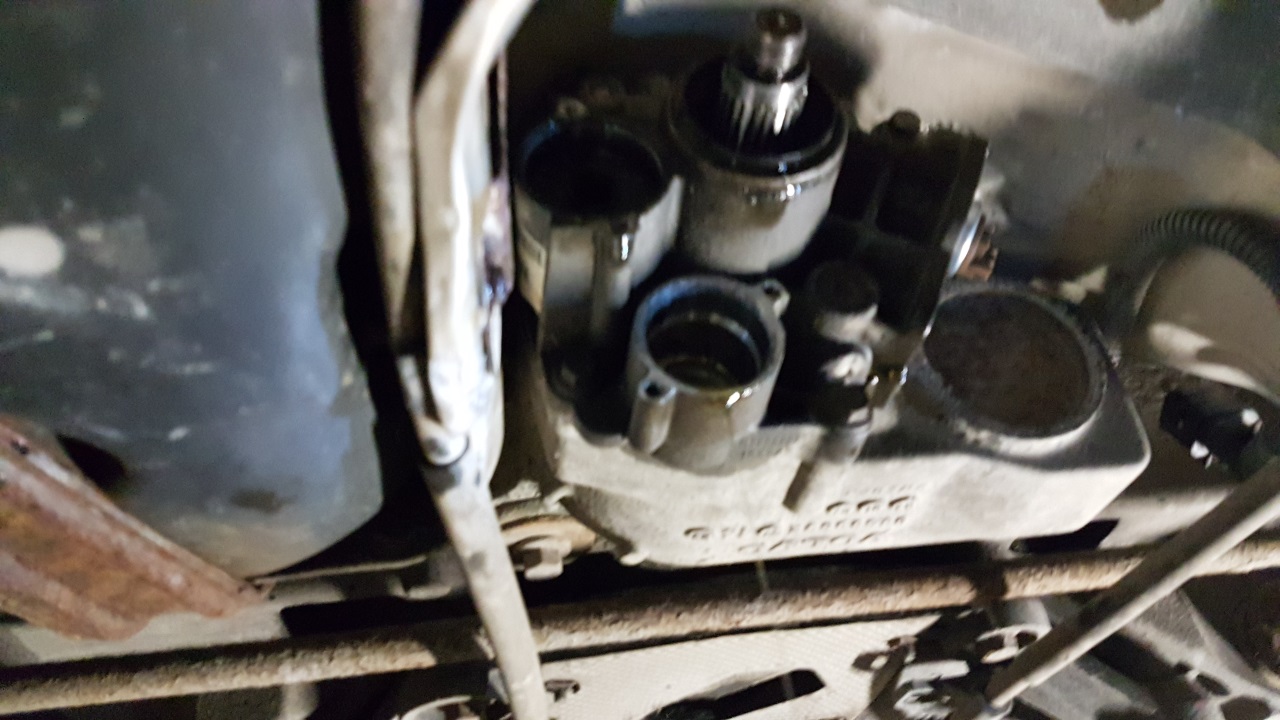
Filtret sitter i den övre håligheten, snett ovanför pumpen.. Tyvärr hade jag fått fel filter, så jag får även avvakta med att byta det tills nästa gång. Det kändes mindre bra, men vad gör man när man behöver bilen?
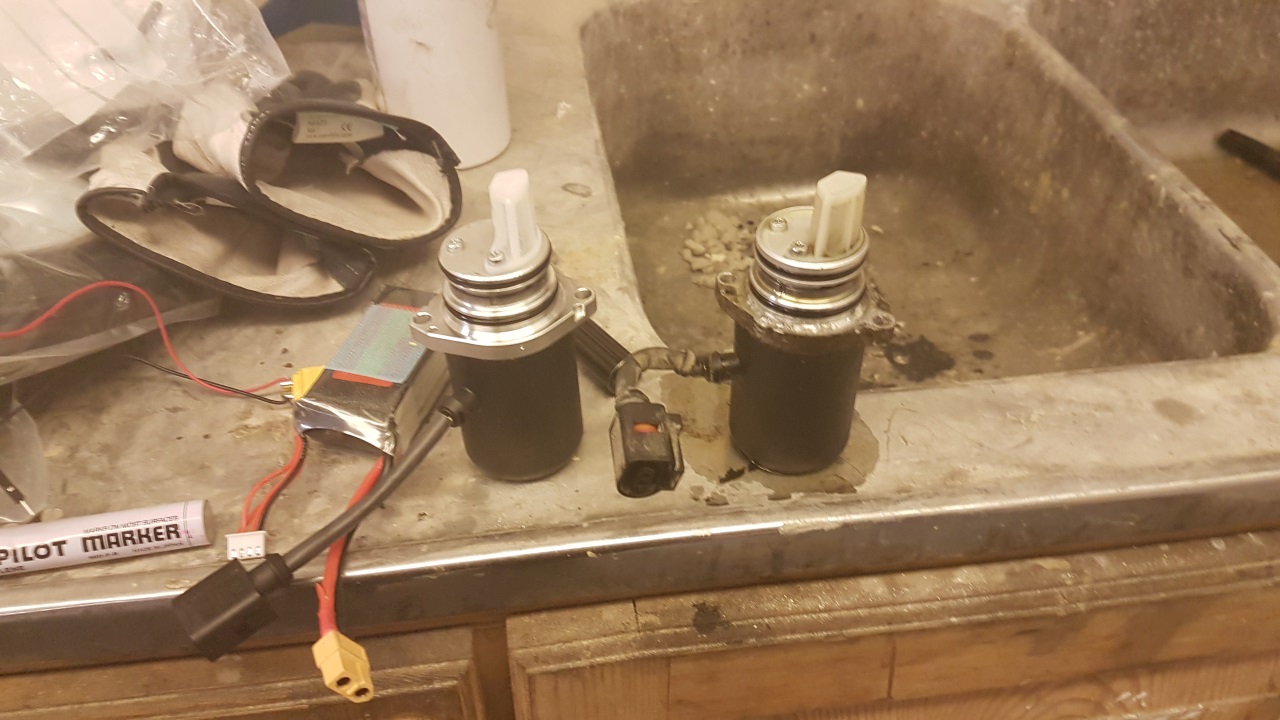
Nu när allt är löst så passade jag på att testköra pumpen på batteri igen, och då hoppade pumpen igång och gick hur bra som helst. Låter och känns precis som den nya pumpen.. men när man startar och stoppar ett par gånger så hamnar man lite då och då i ett läge där pumpen inte startar. Då krävs ett slag i sidan på pumpen för att den ska hoppa igång igen – ett typiskt tecken på att kolen i motorn är slut. Nu har jag en ny pump, och jag vill inte behöva göra detta arbete varje vecka, så jag byter ut pumpen.. men jag ska plocka isär den gamla och kolla ifall att den går att renovera, det kommer mer info om det senare.
Som alltid så går återmonteringen mycket snabbare än demonteringen..
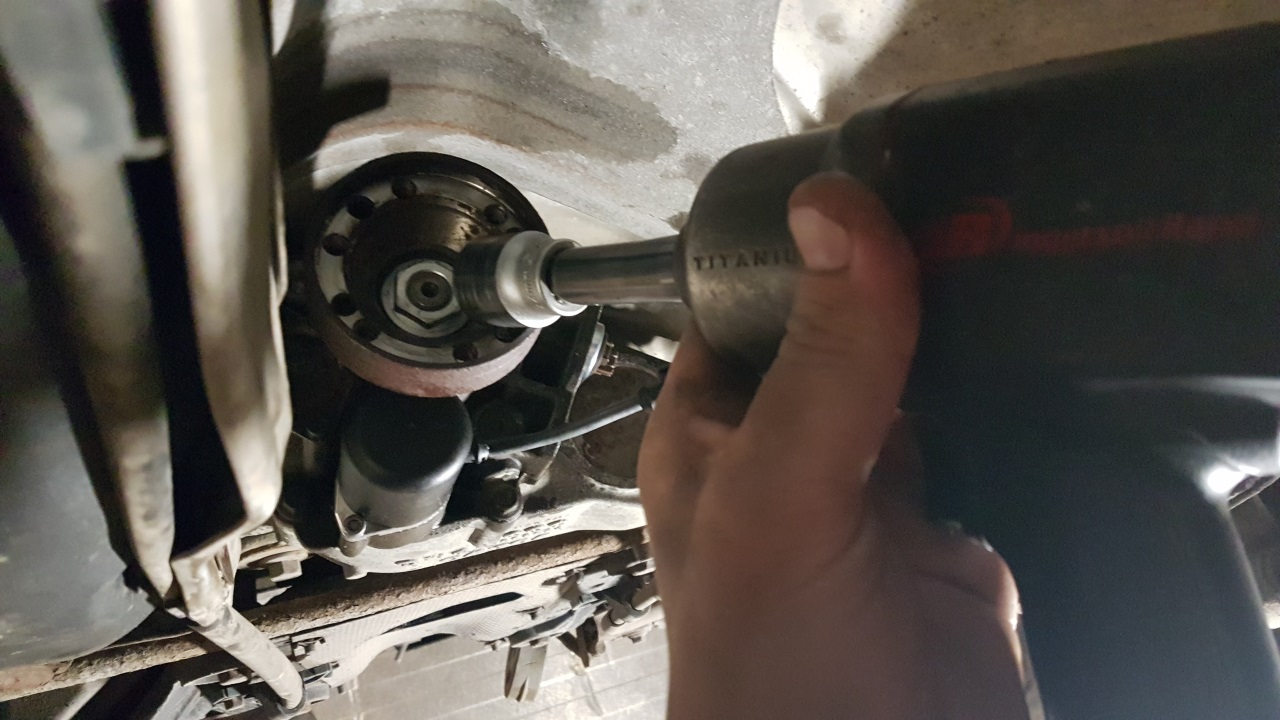
Ny pump på plats, fläns monterad och ”momentdragen” medelst mutterknack..
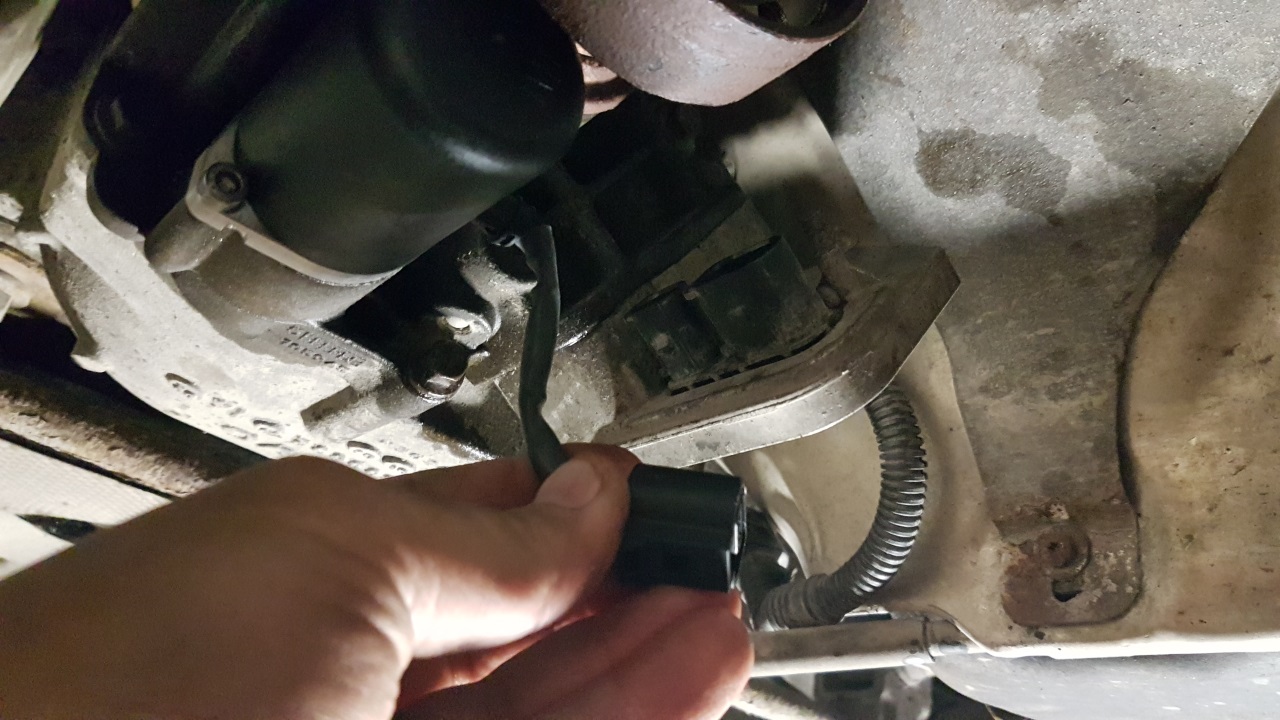
Elektronikstyrenhet återmonterad, kontakter kopplas i..
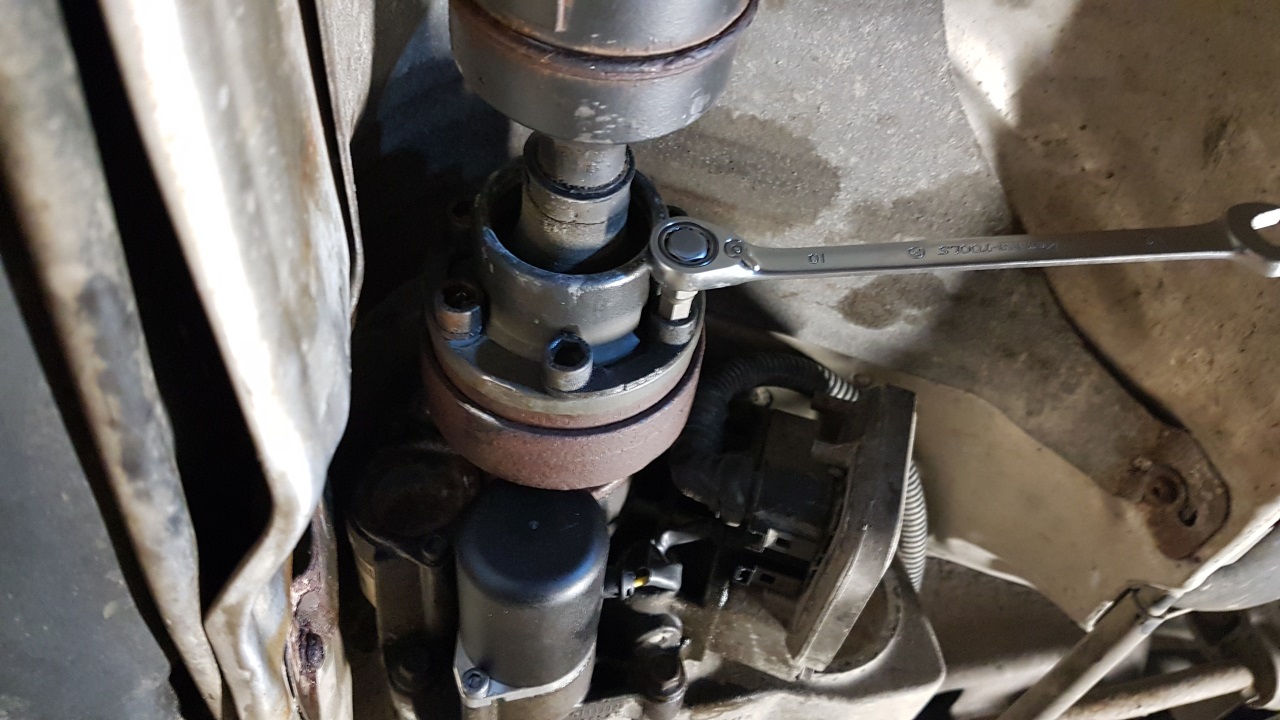
Kardanaxeln återmonteras med lämpling mängd gänglåsning på skruvarna, avgassystemet hängs upp, plåtarna under bilen återmonteras..
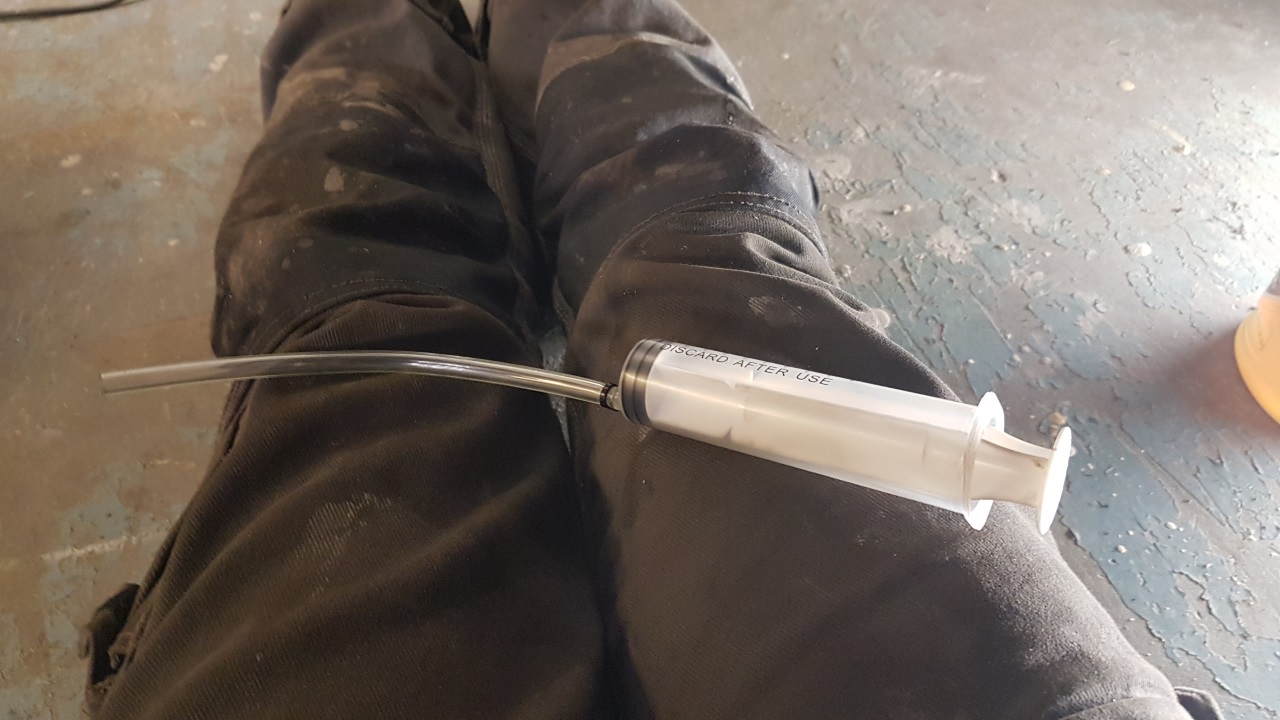
Sen gäller det att inte glömma att fylla upp haldexkopplingen med lämplig olja igen..
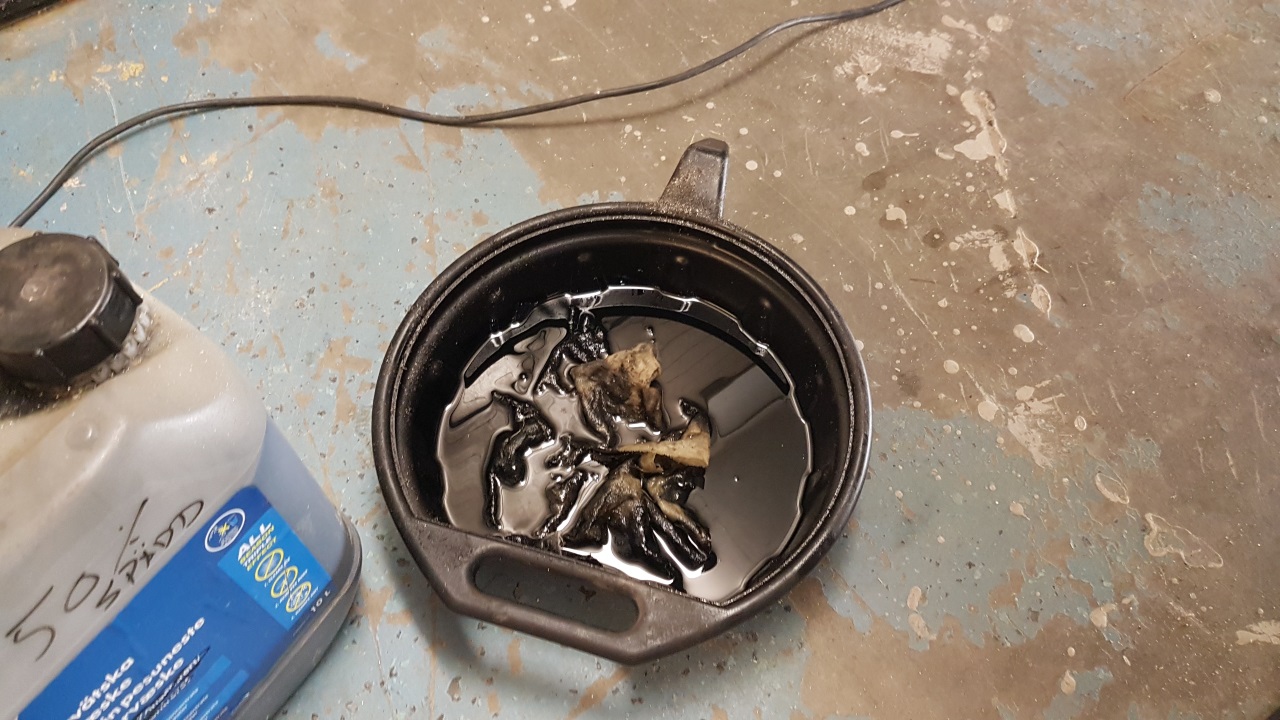
Den gamla oljan såg sådär ut, så det var läge att byta. Troligen är det även dags att byta olja i den främre vinkelväxeln, så nästa gång bilen är på lyften ska det göras!
.. och sen, sanningens ögonblick..
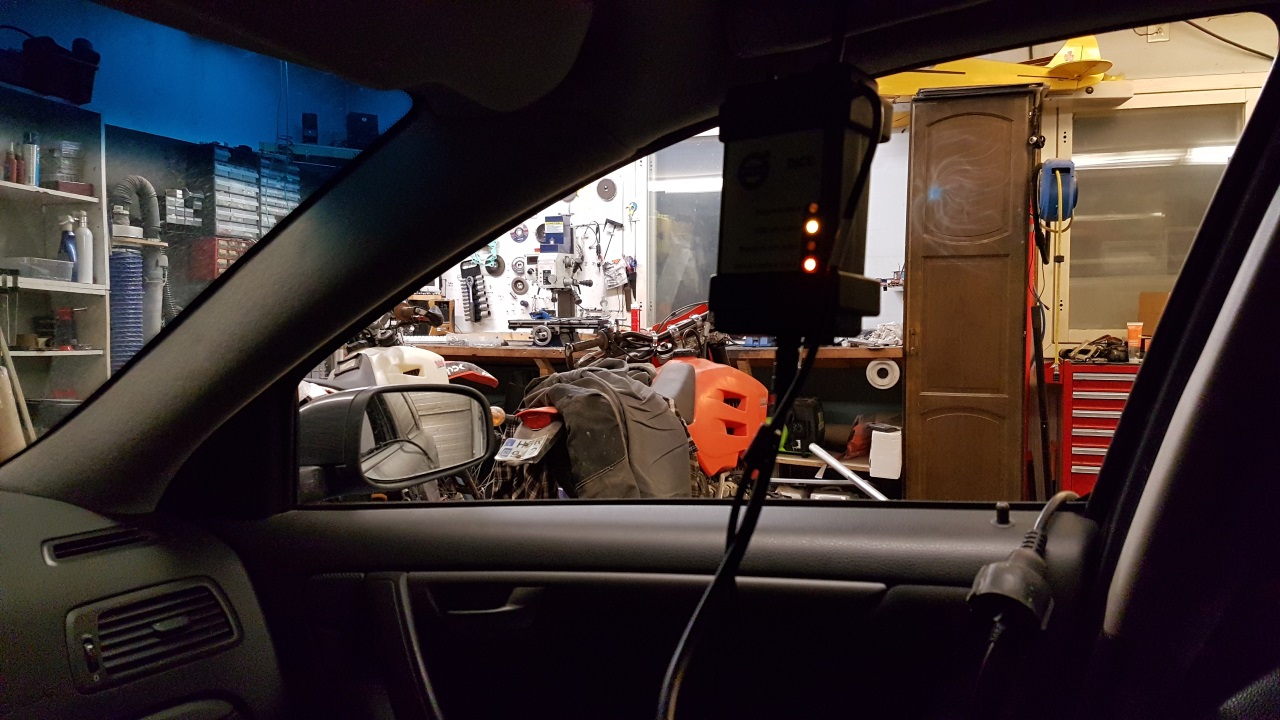
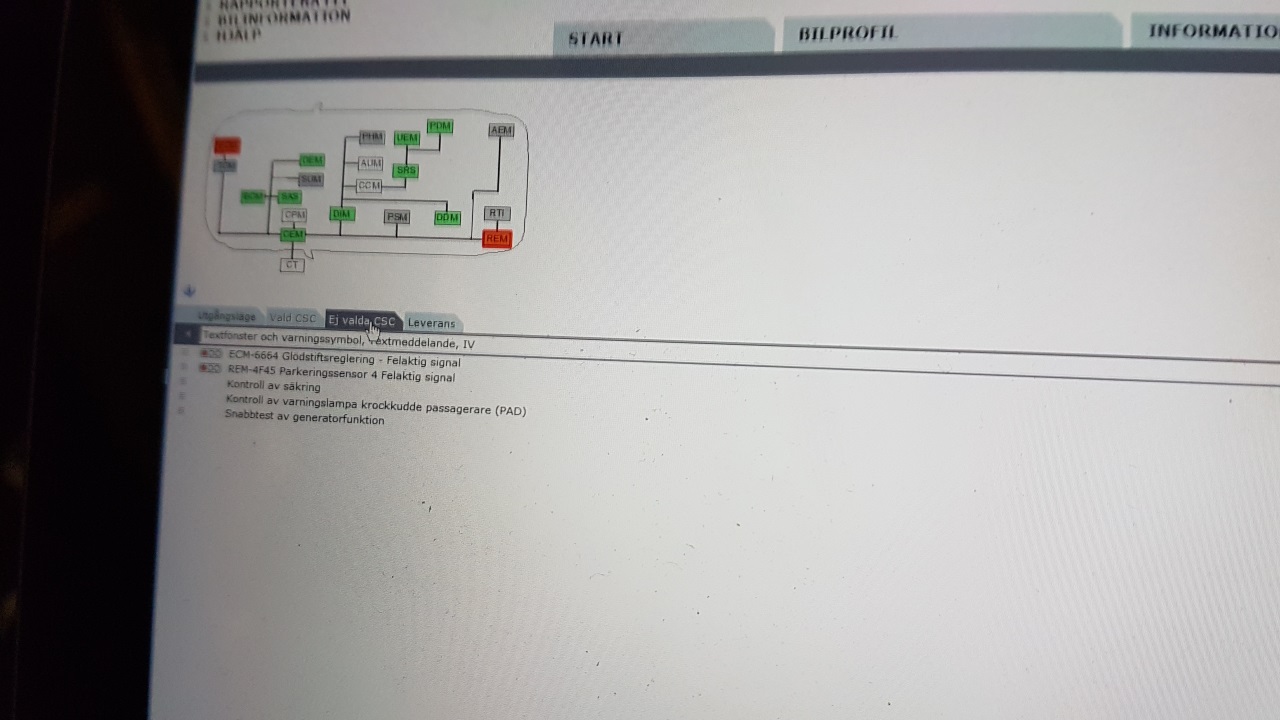
Rensade felkoderna, tog en testtur och sen såg det ut såhär.. Parkeringssensorn och glödstift har vi haft sedan tidigare, det ska åtgärdas men känns inte som någon panik. Det härliga här är att felkoderna om fyrhjulsdriften inte kom tillbaka! Dessutom fungerar fyrhjulsdriften, antisladd och antispinn, vilket gör en ohygglig skillnad på de snorhala höstvägarna vi har nu.
Summa summarum: 2500kr i delar, och en halvdags arbete..
Resultat: Sinnesfrid