Kategoriarkiv: RunBike_v1
Bike season closing in
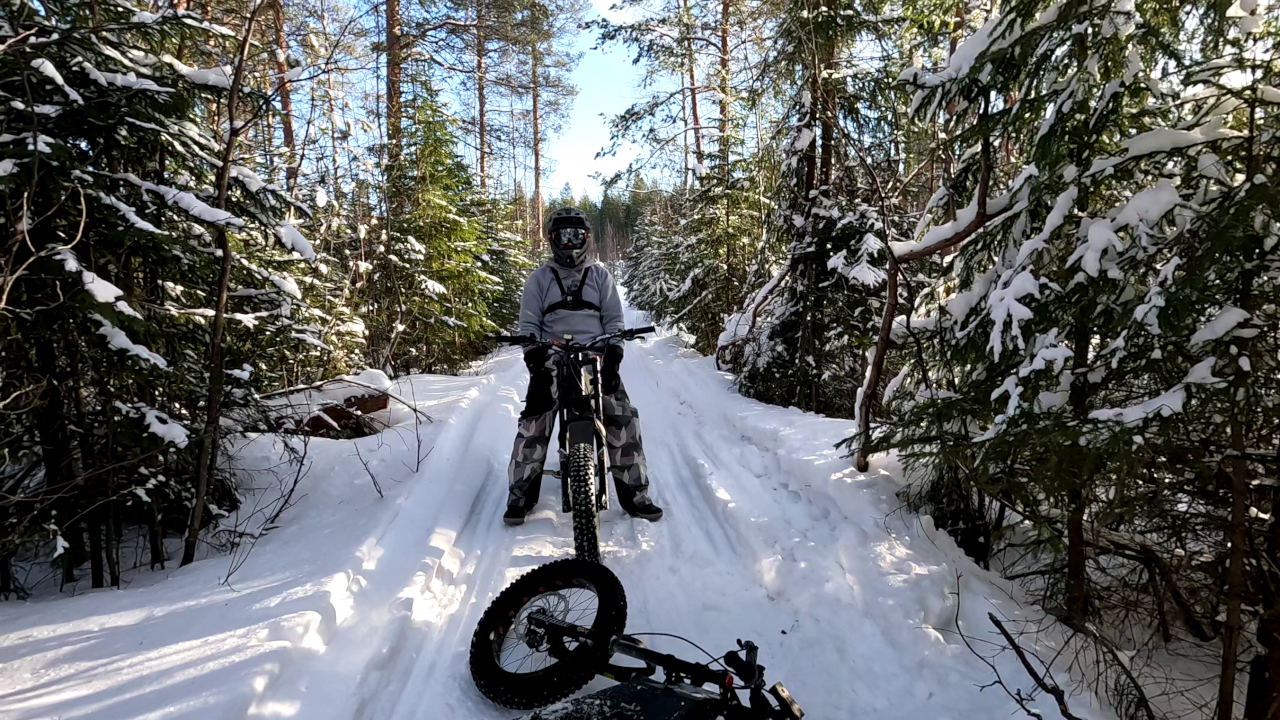
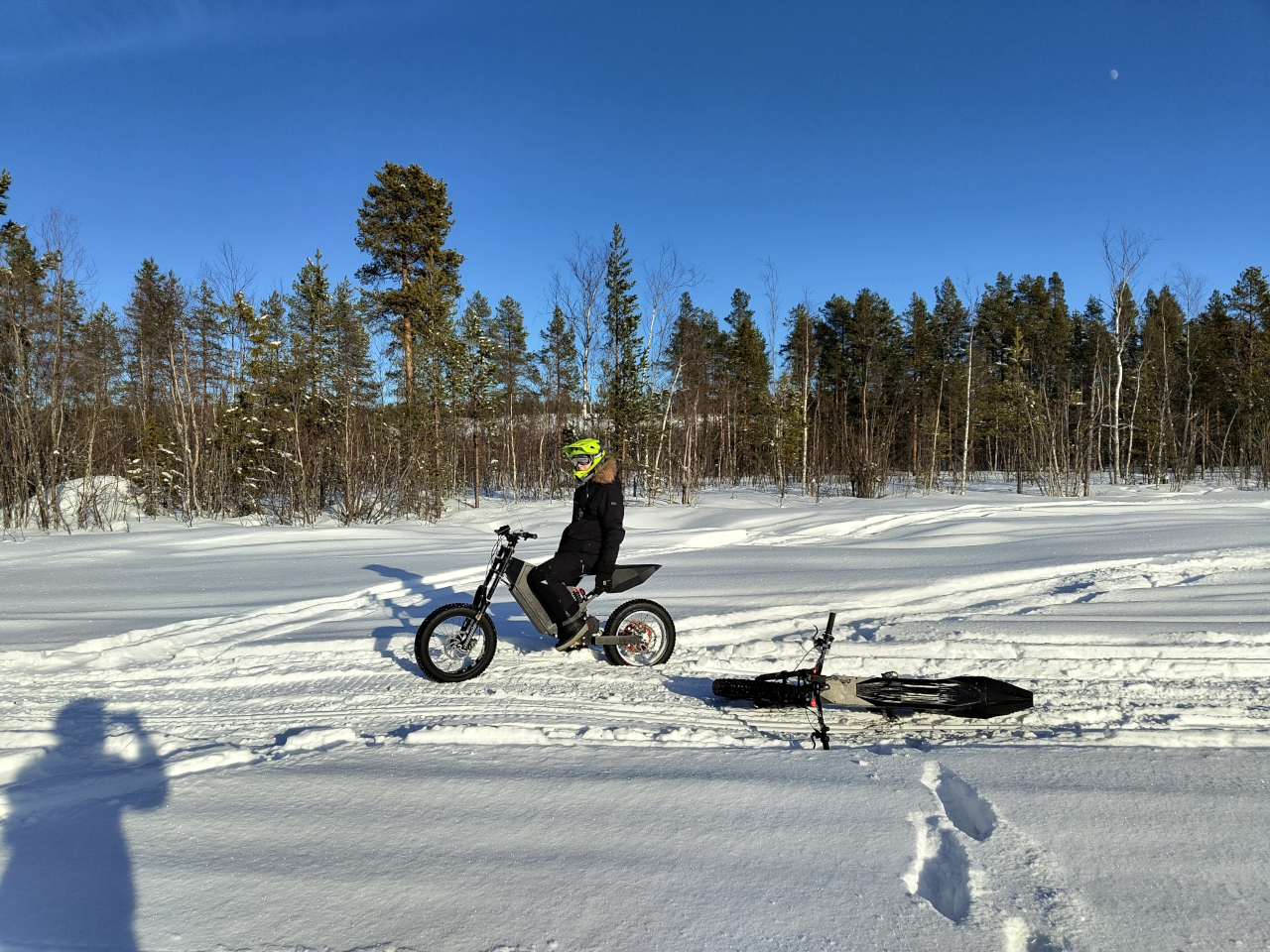
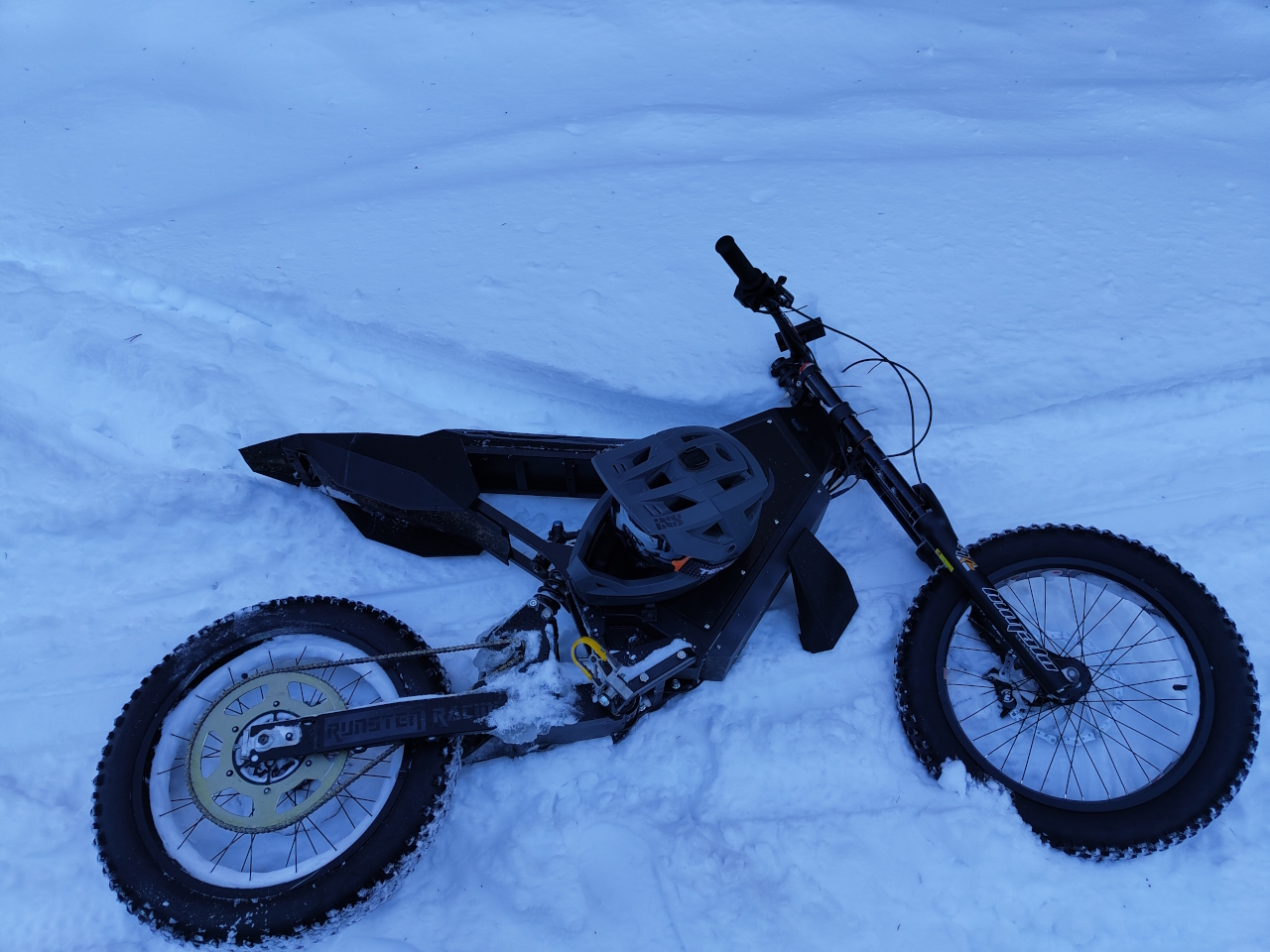
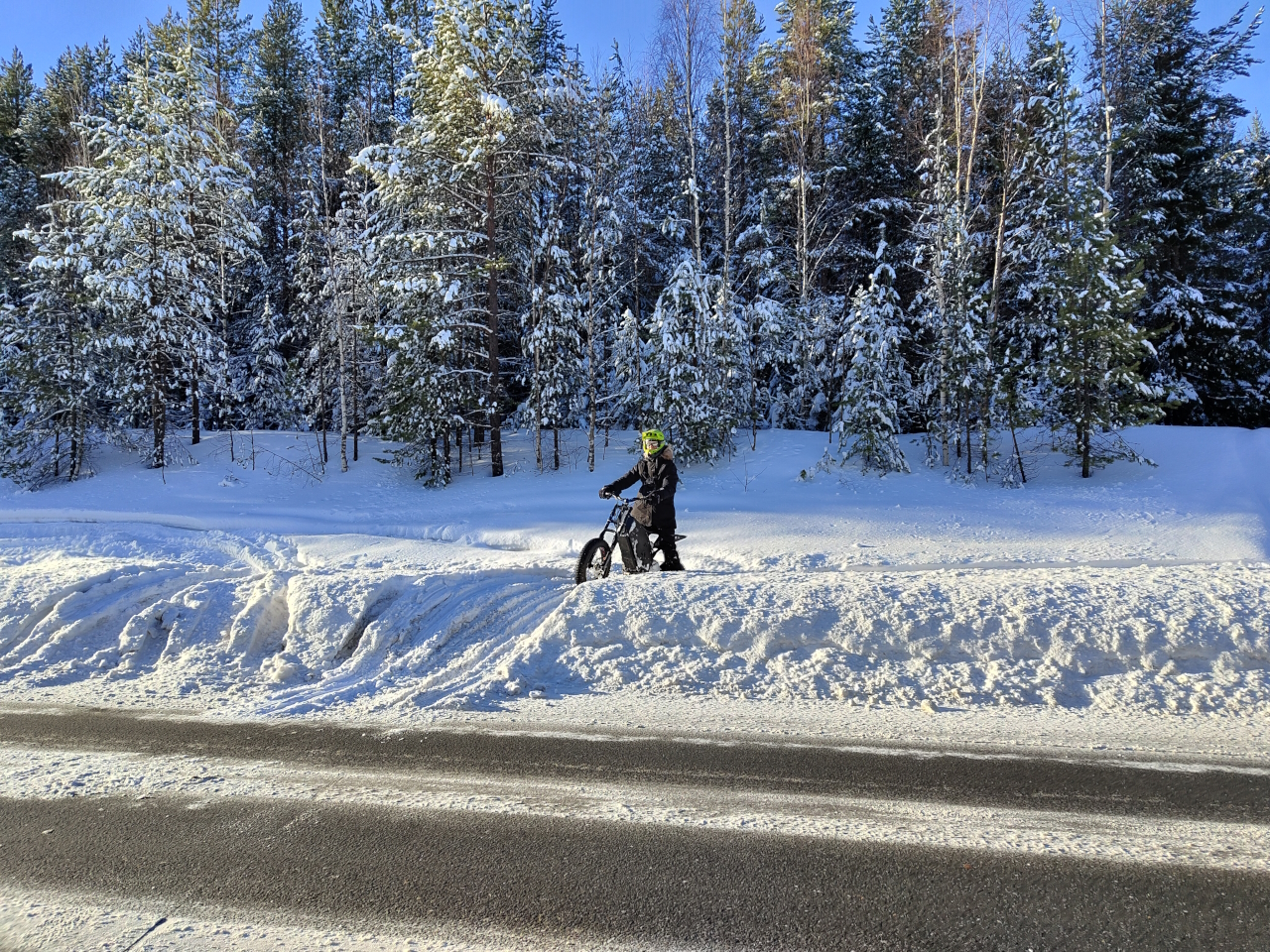
Super nice to start riding again, let’s hope for a great spring this year and loads of riding!
The second bike, progress
So, the footpegs I put on the bike were cheap, but not awesome..
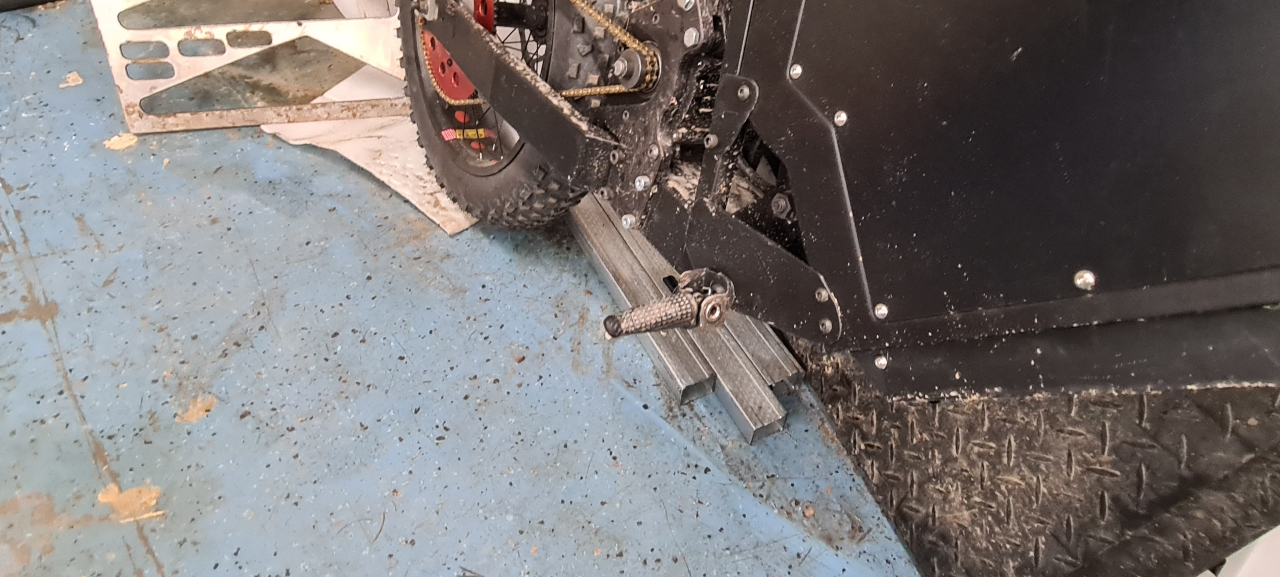
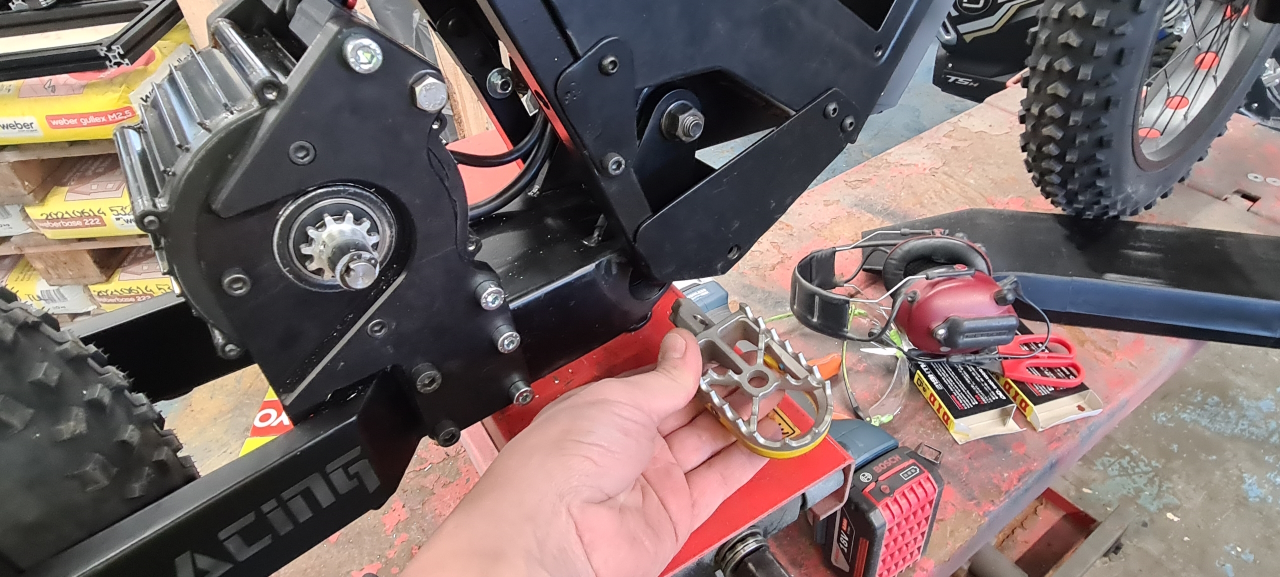
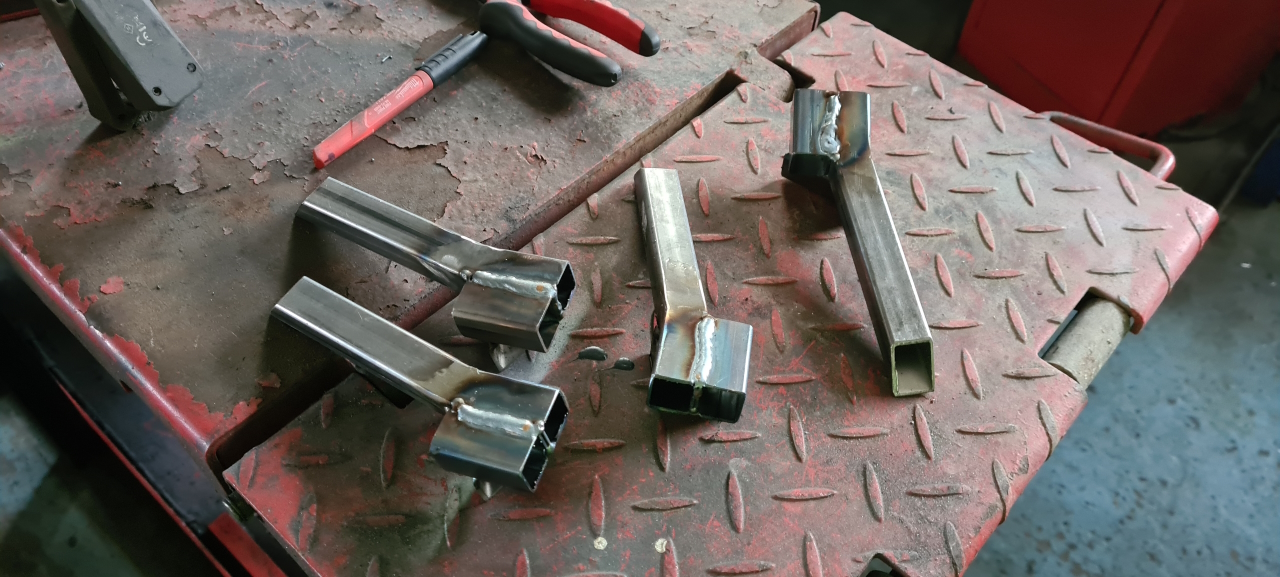
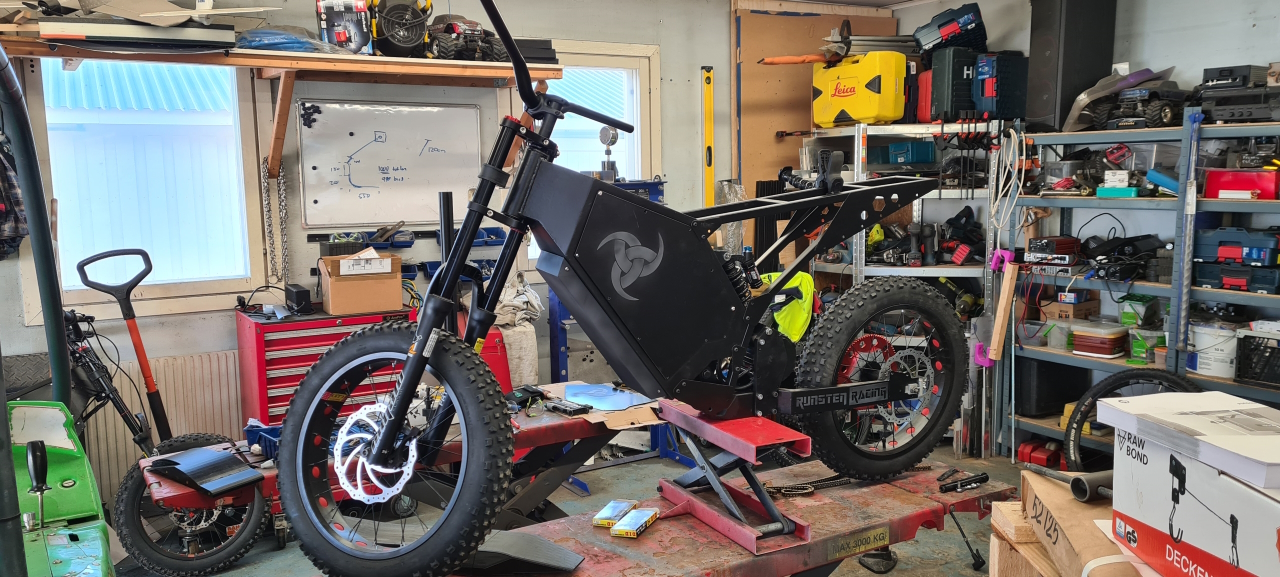
Also, I made stickers since I kind of like the black/grey color scheme.. What do you think?
When the bike is finished I’ll post a youtube video of the entire build. I’ve also got a lot of questions about what components I’m using and the total cost for the build. I guess I’ll put a BOM together and take on the dreaded task of figuring out how much $$$ these two bikes have cost me.. :/
To be continued..
Finishing steps and final assembly
So, after finishing the sand blasting of the frames we took a break and celebrated easter in the cabin with some nice snowmobiling and relaxing.
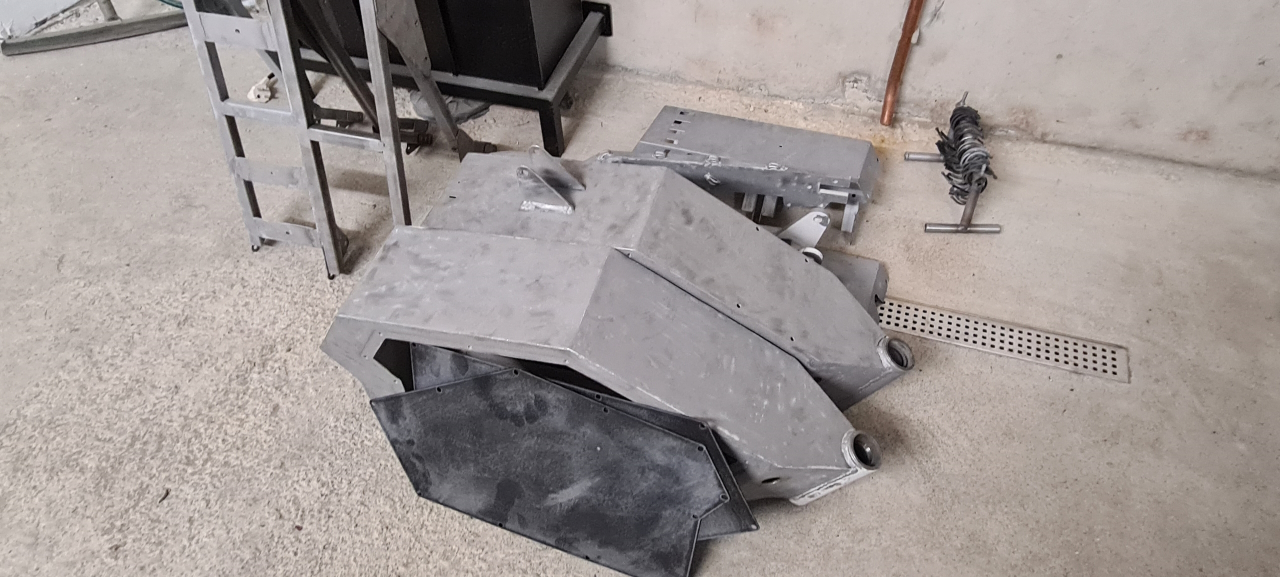
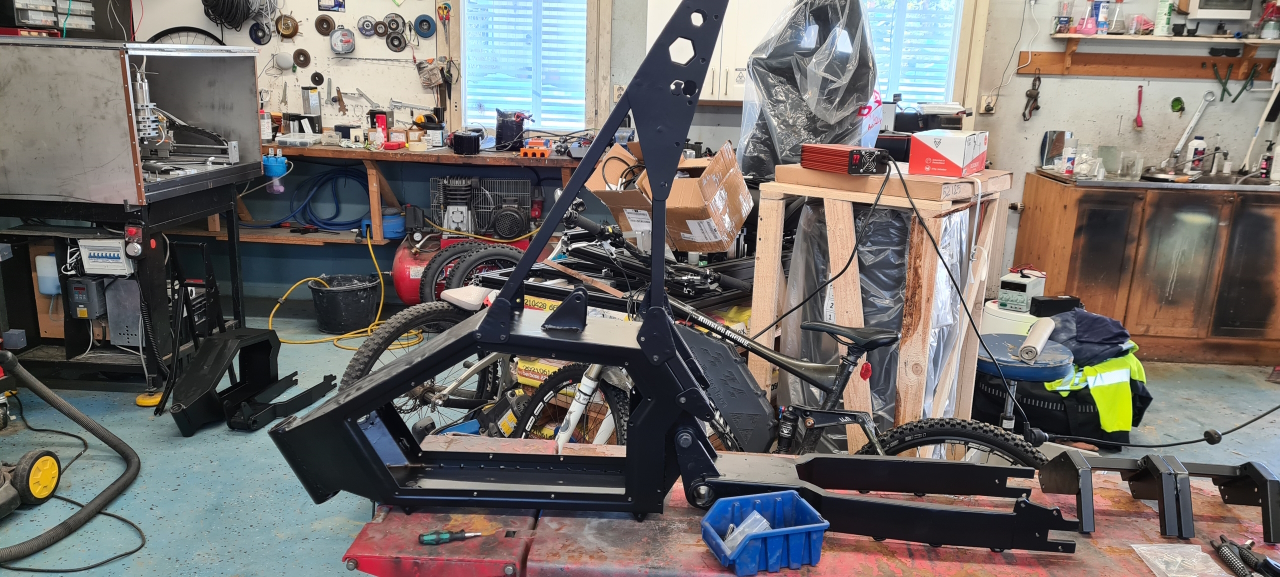
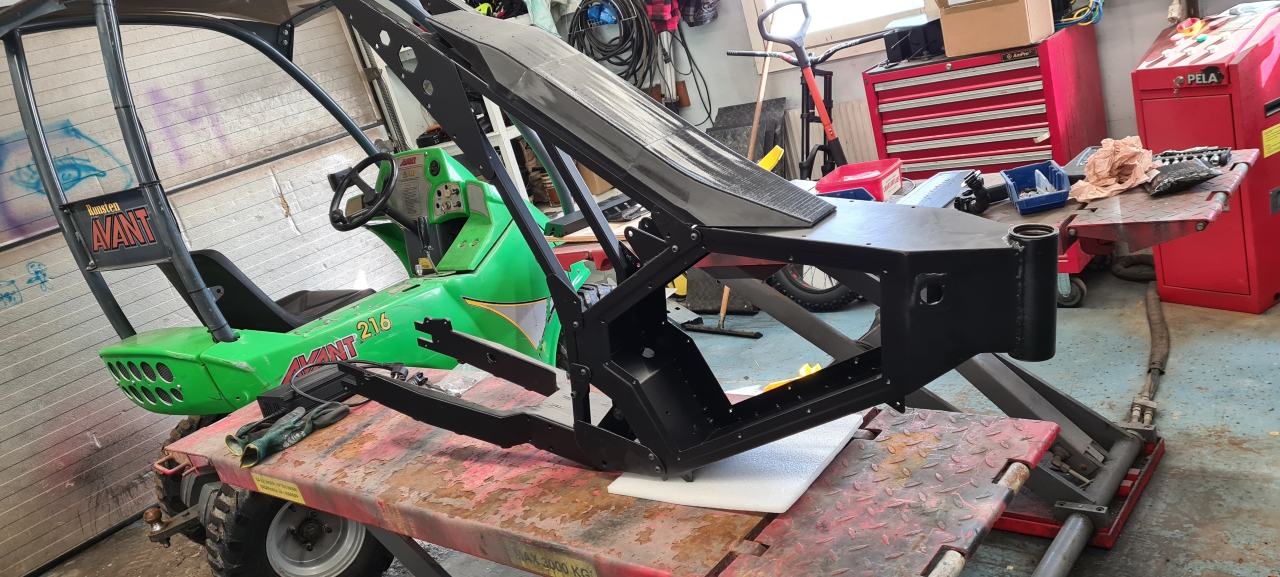
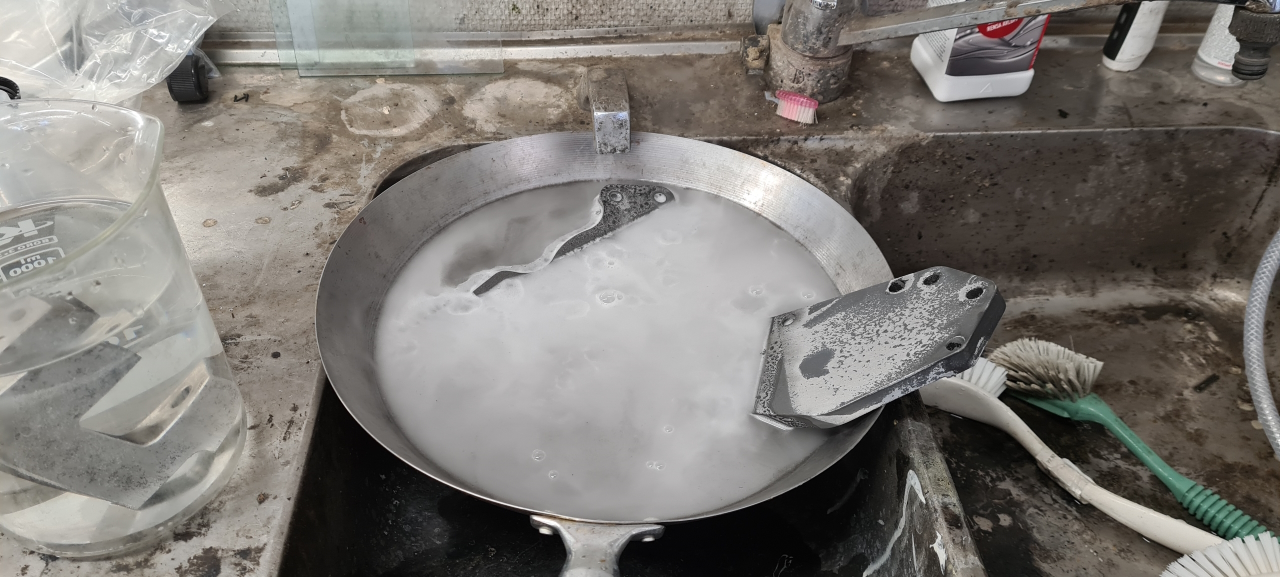
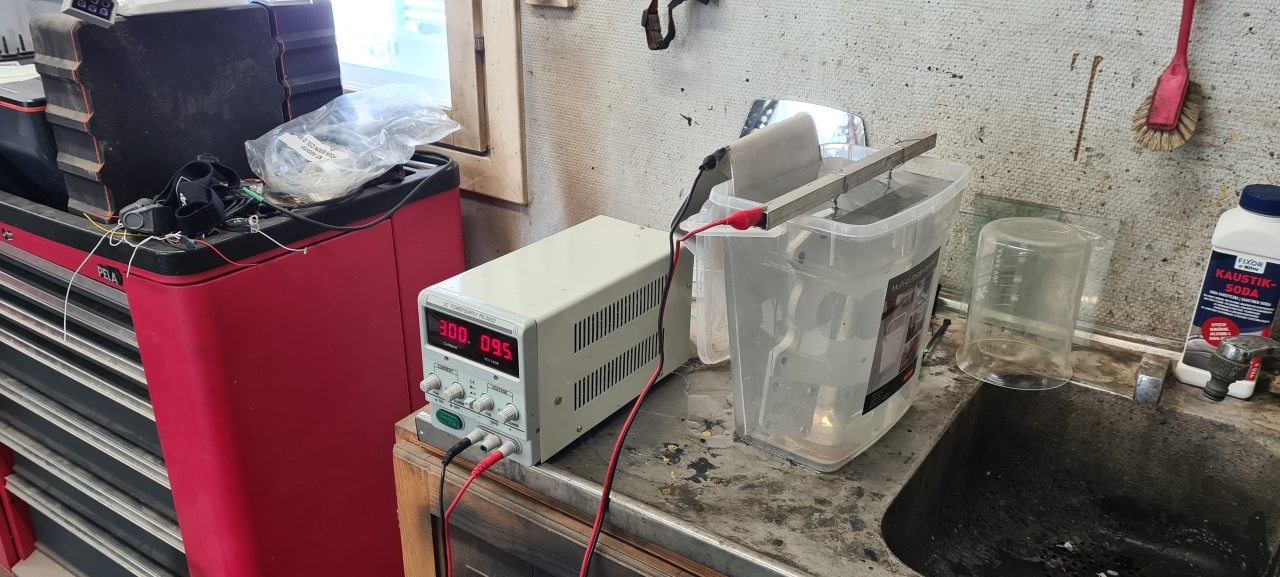
Since I wanted a thick uniform layer of color I let the parts anodize for about an hour at quite low amperage. The required current depends on the surface area of the part to be anodized but I usually kind of just guess and mostly it turns out OK. If not I’ll just redo the process from the lye bath and try again with different settings. =)
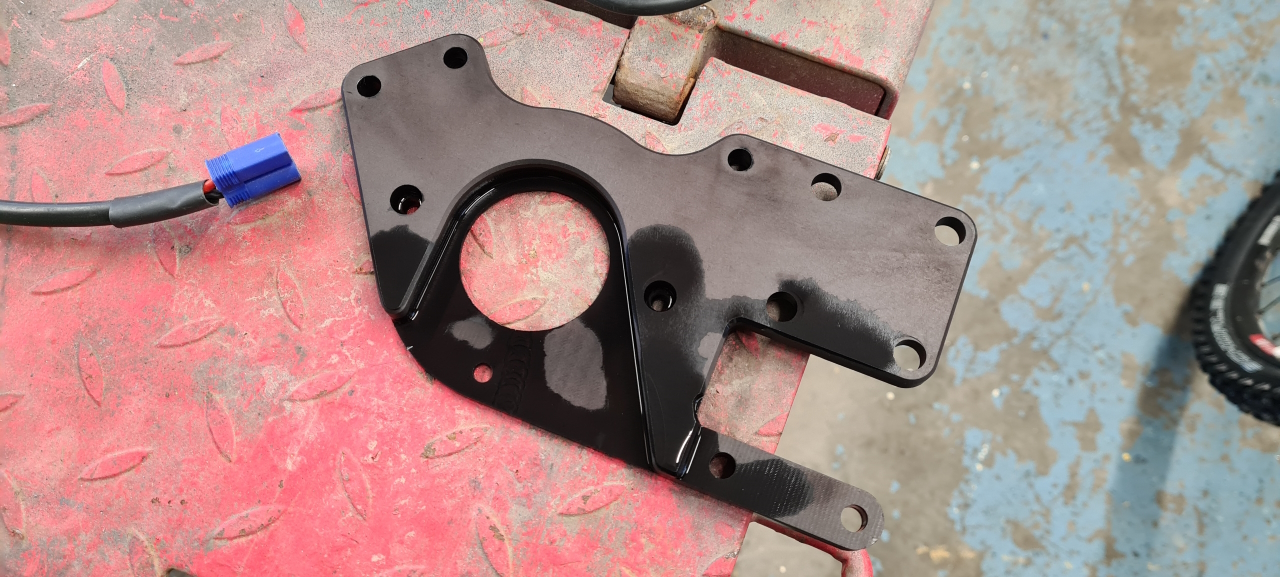
To seal the porous oxide layer the parts are boiled for about 15 minutes – again depending on the properties of the oxide layer and so on. I’ve precviously had the water wash some of the dye out of the part so now I boil the parts while still in the dye bath.
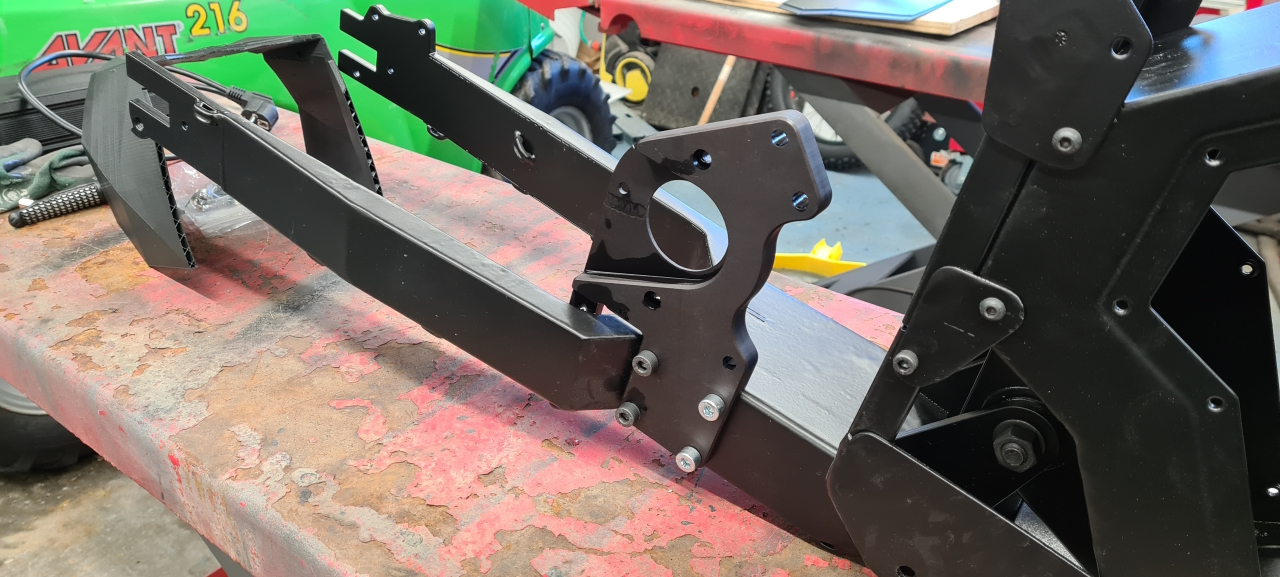
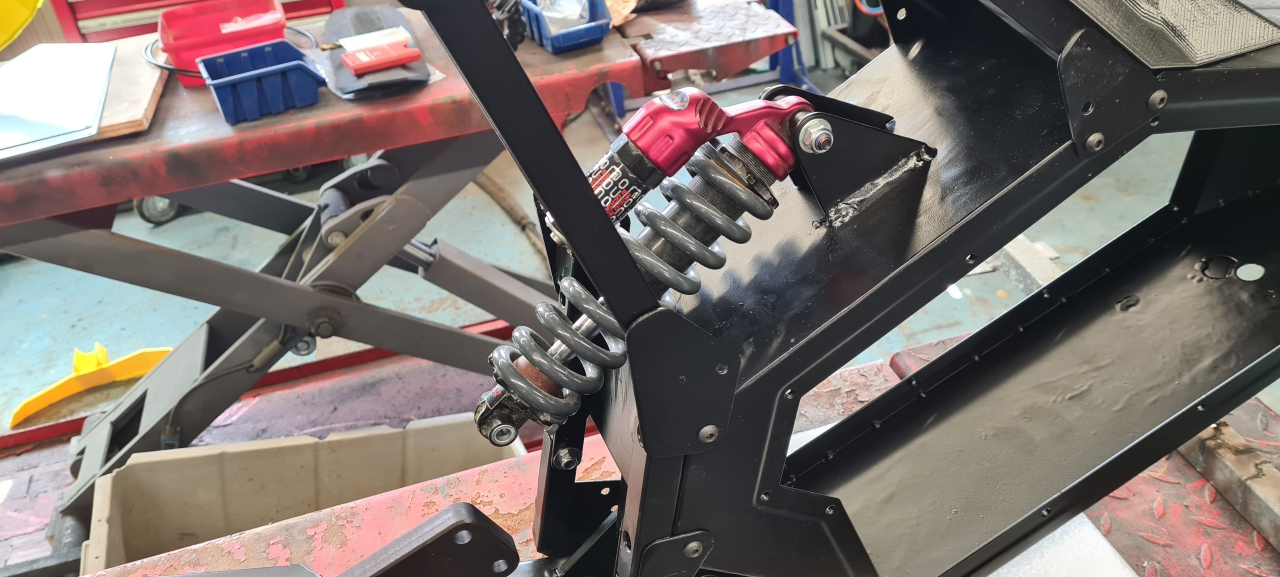
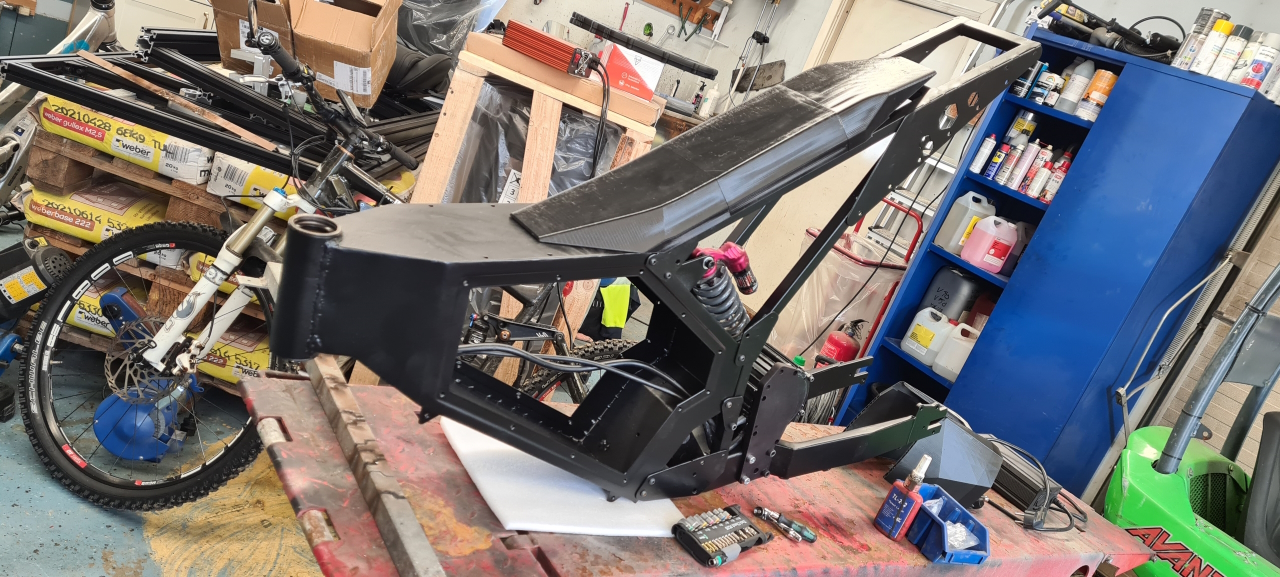
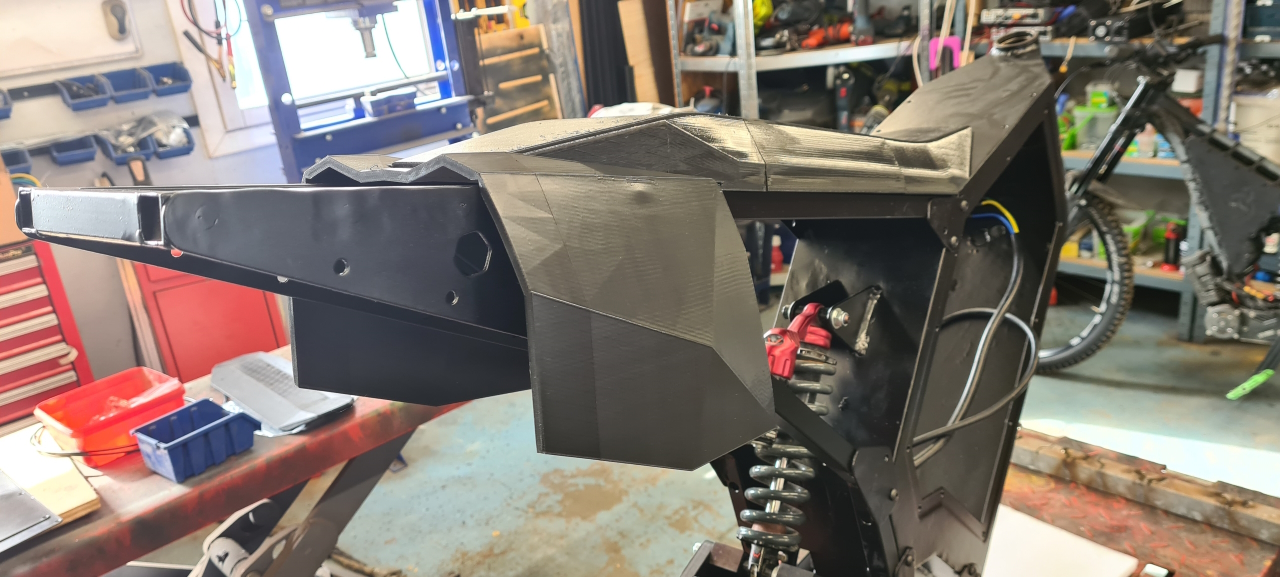
This was to be able to test the fit of the 3d printed rear fender, which was too small and required a couple more prototypes before I had a good fit.
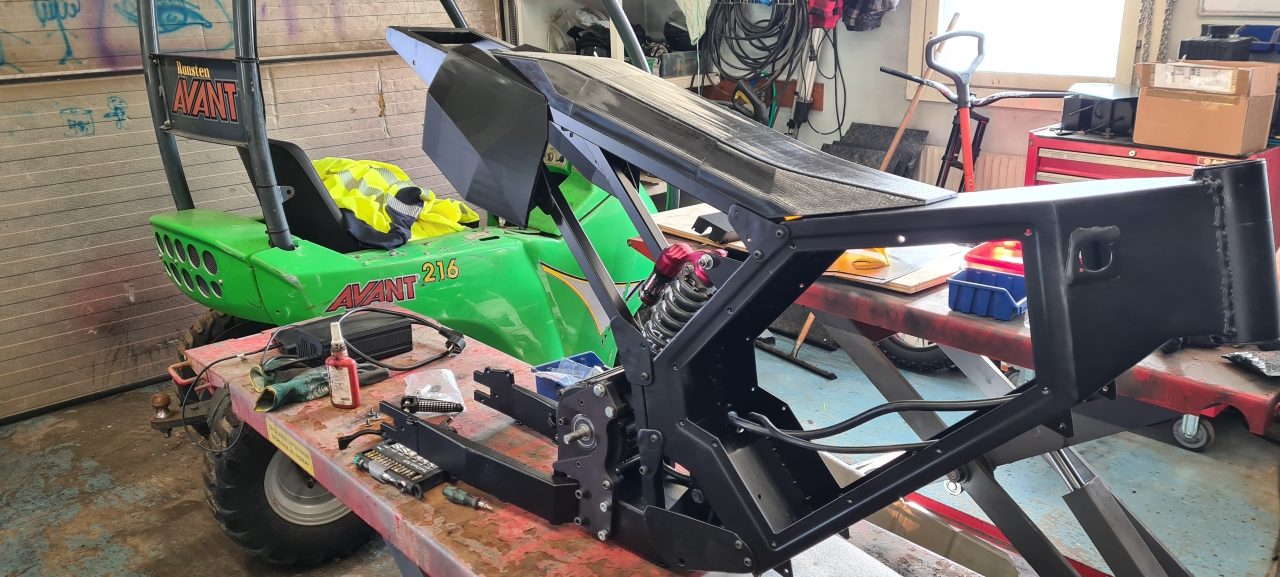
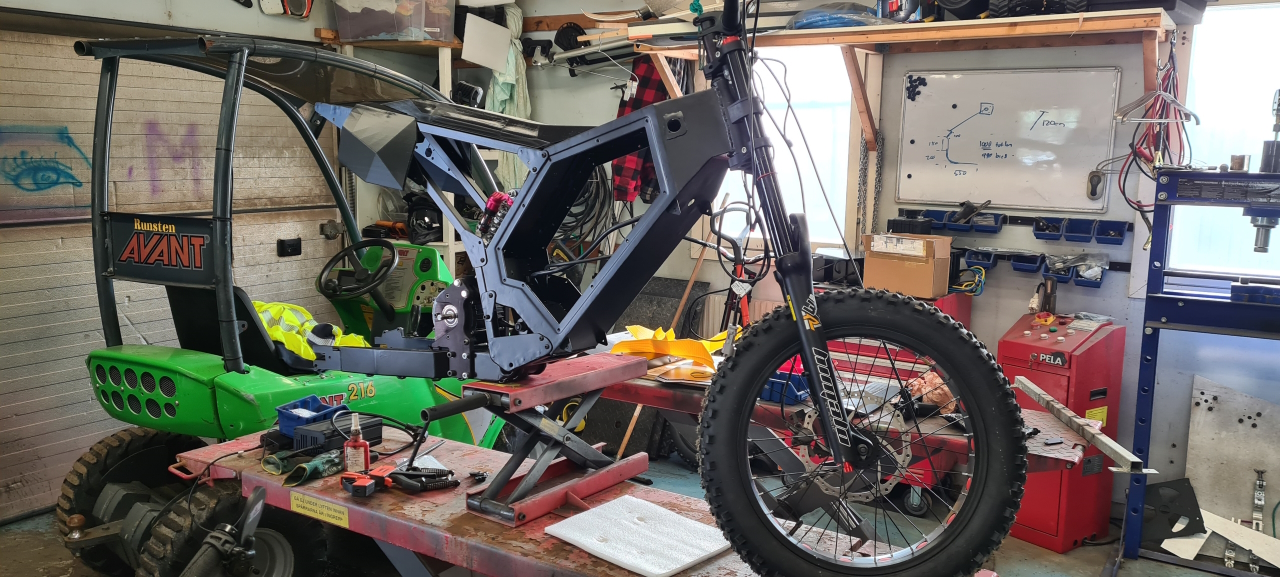
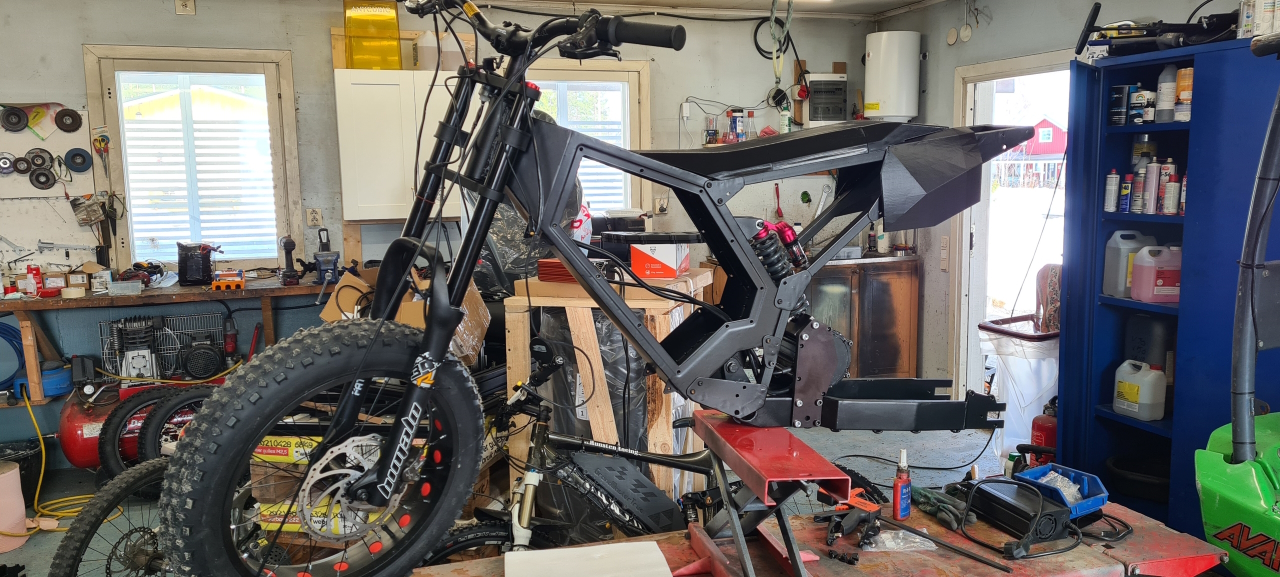
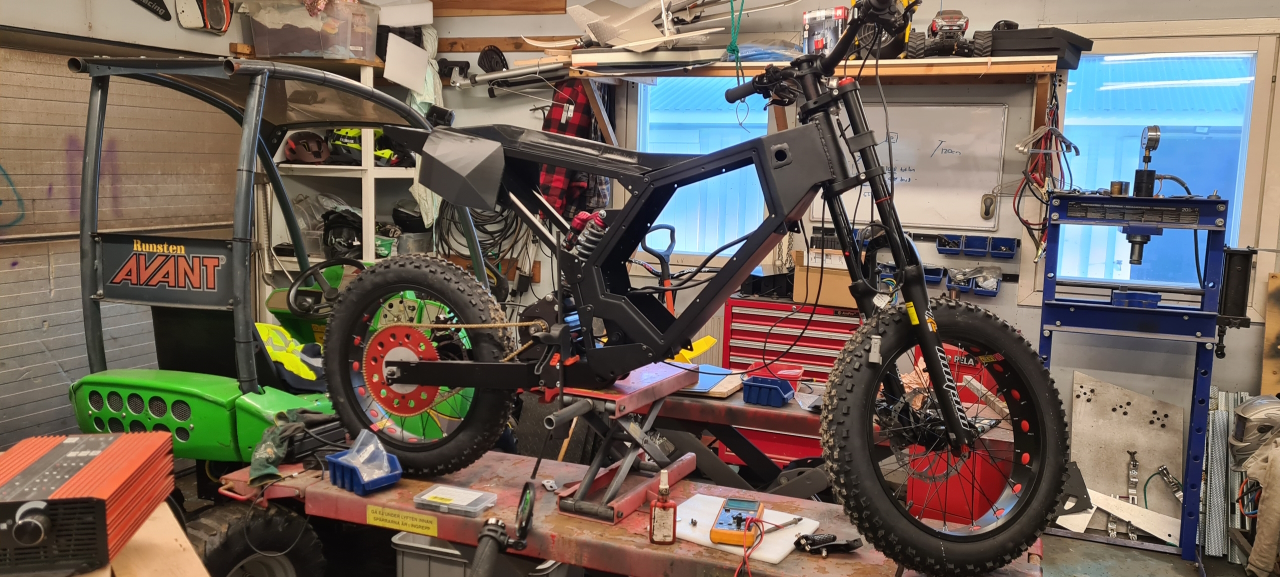
Rear wheel, chain and so on..
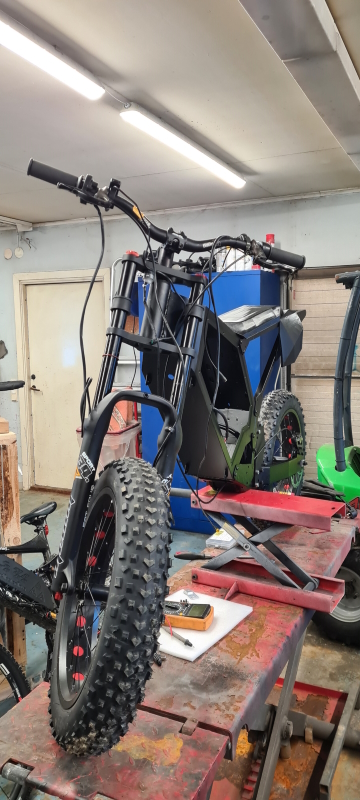
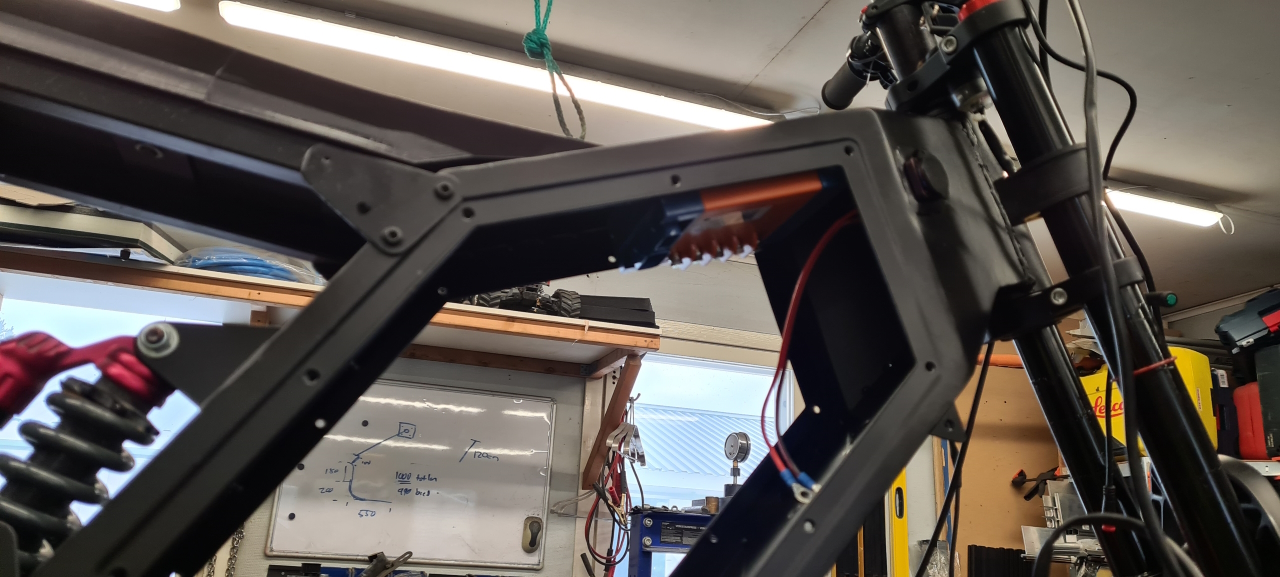
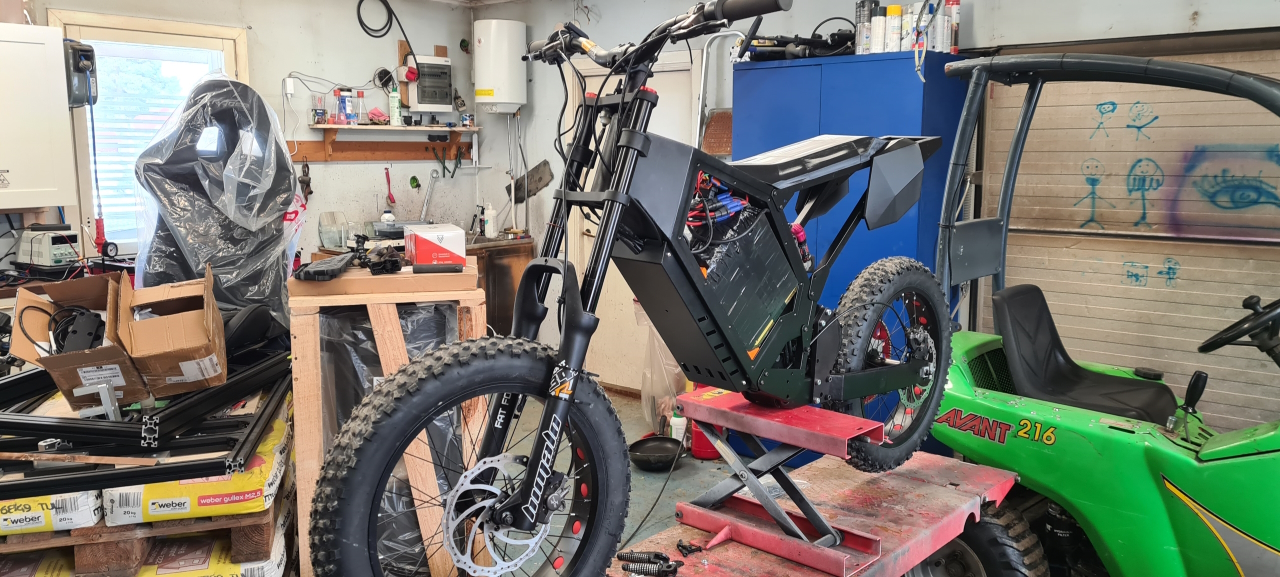
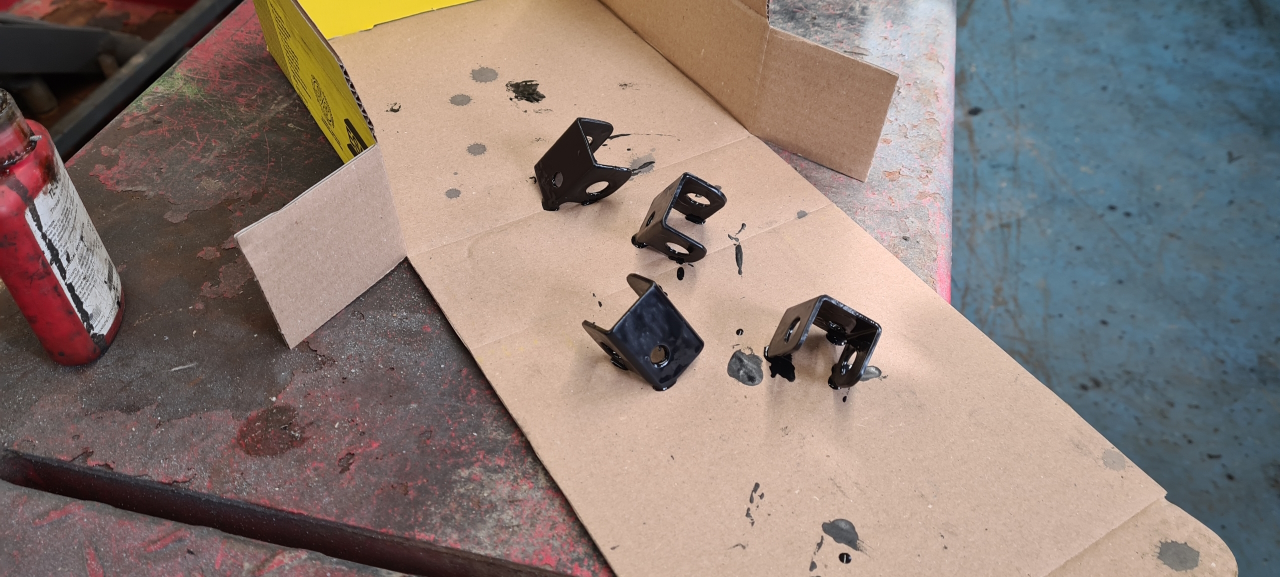
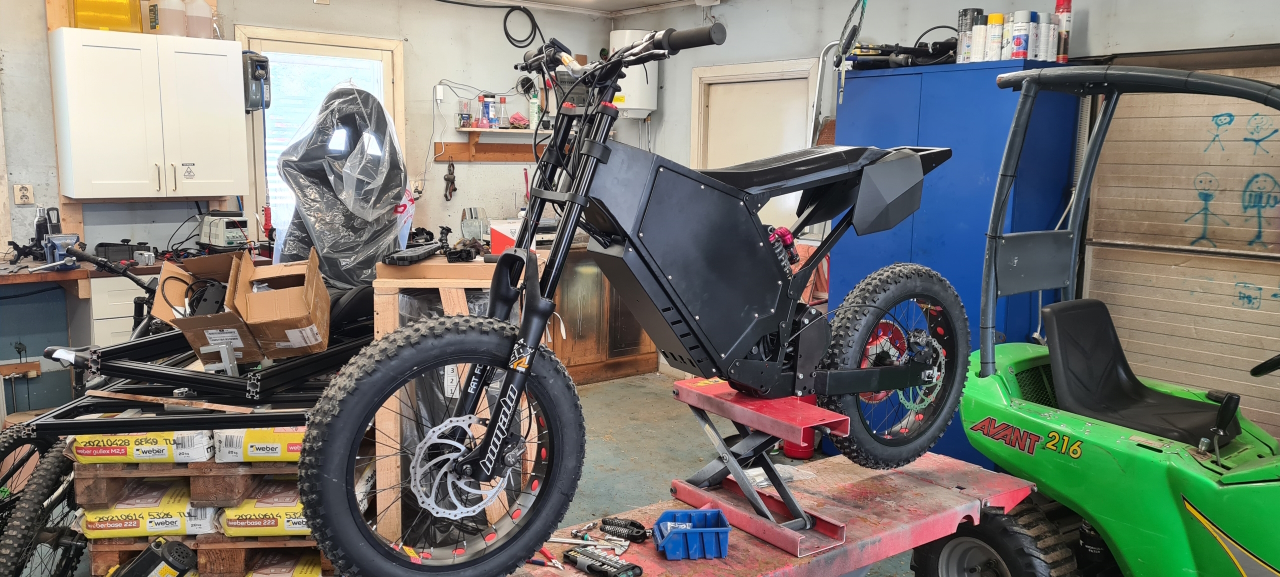
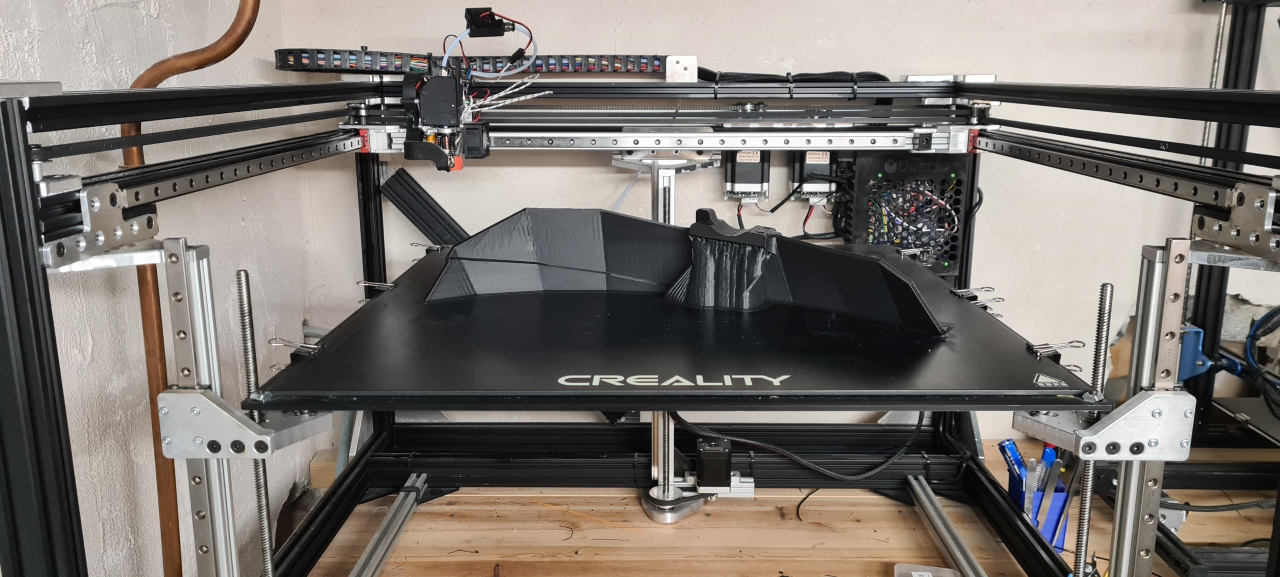
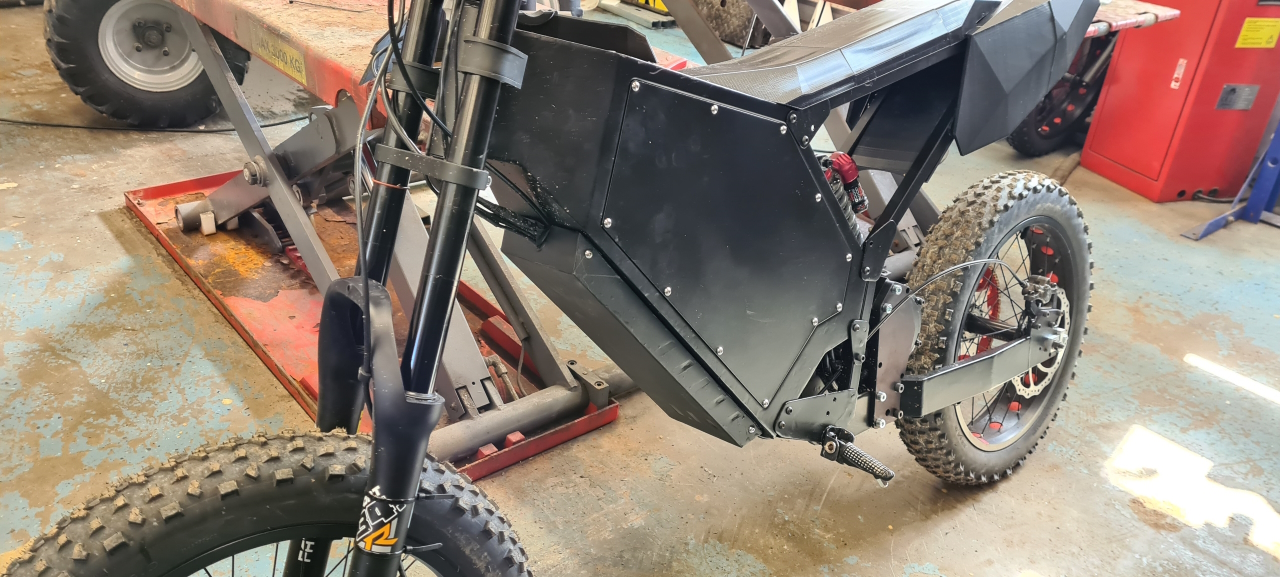
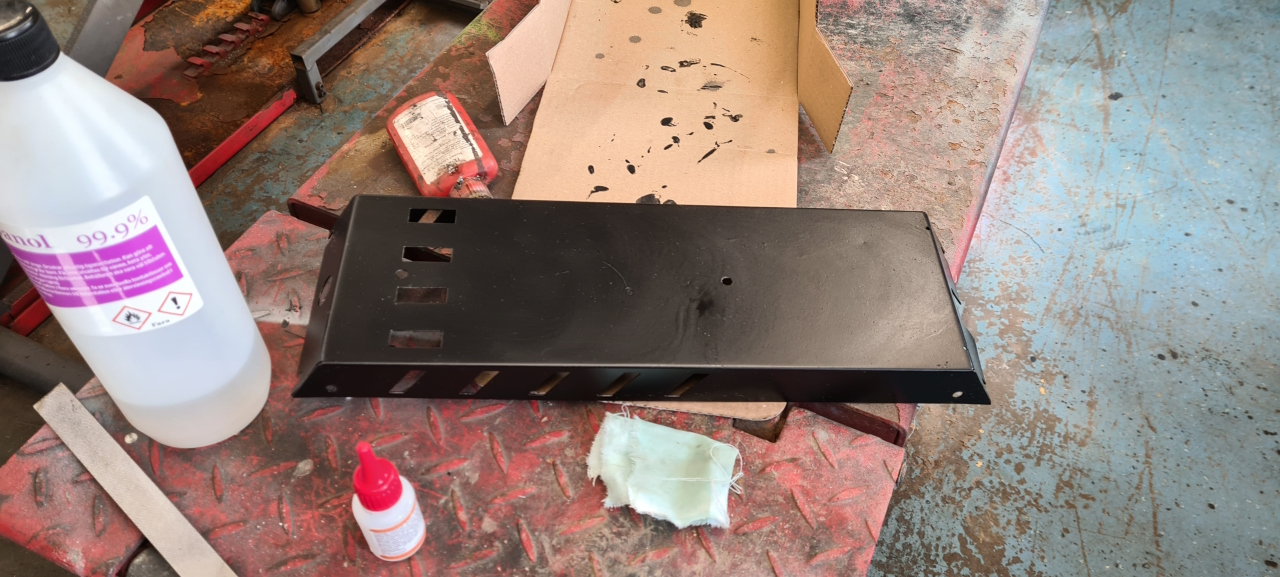
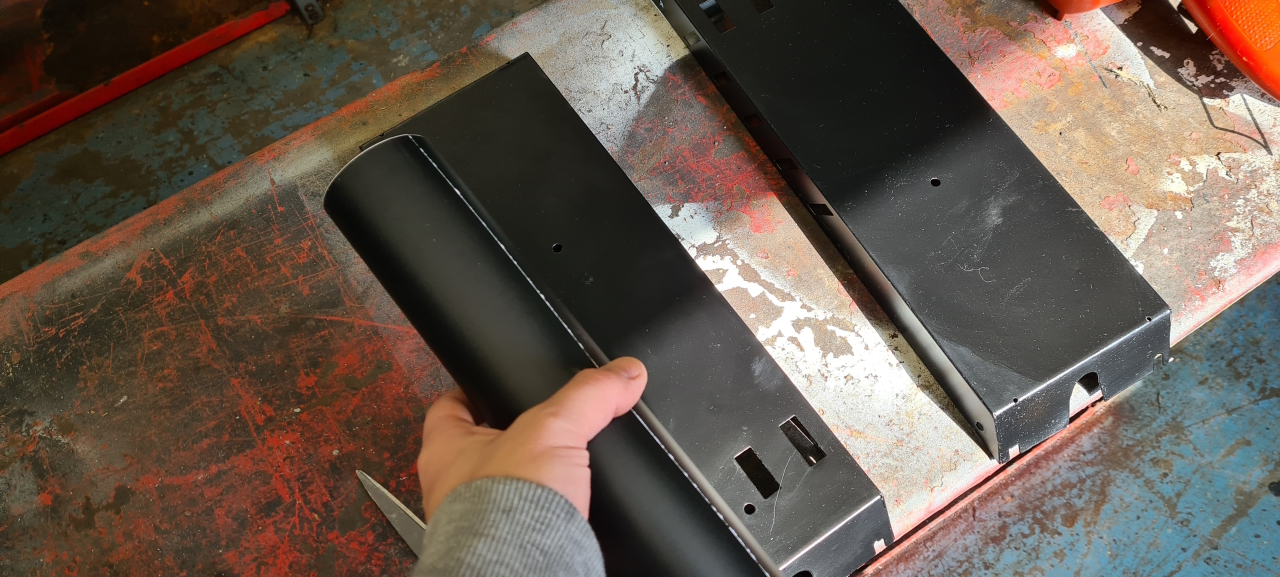
Instead, for the time being, I wrapped the cable cover box in protective vinyl wrap. This’ll make it less sensitive to flying pebbles and sand.
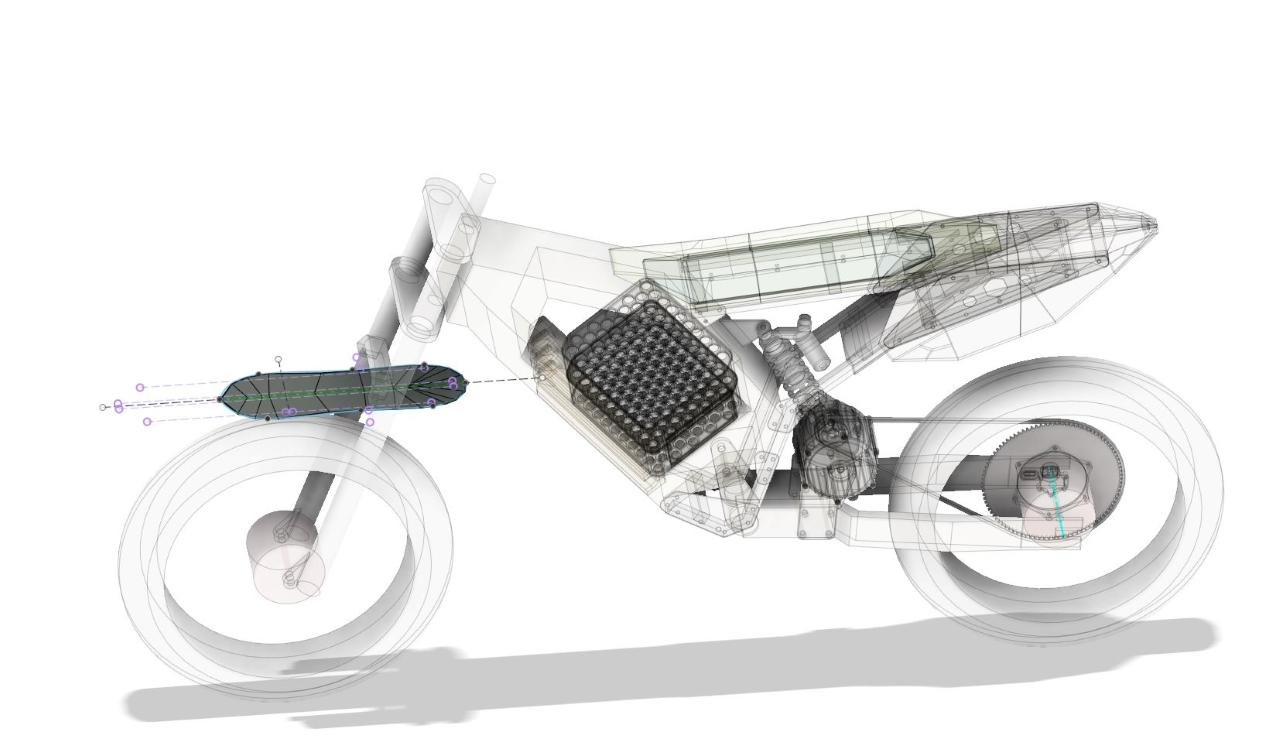
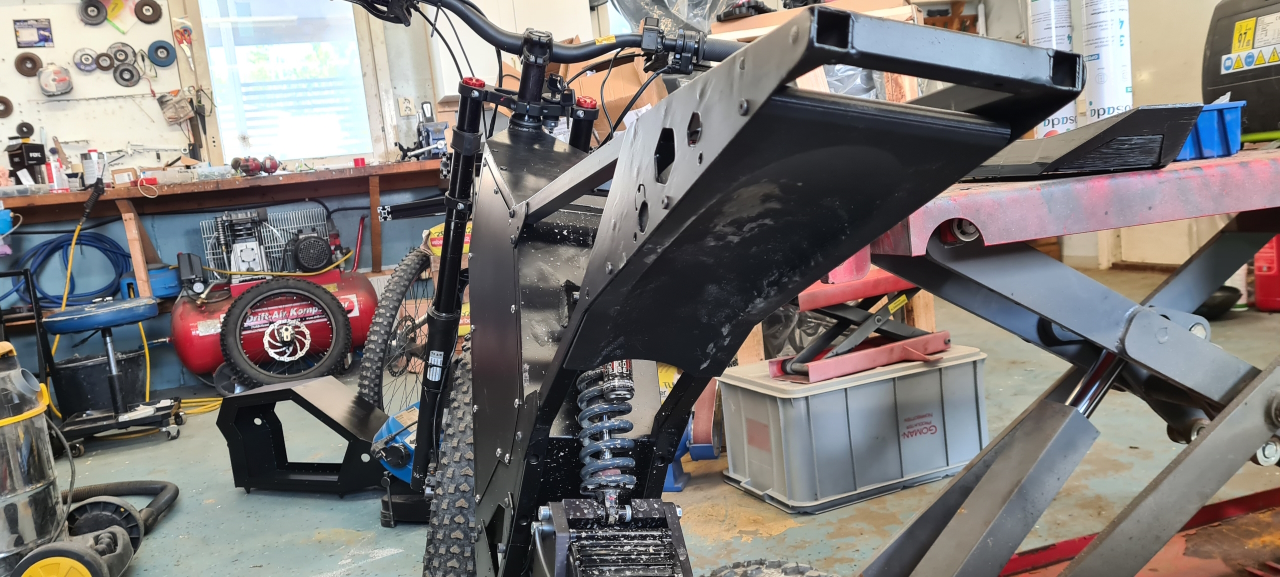
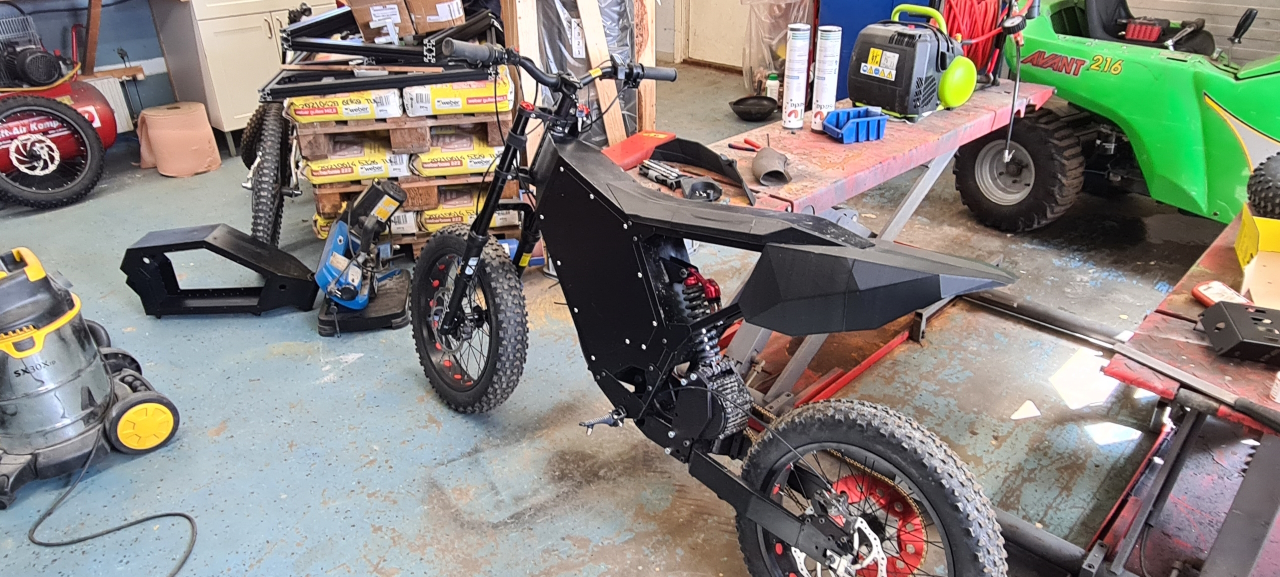
Re-assembly of motor and frame preparation
So, since the magnets in the rotor was super strong I’ve been a bit nervous about re-assembling the motor, but I got an idea..
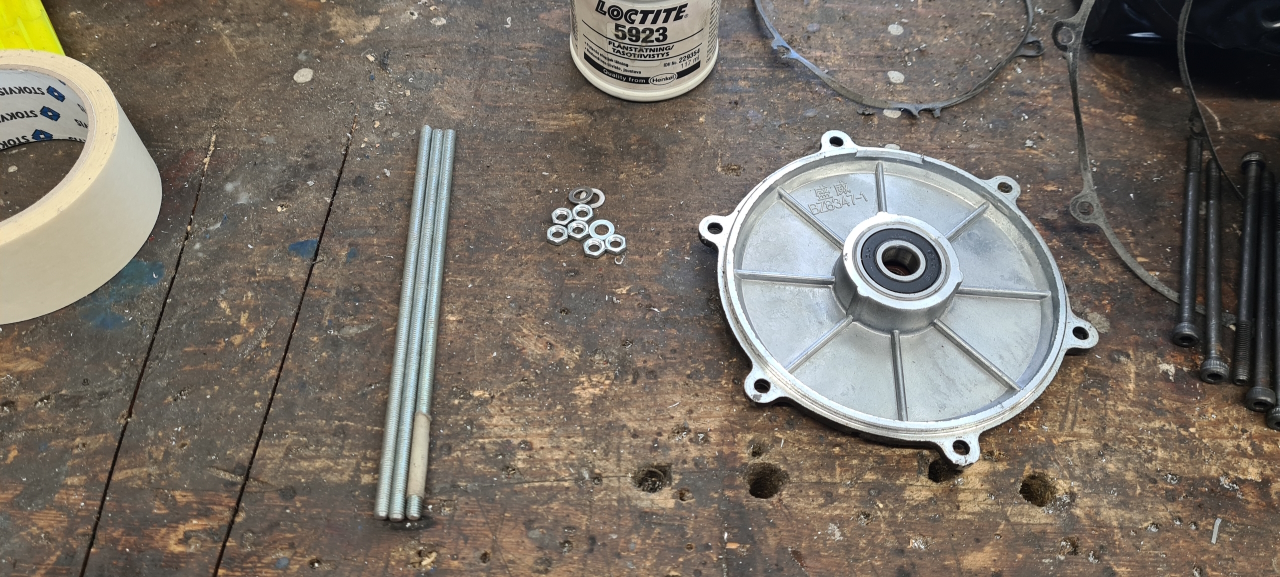
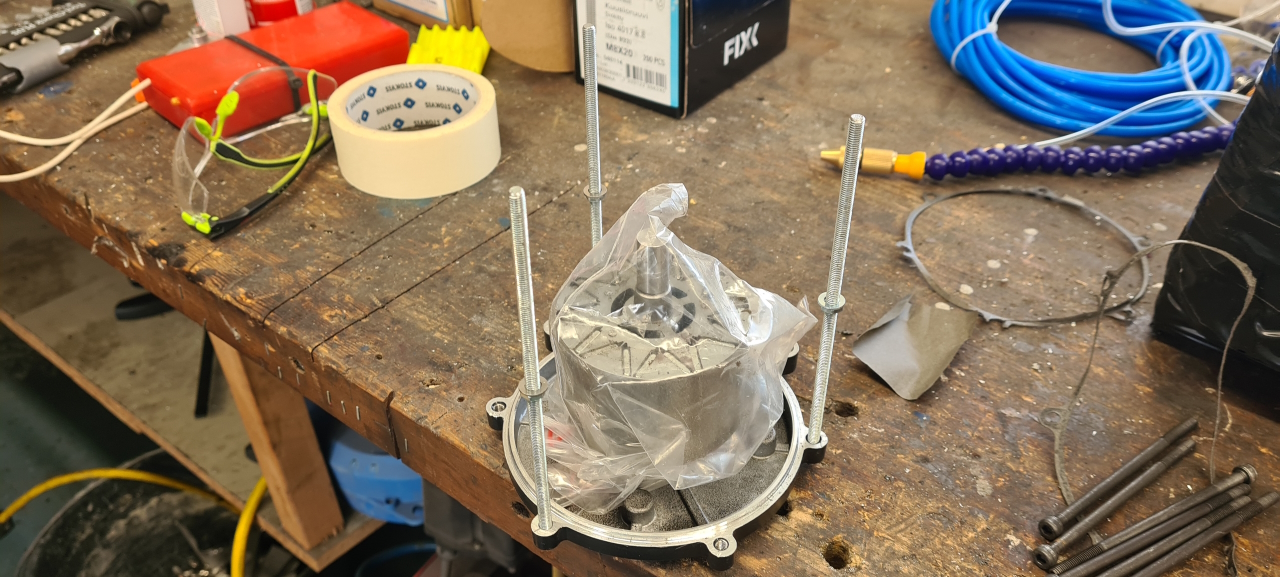
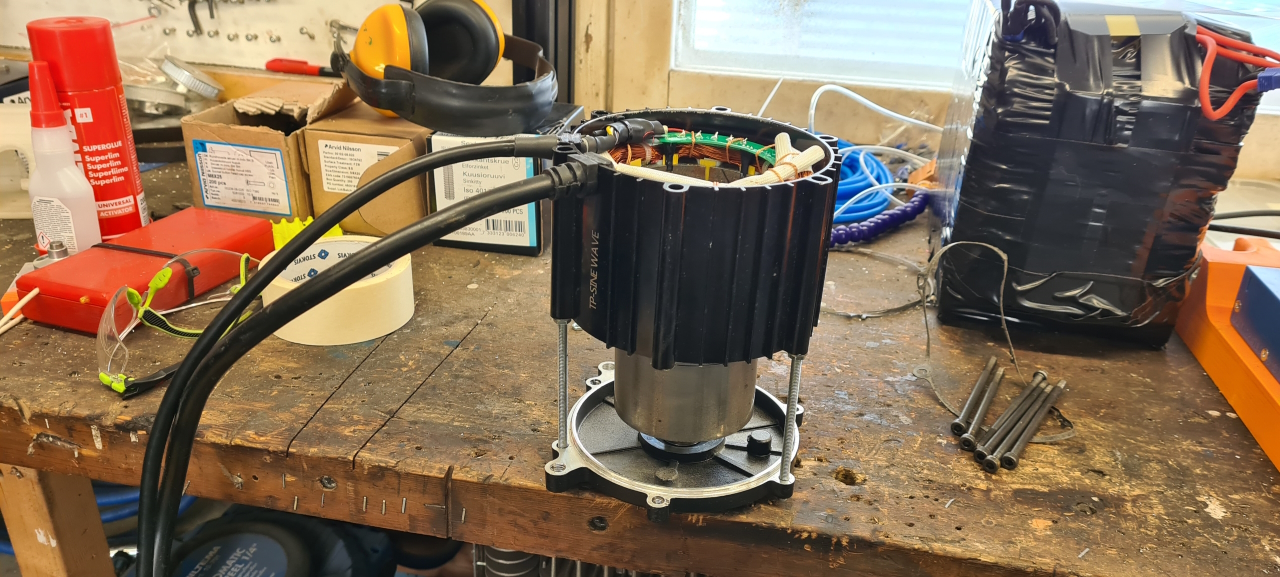
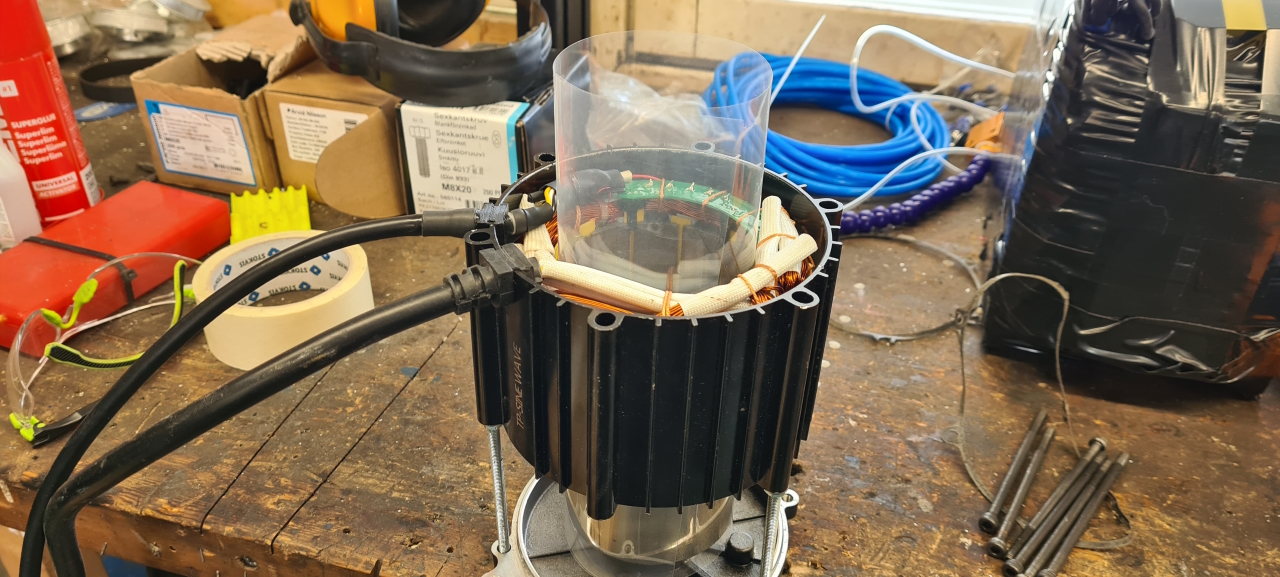
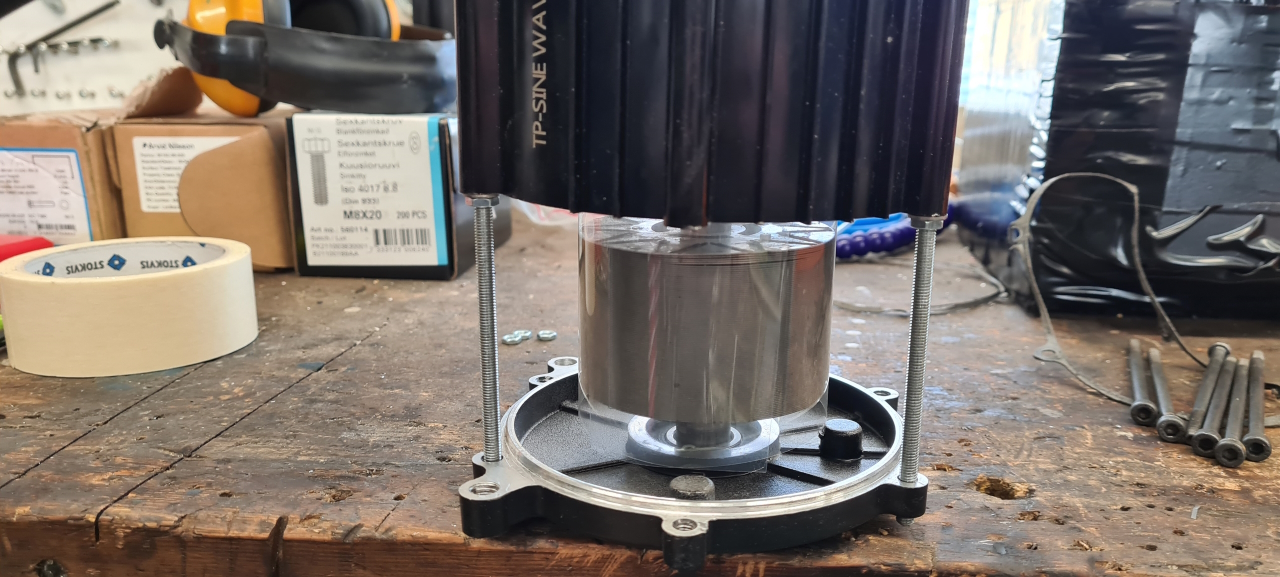
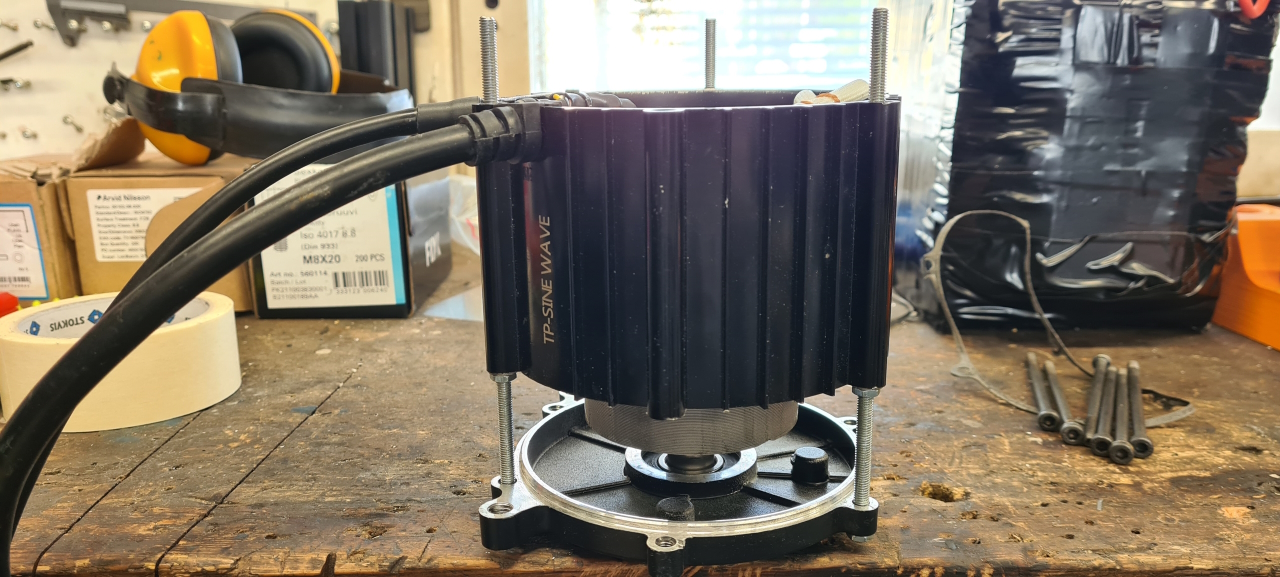
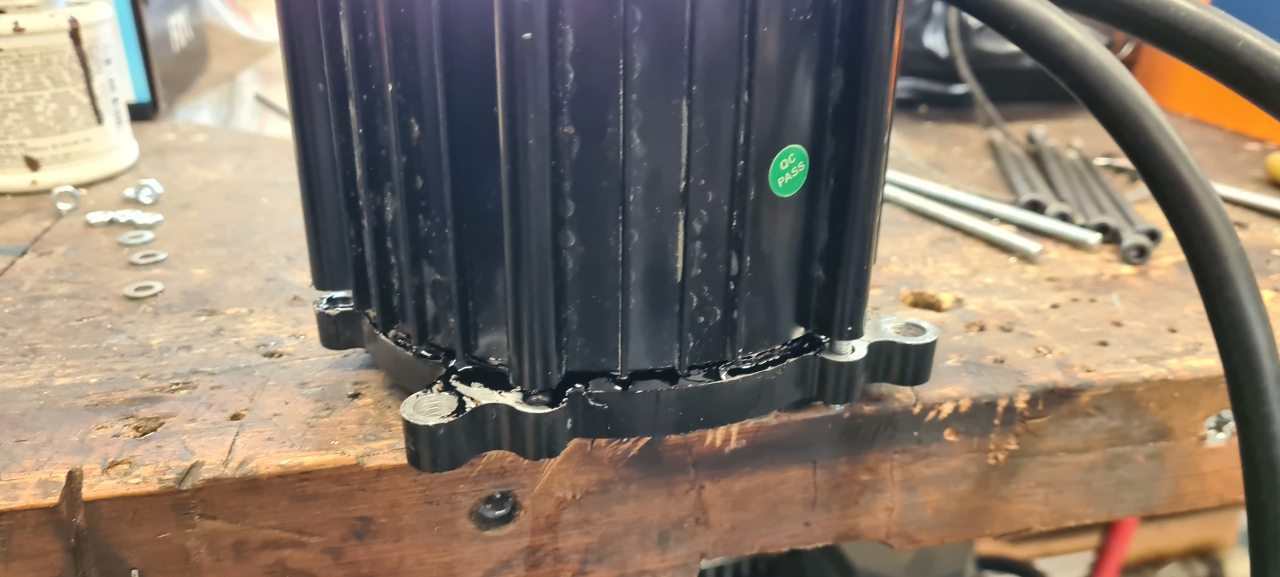
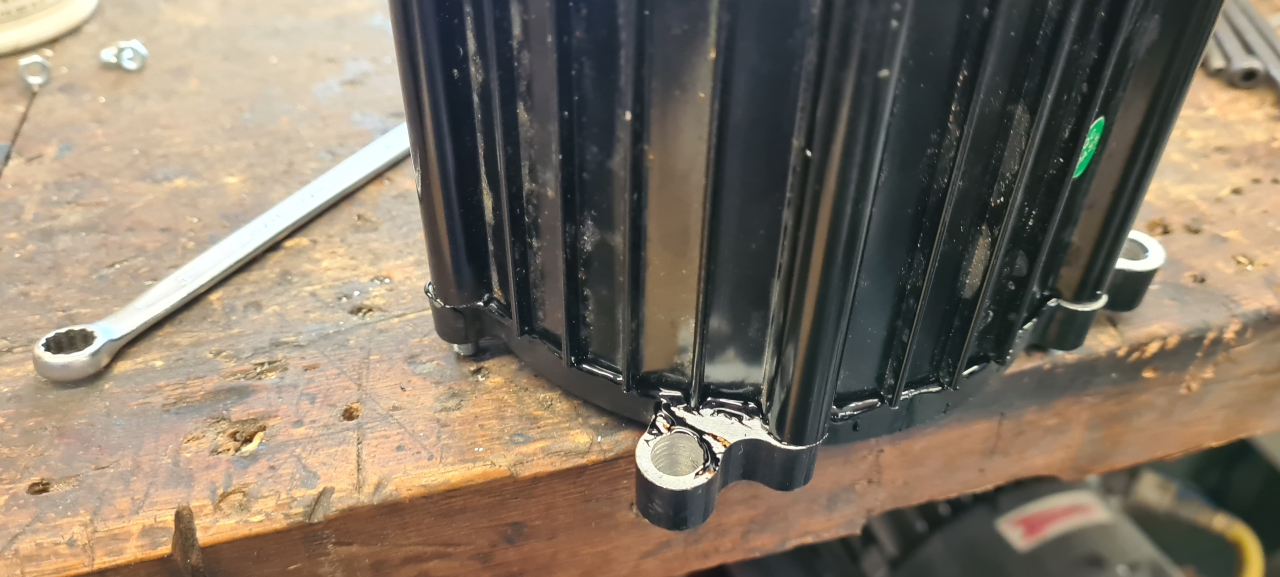
So, now it was just a matter of easing the stator down all the way. Most of the way I could just turn the nuts by hand but it’s the last centimeters that are hardest to control but the three-nut-solution made it super easy.
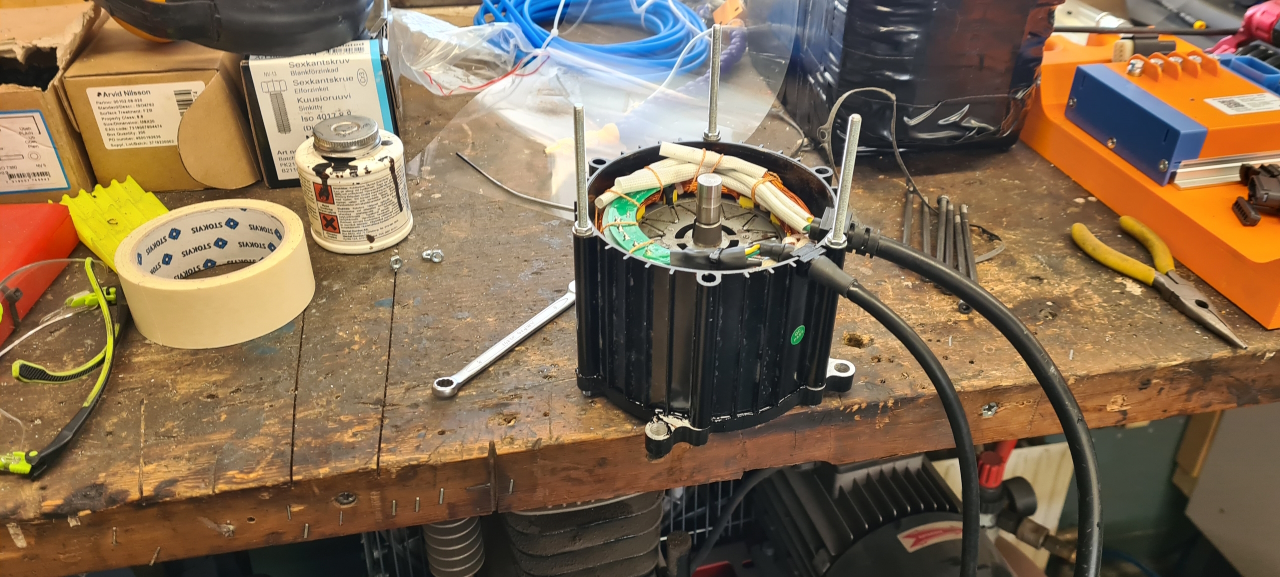
Frame preparation
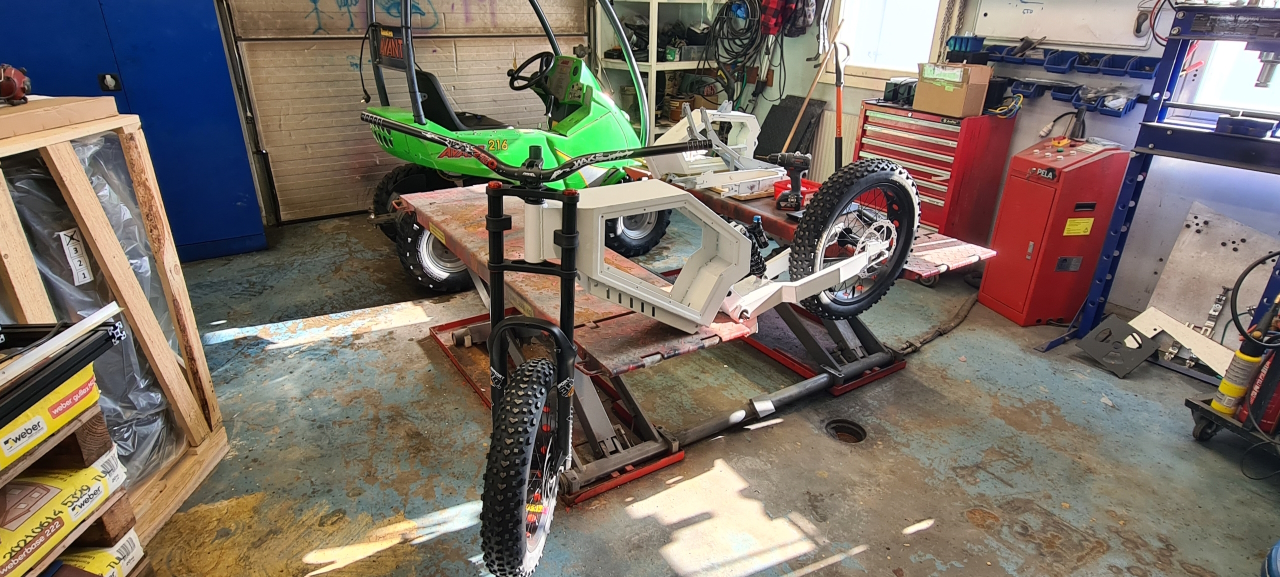
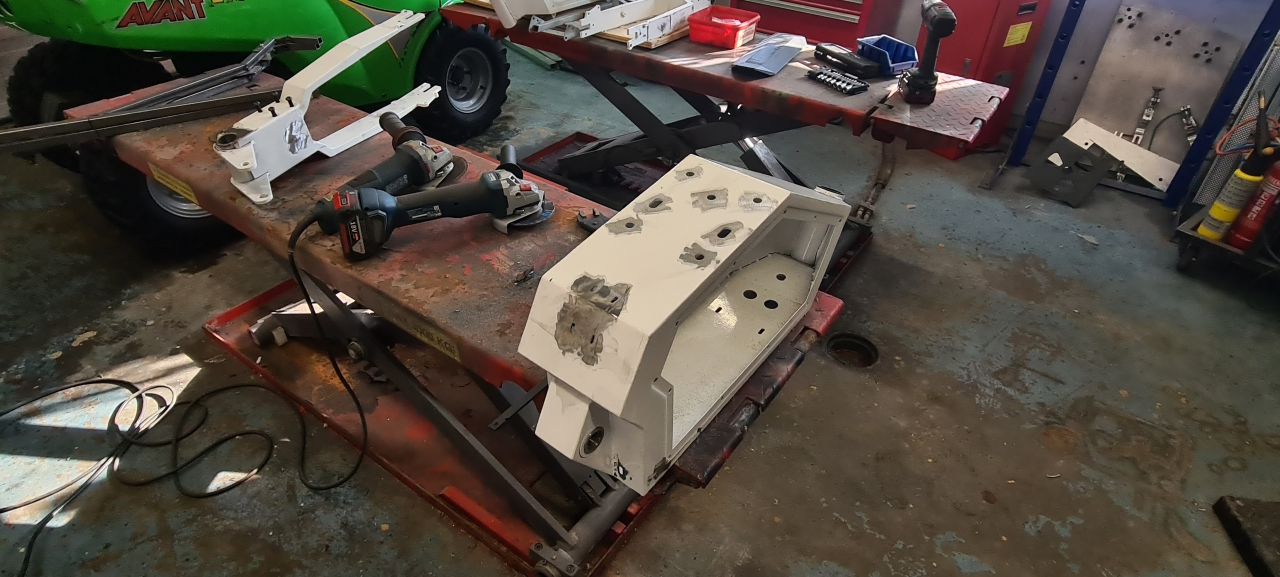

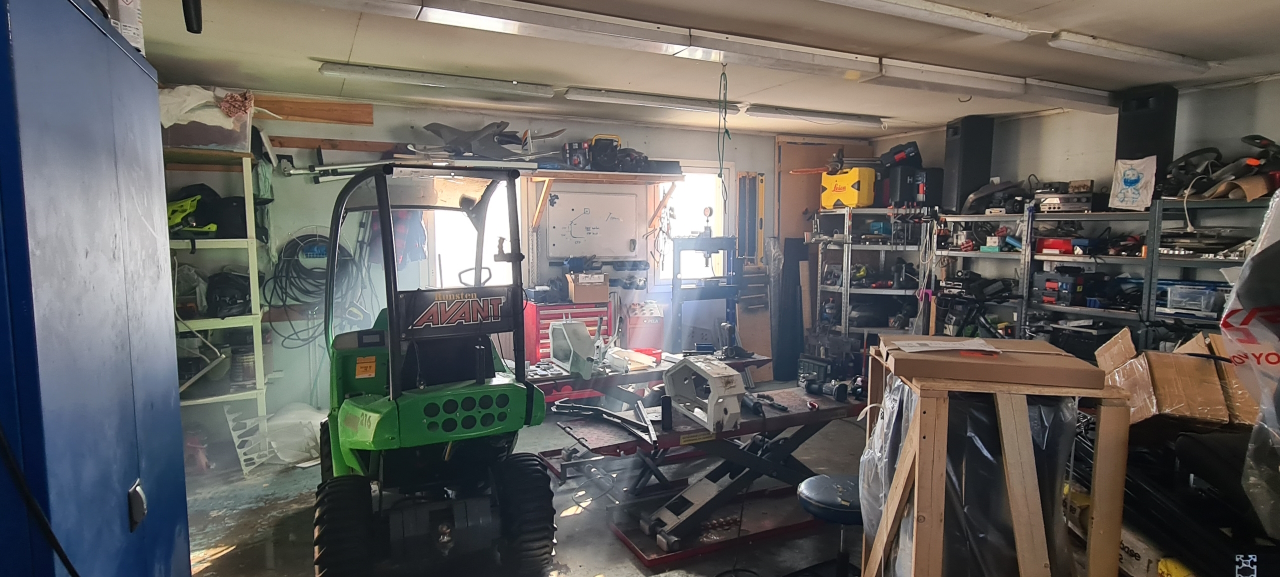
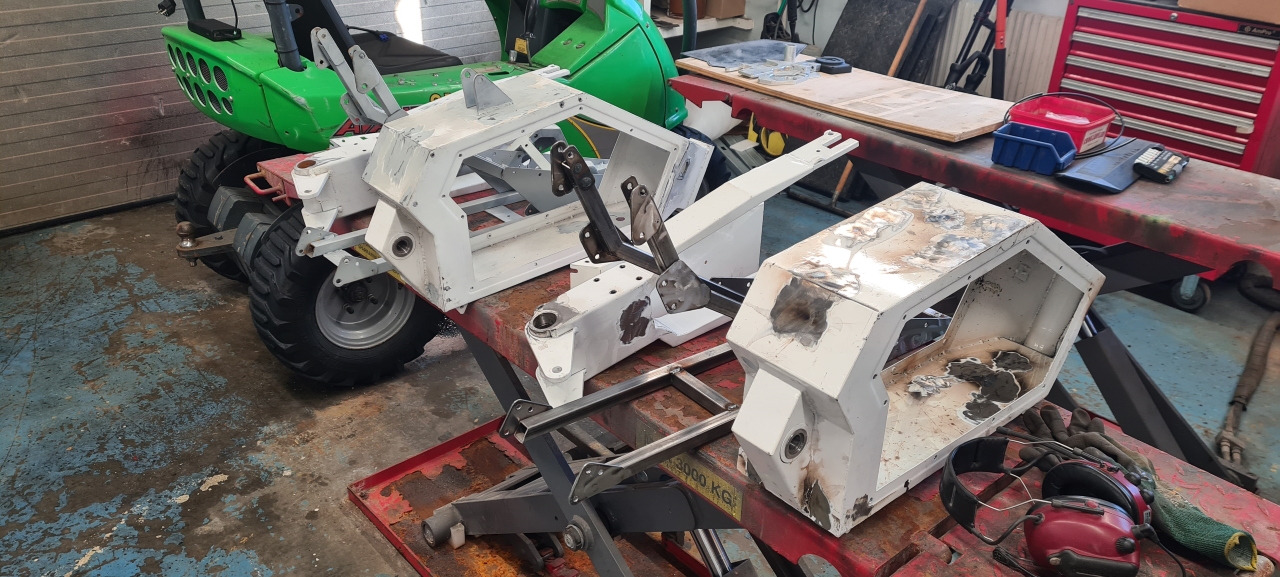
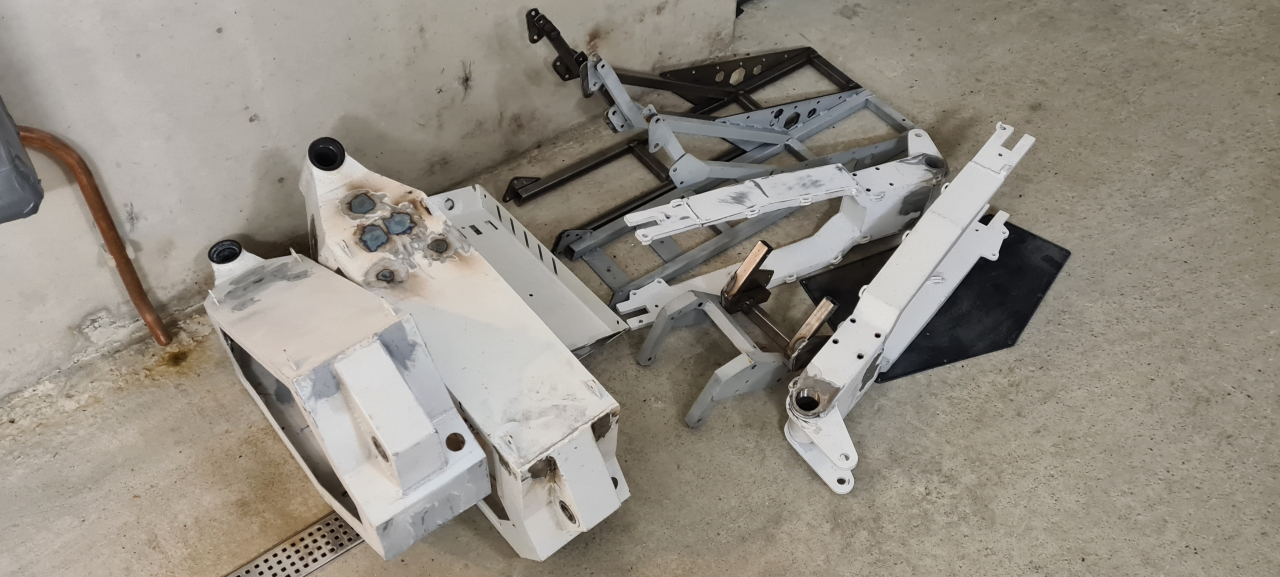
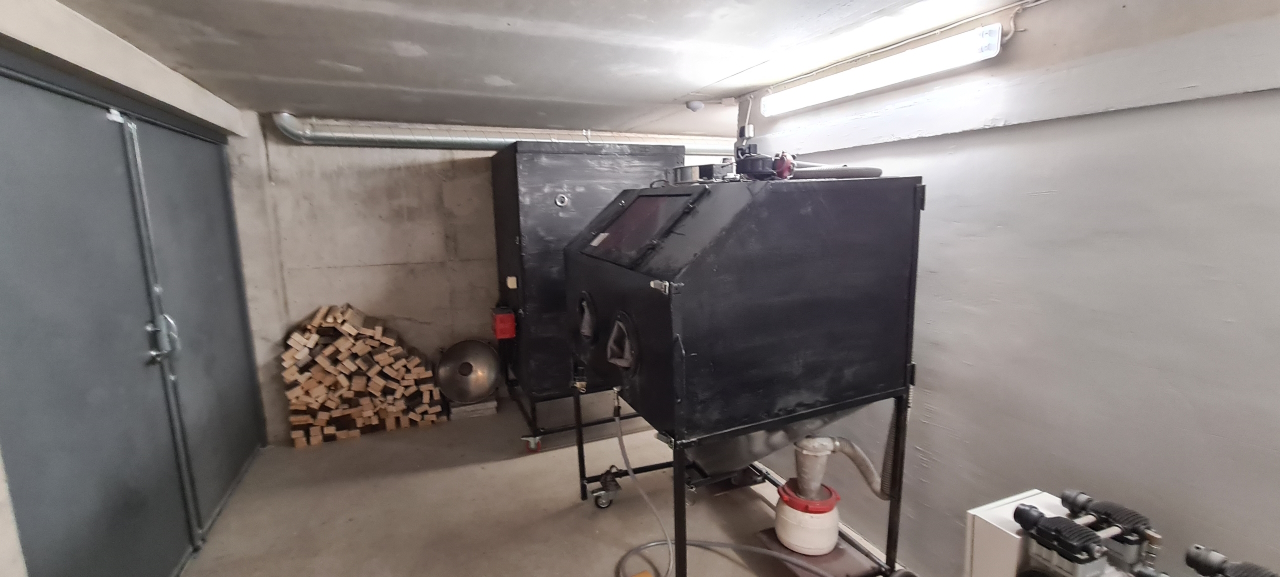
To be continued..
Bike repair and improvements
So, after testing the bike for a few trial runs it stopped working. Connecting to the controller I got an error saying ”Post static gate test” which usually means there’s a problem with the controller having a mosfet fused to ground or the postitive terminal.
So, a bit displeased I started taking the bike apart but before putting in an RMA I decided to test another controller I’ve got sitting around, and got the same error with that one.. so, the problem seemed to be with the motor, which was a bit wierd. Connecting my second motor to the controller confirmed that the motor was the issue since it ran without any problems.
After doing some measuring I was a bit confounded as all the resistances seemed to check out and sure enough when I connected the motor windings to the controller it all worked. However, when I connected the hall sensor array it stopped working again.. Hmm..
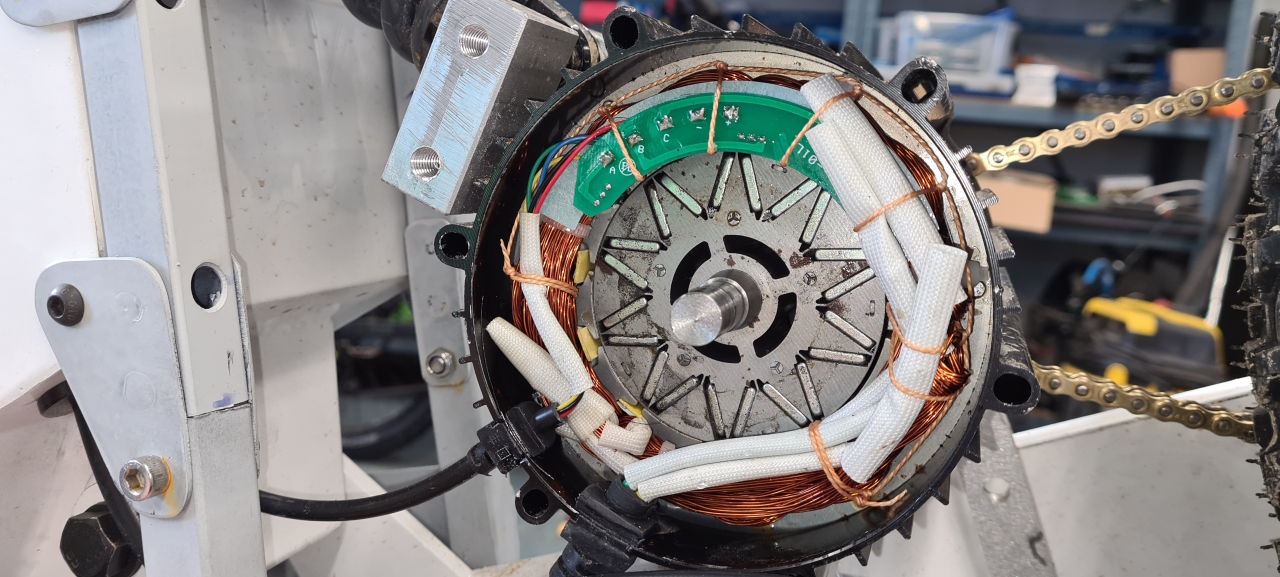
Taking the motor apart the seal that sits between the stator casing and the end bells on the motor crumbled to dust which is probably why the water got in there in the first place.
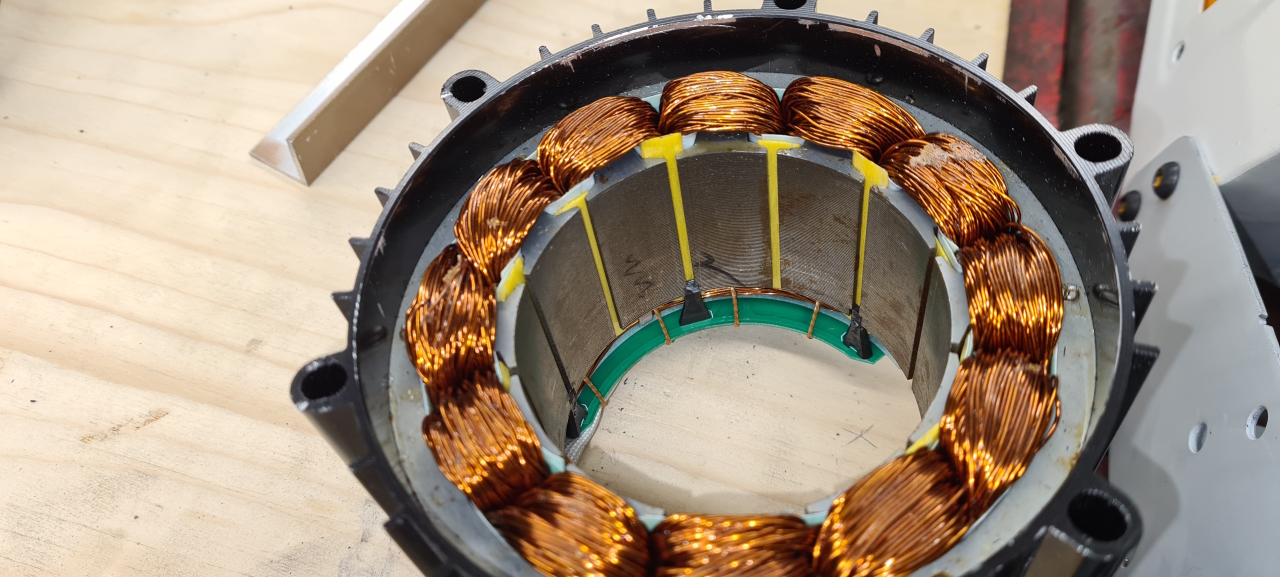
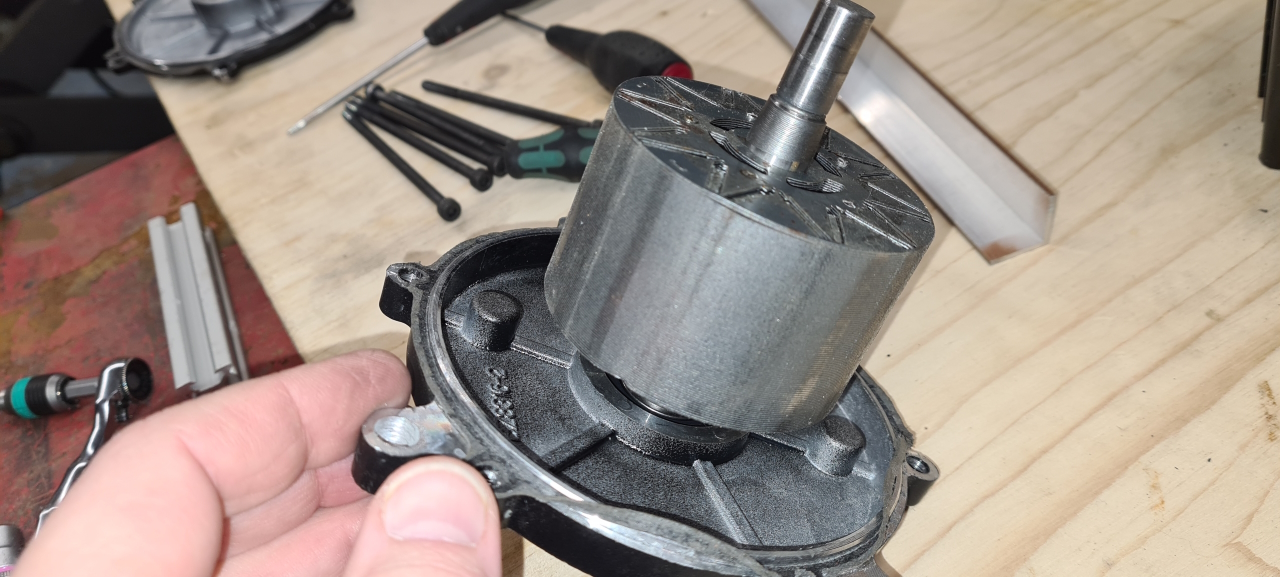
If you get your fingers caught between the stator casing and the end bell on the motor I guess you’d have to leave your fingertips inside the motor. I’m not looking forward to putting it back together again.. I’ll have to come up with some contraption to make it not slam back cause I reckon that’d make the motor self destruct and take half of the garage, both my hands and my left liver with it as it goes…
As I had the motor apart I thought I’d add a thermistor to be able to have the controller reduce power if the motor gets too warm. The Lightningrods motors come with a thermistor if you ask Mike to install one, which I happeded to forget..
The normal way of adding a thermistor is to make a hole in the case and route a cable from the thermistor to the controller through there but I didn’t like the idea of adding another cable to the motor. Two is enough I think. So I instead opted to replace the 5 lead cable that goes to the motor originally with a 6 lead cable instead. To be able to fit the larger cable I had to make a new grommet for the motor casing though.
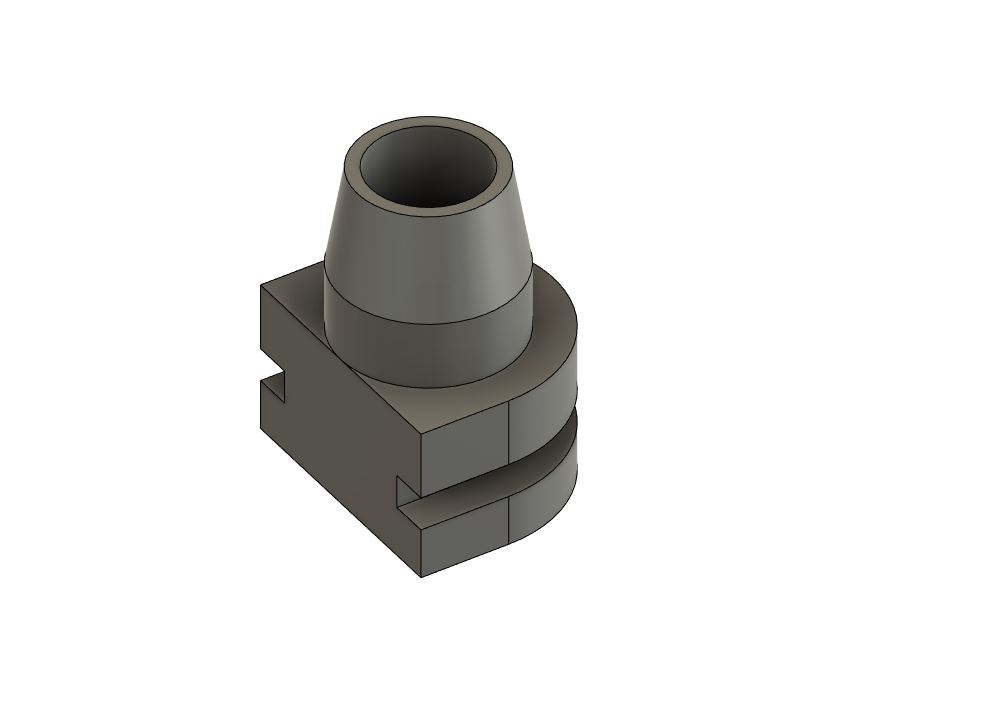
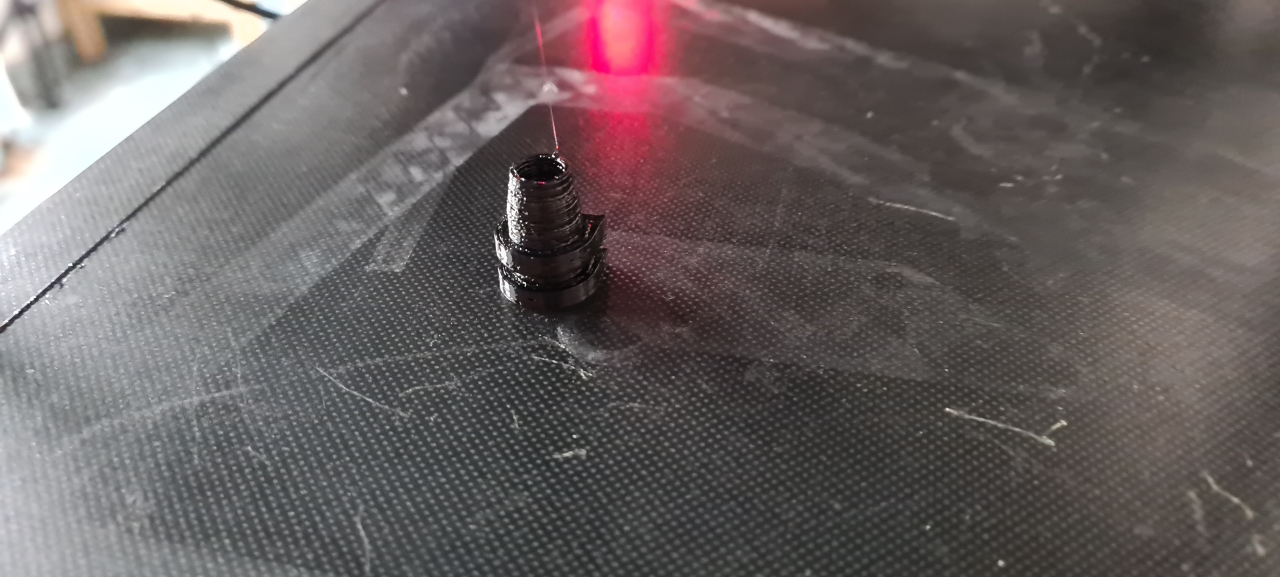
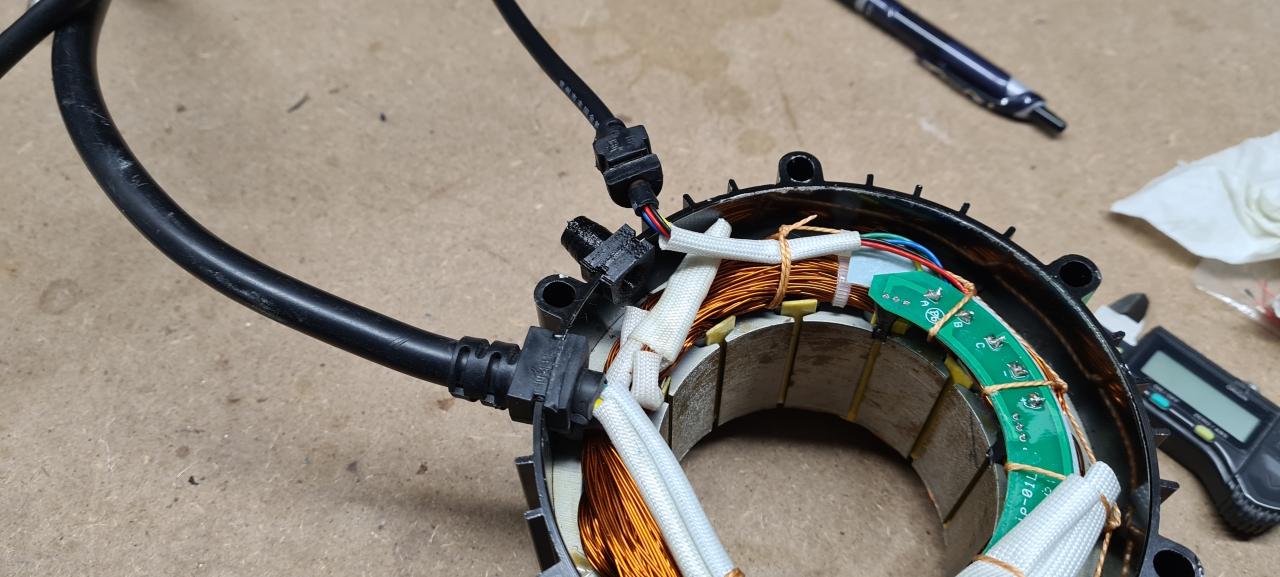
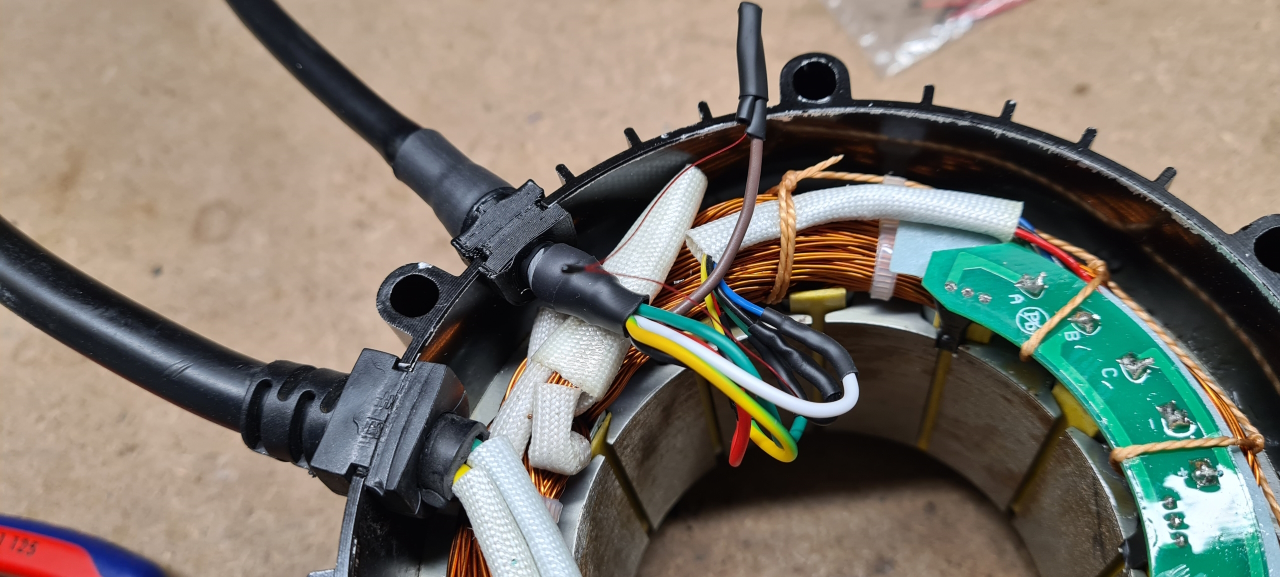
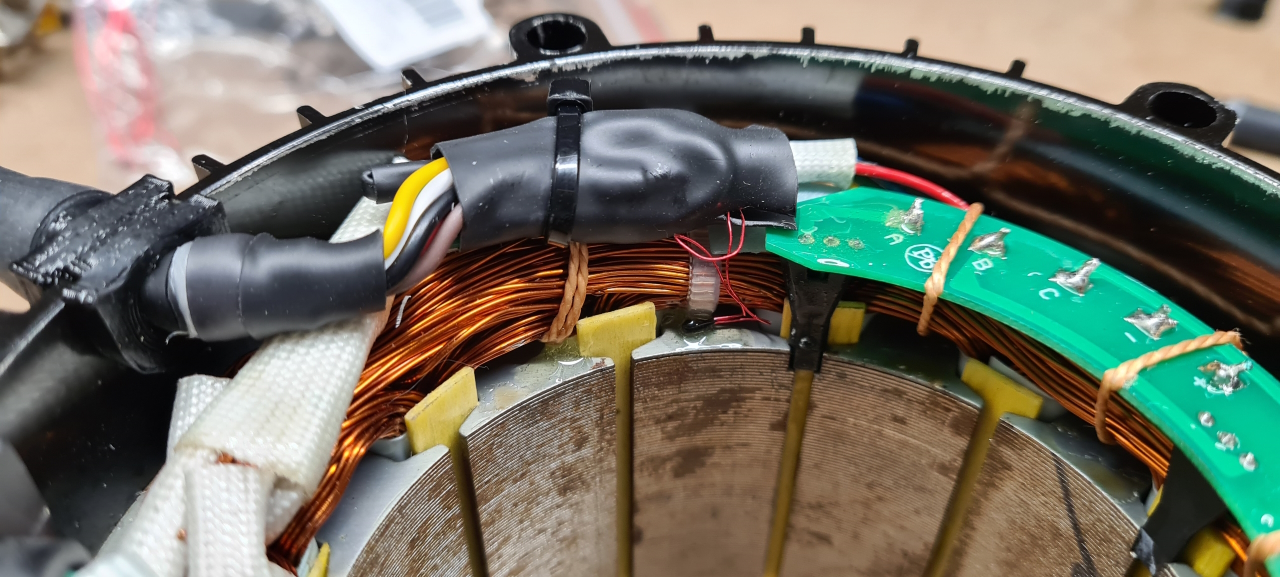

Taking the motor apart I saw that the conformal coating on the hall sensor PCB was missing in part, probably allowing the problem to occur in the first place. I used epoxy to cover the PCB to hopefully make the motor more resilient to failure in the future even though some moisture might get inside.
Well, to be continued..
Final assembly and test ride
So, it’s been a while since I last posted and it’s been a lot going on. I have had to rebuild the battery for my Radon Swoop which has taken quite some time with measuring all cells and cleaning everything up for re-use but there’s been a bit of progress on the RunBike project too.
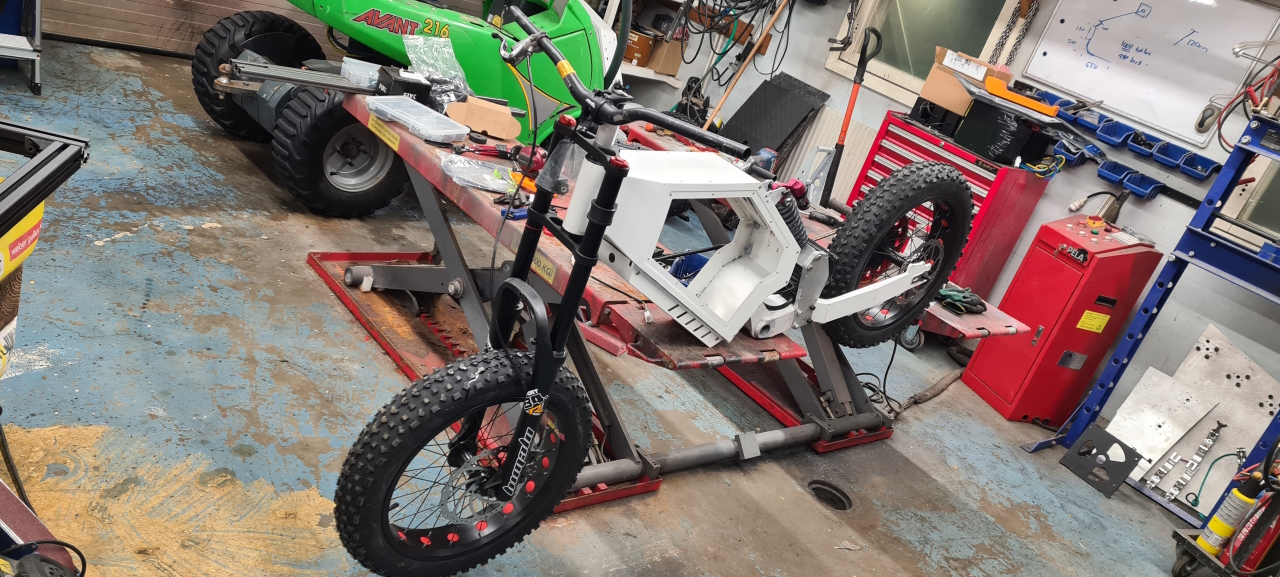
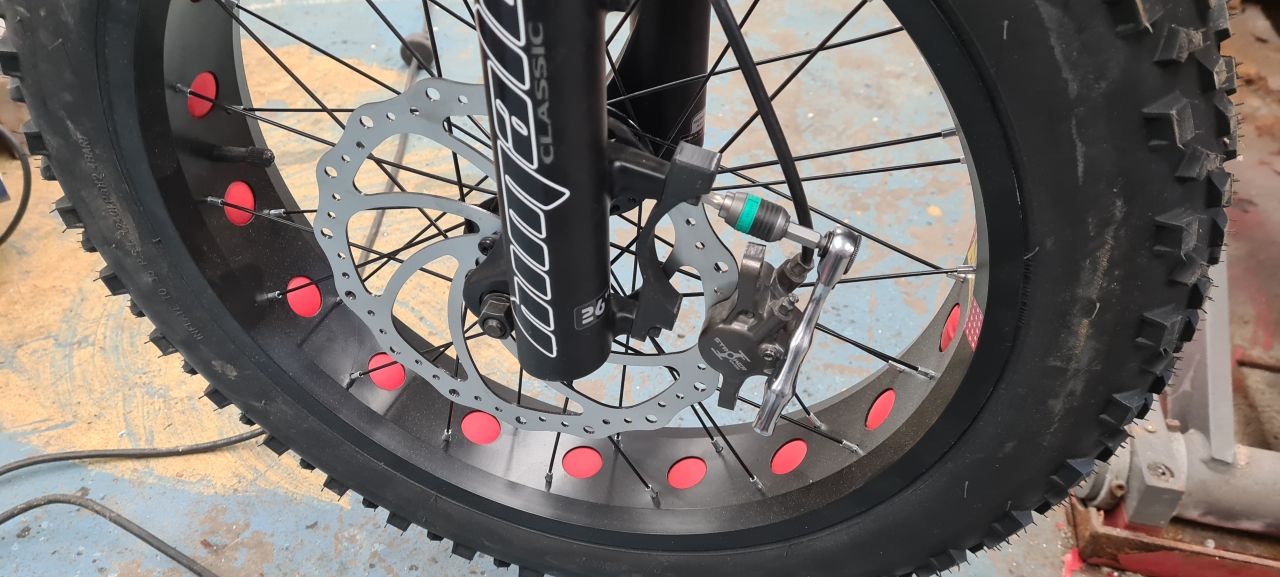
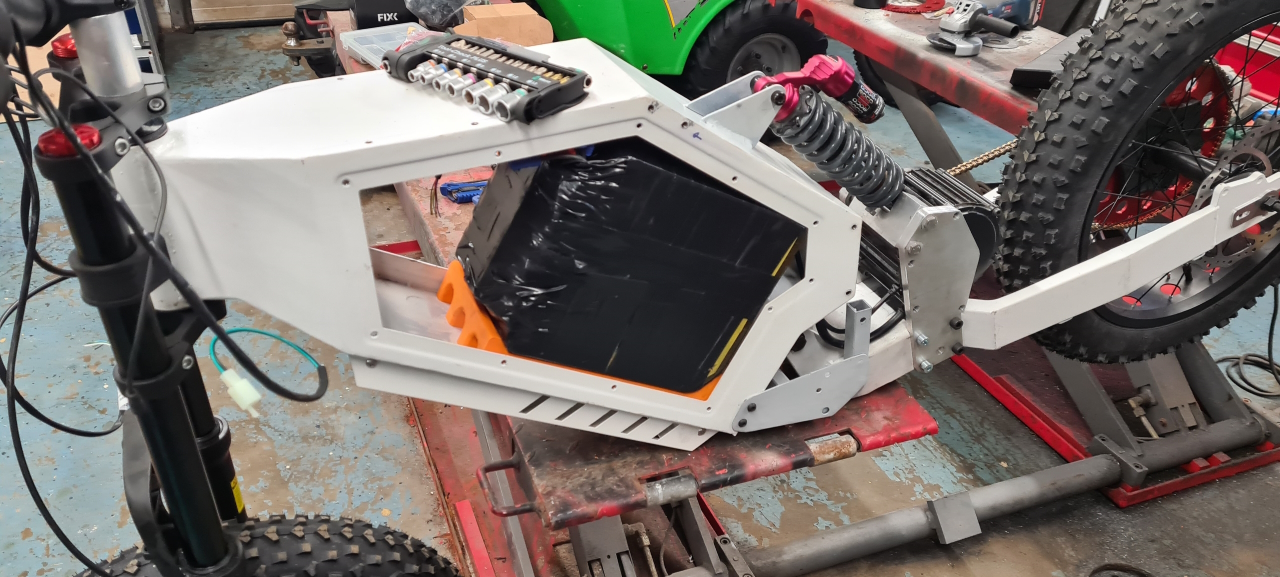
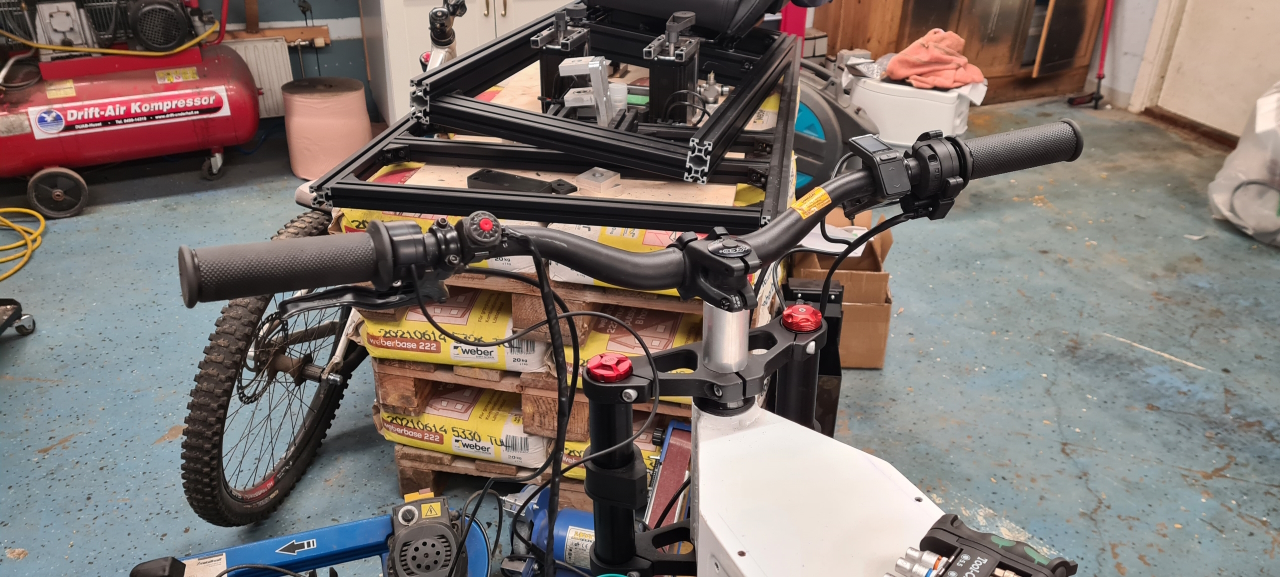
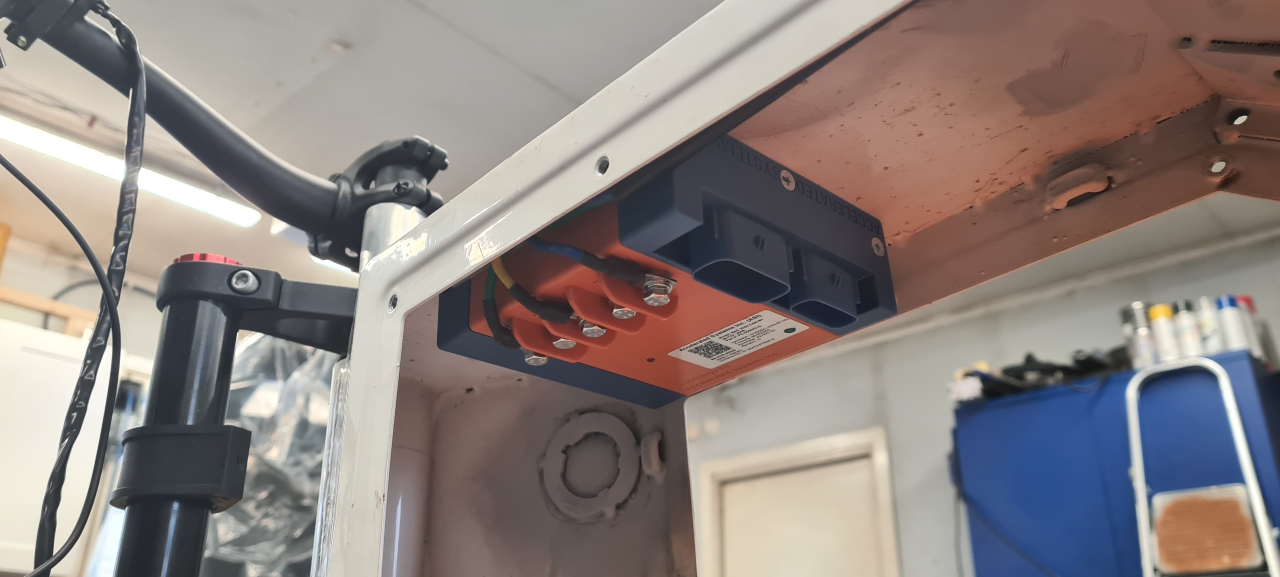
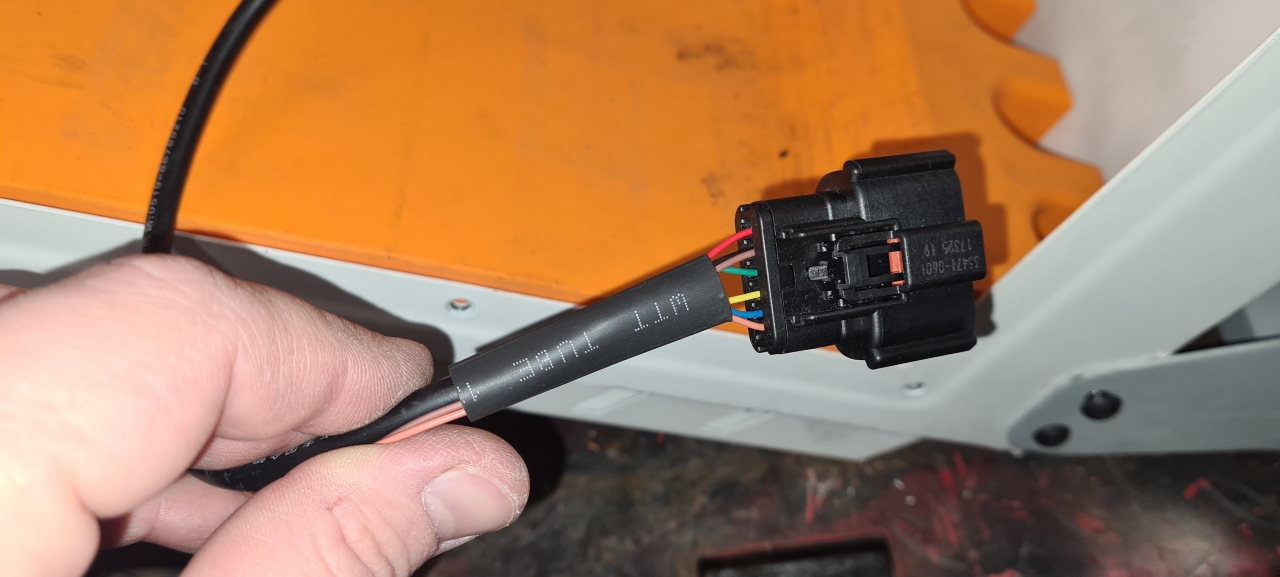
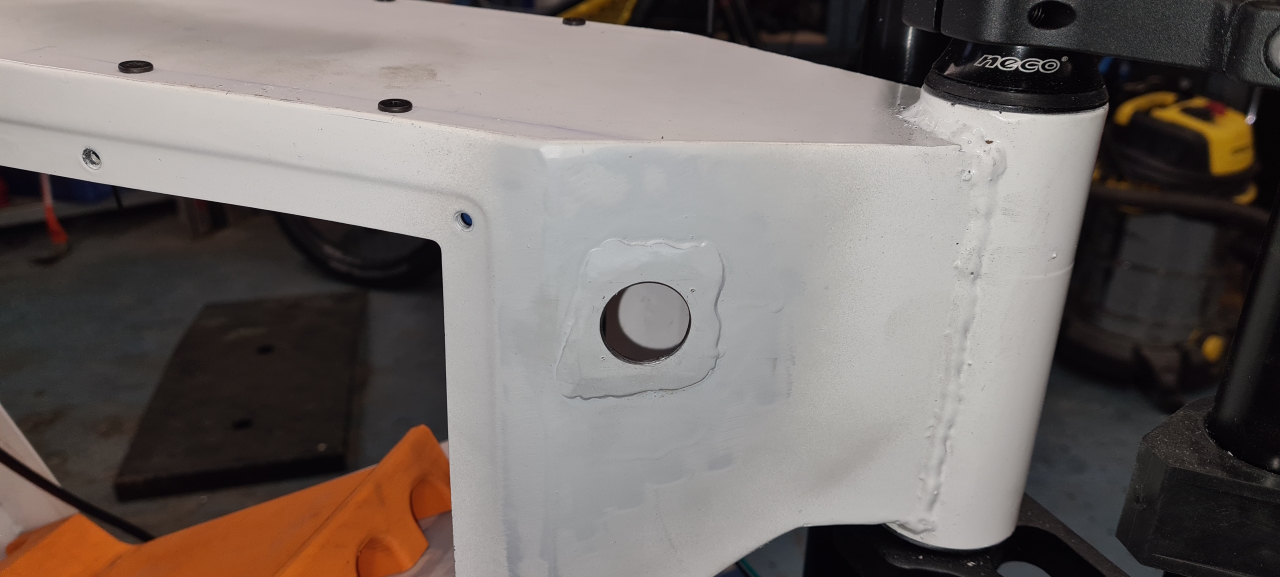
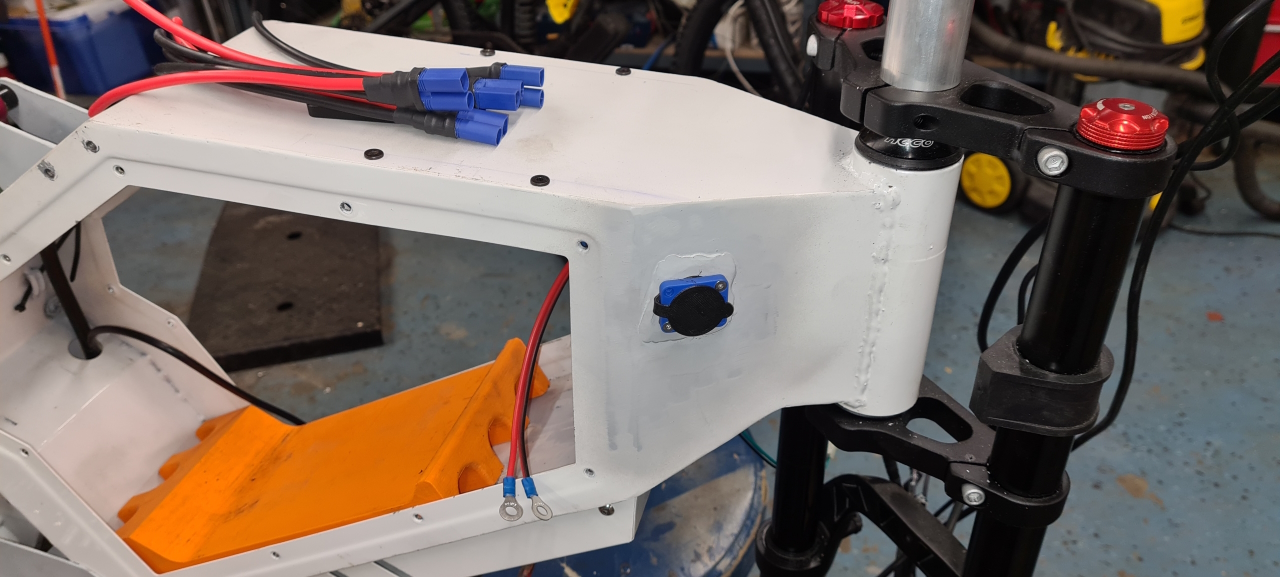
Drilled a 24mm hole, sealed and added the charge connector for the battery.
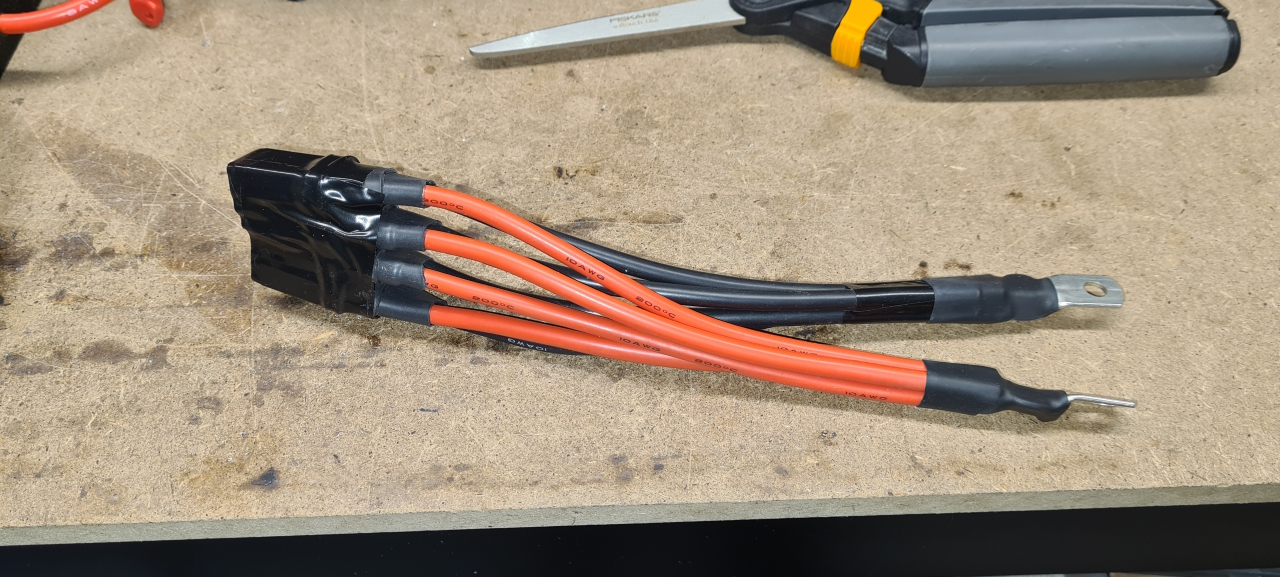
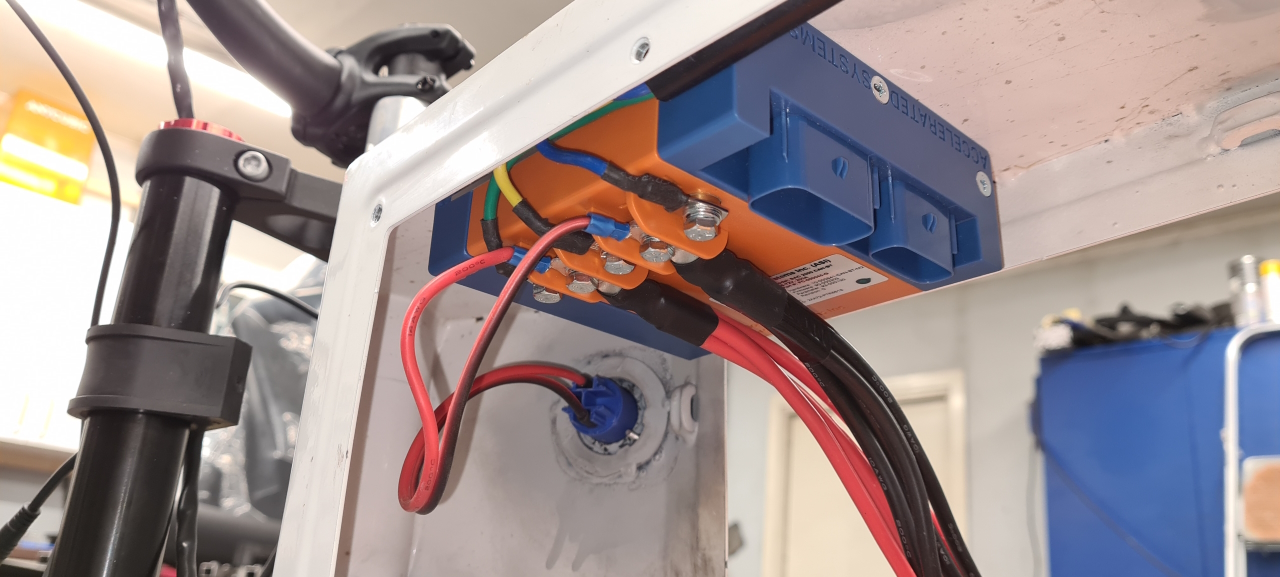
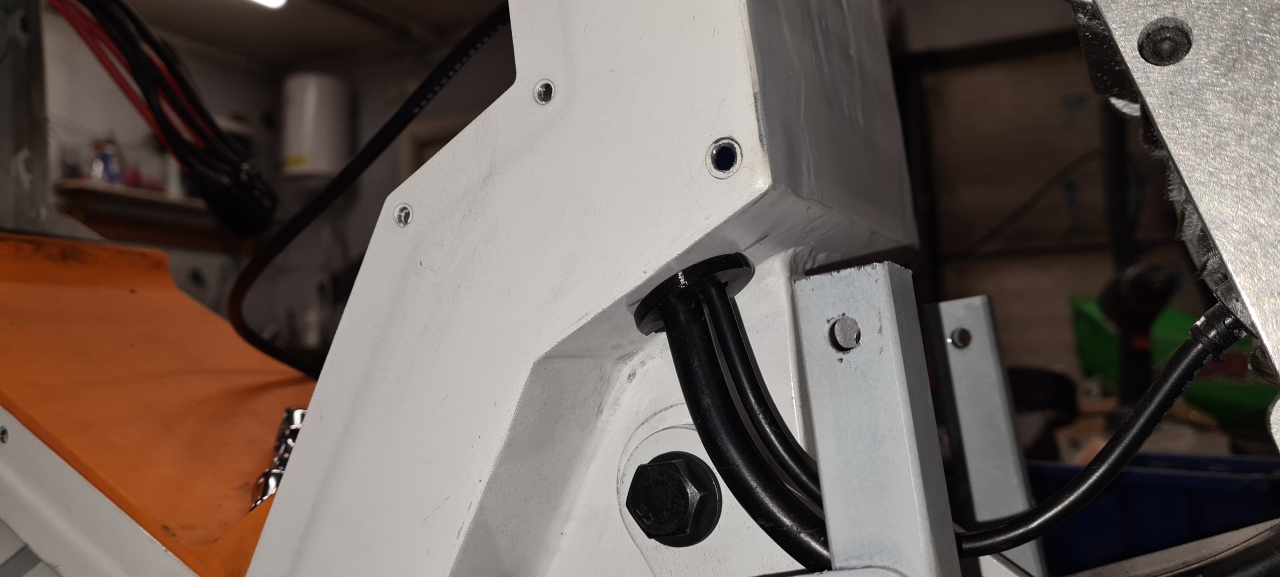
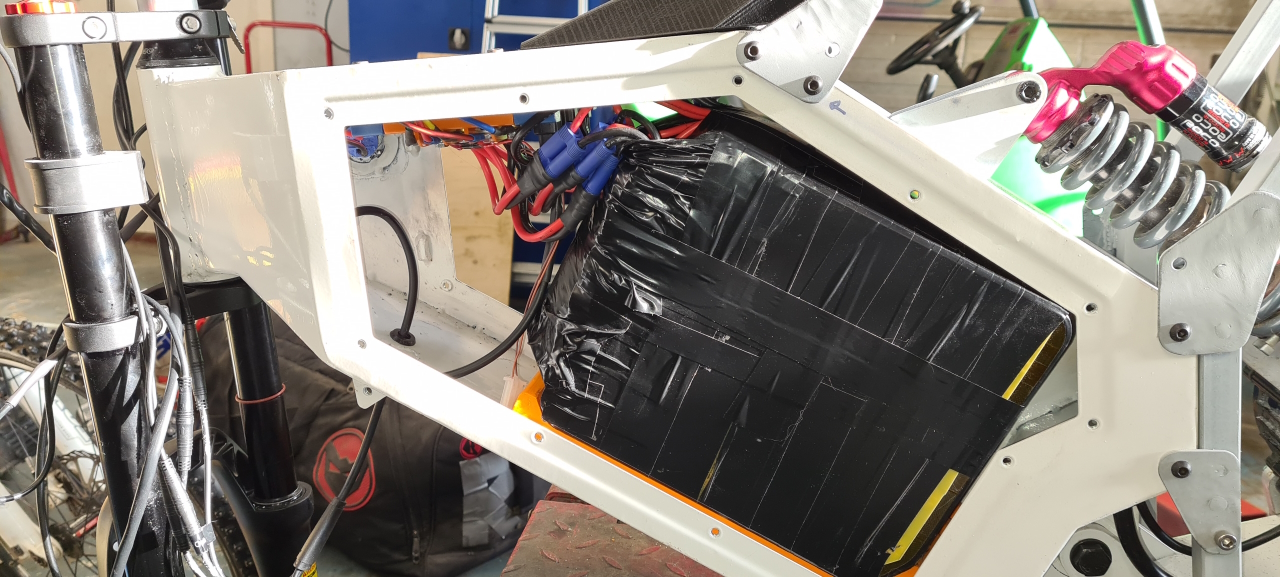
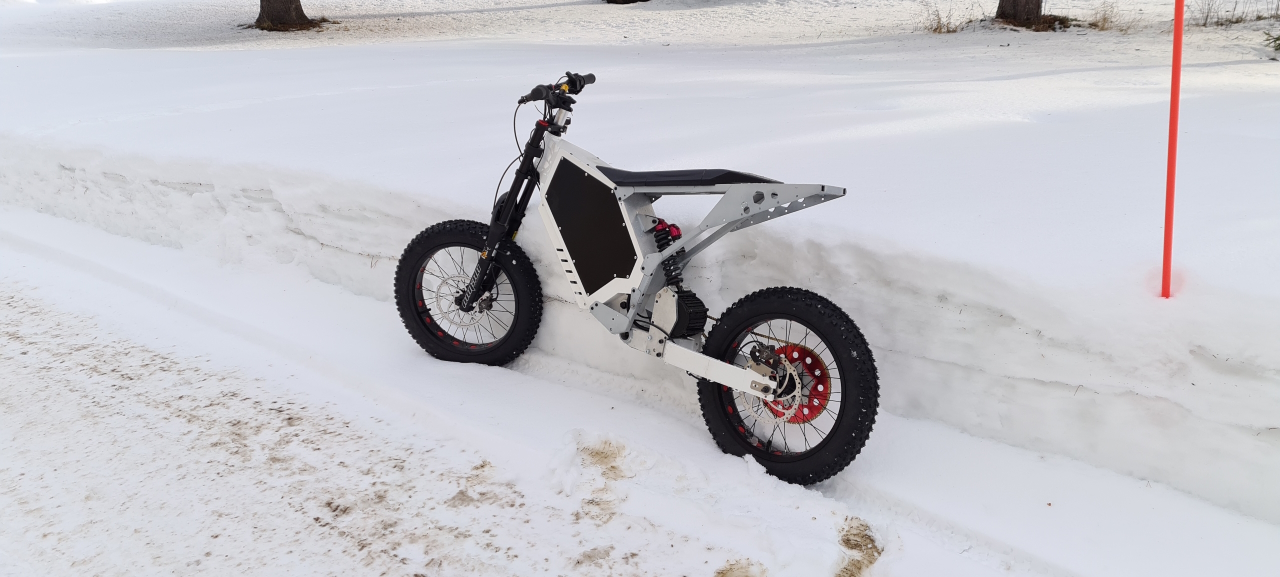
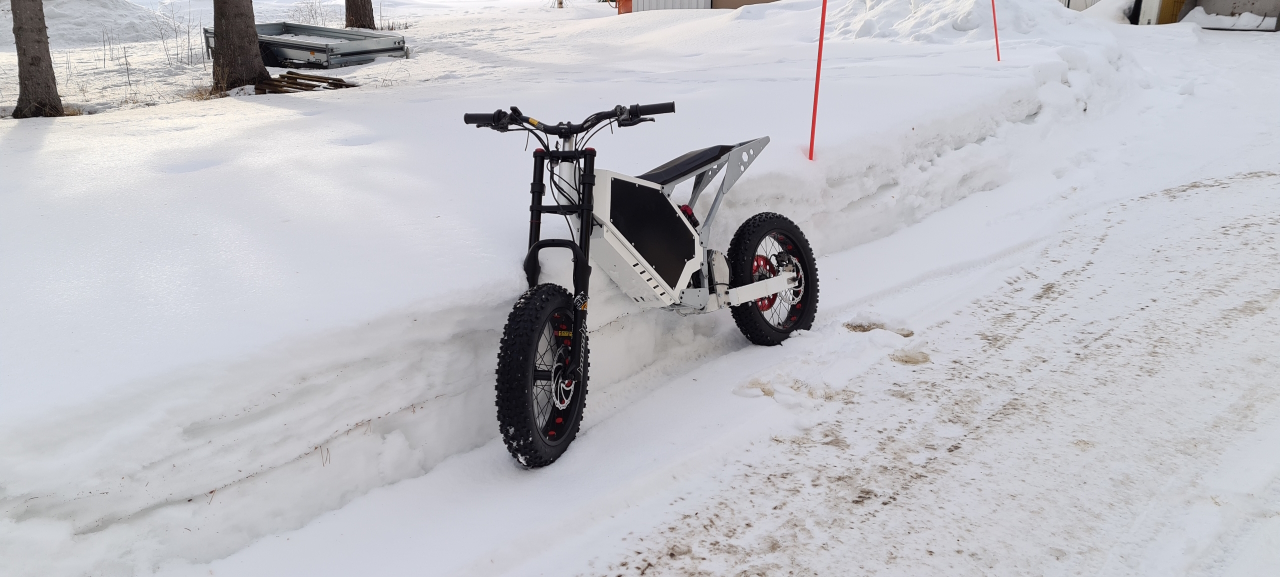
The bike runs super smooth with tons of acceleration and a seemingly high top speed. The spedometer isn’t calibrated yet so I have no idea how fast I’m going and the roads are covered with ice, but it feels nice! The torque makes the motor pull the rear wheel forwards though so I’ll need to add a chain tensioner to secure it in place. I also need to add brake fluid to the rear brake, which is good to have even though the regen braking is awesome! Also, footpegs will be nice to have to be able to ride standing up!
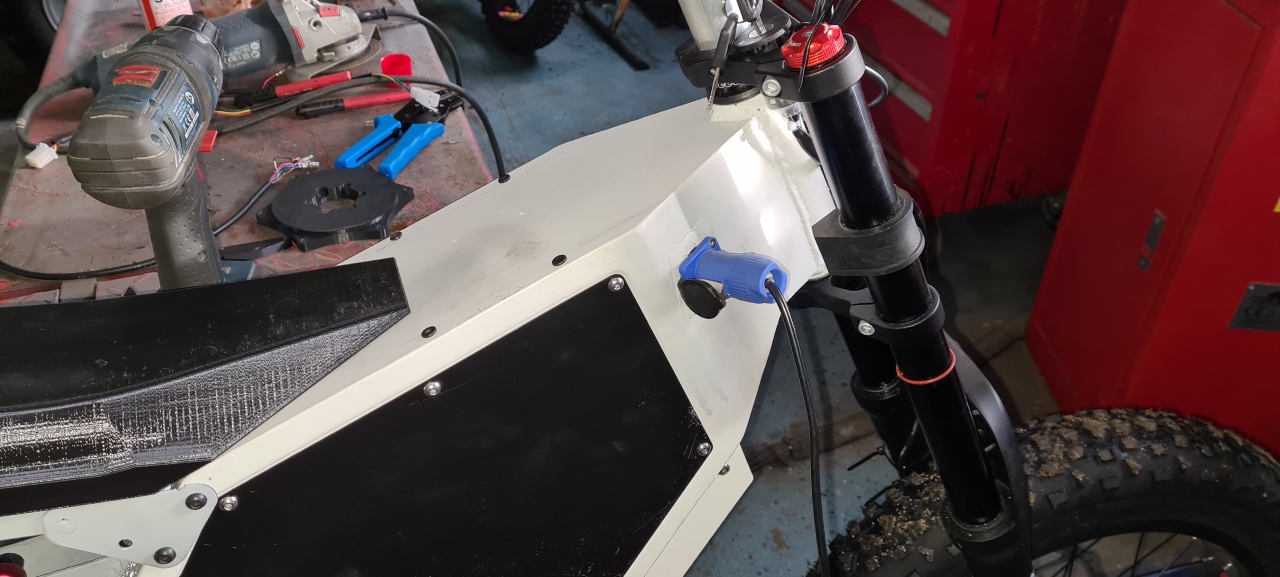
To be continued with more awesomeness..
Battery mouting solution, work in progress
Rear frame, shock- and motor mount
So, it’s been a while since I updated the project but it’s been a slow progress.
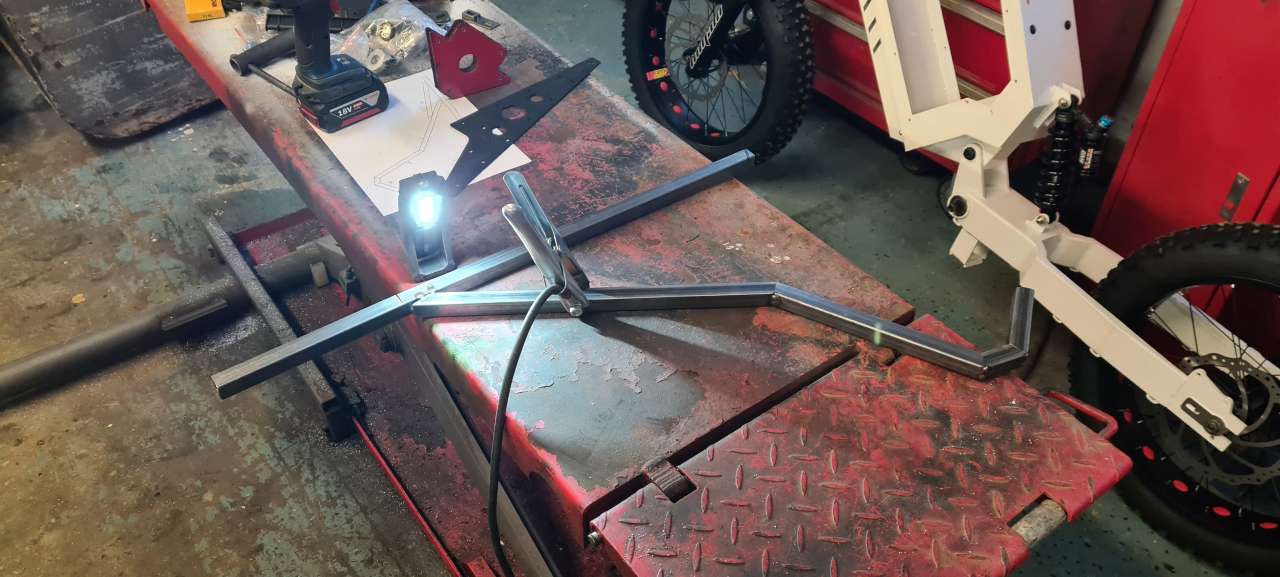
Started by building a mockup for the subframe to test fitment and how it’d look on the frame.
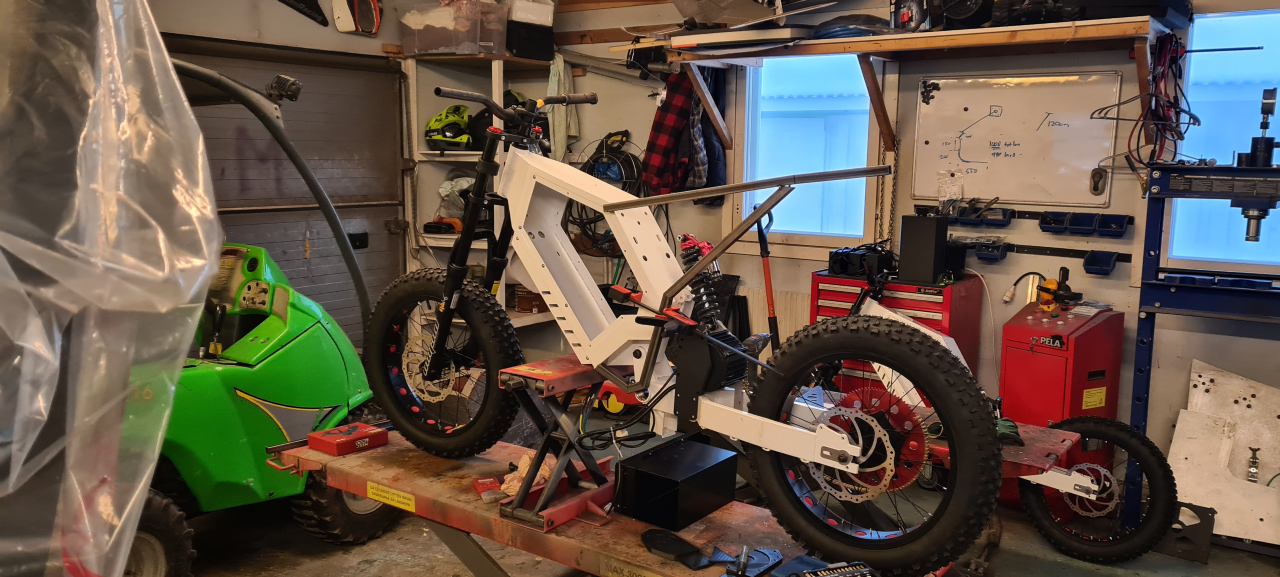
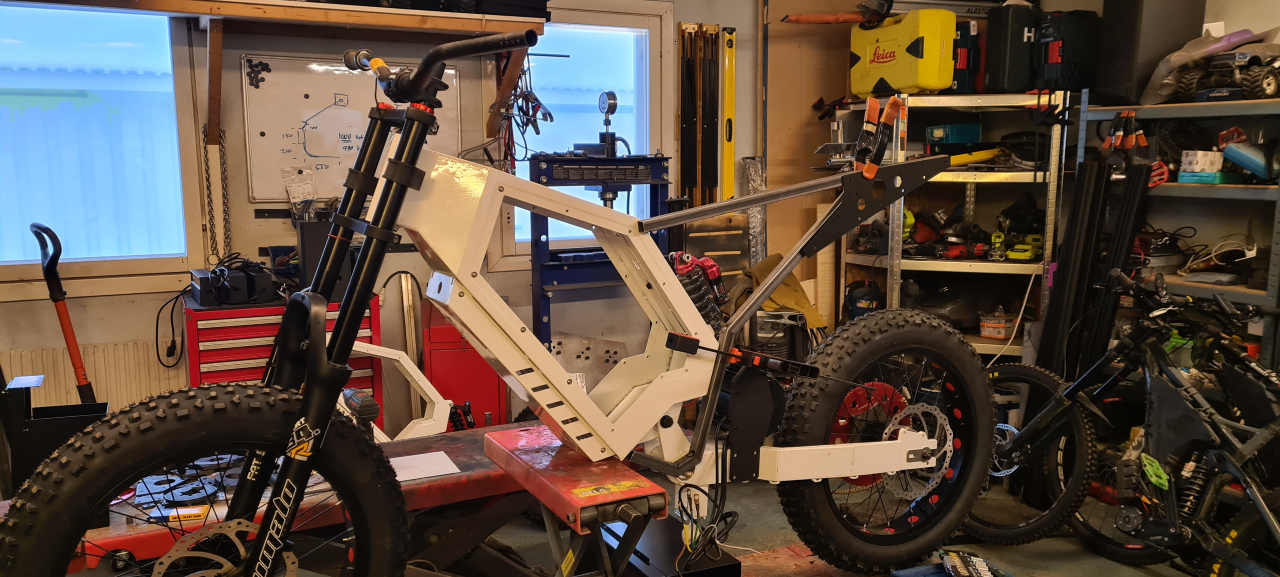
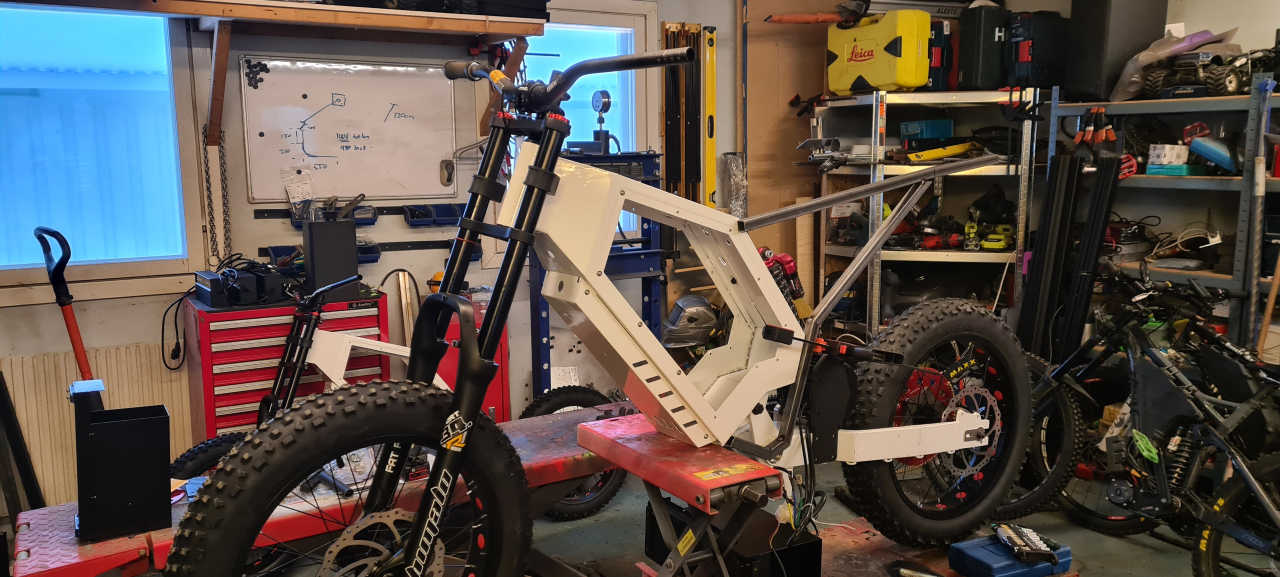
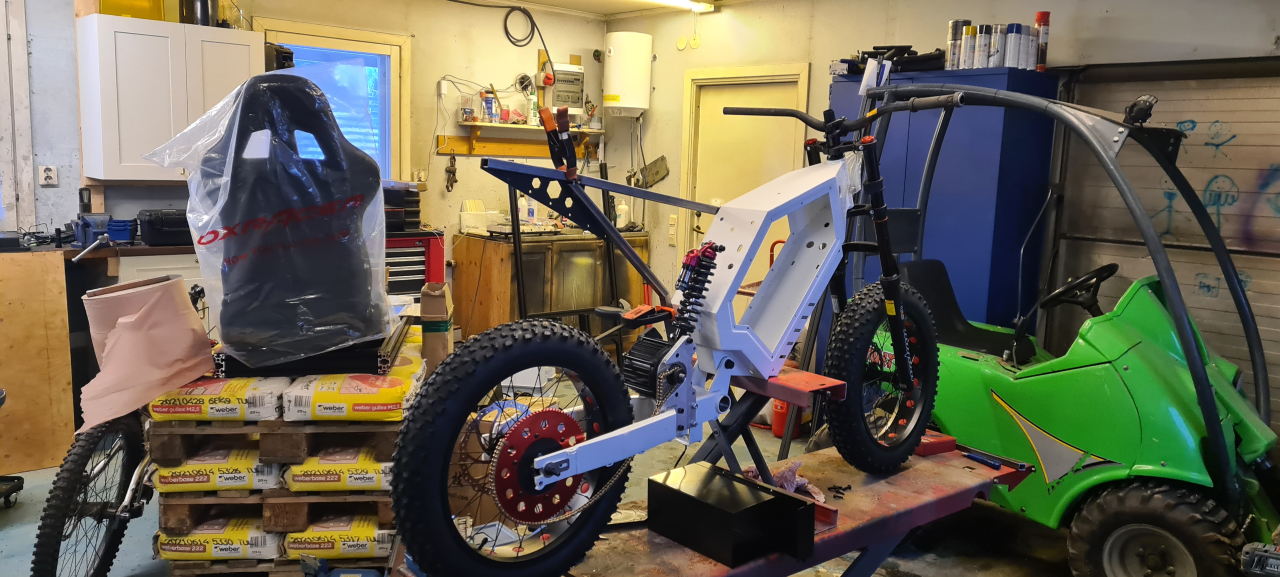
I’m pretty happy with how the mockup looks and fits on the frame, and it seems to be sturdy enough and kind of not too heavy (this isn’t going to be a super light-weight bike anyhow) so, on we go.
After having upgraded the CNC plasma with a better Z-axis it’s good to cut steel sheet with pretty good precision, so I cut the brackets needed for making all the subframe parts from 2mm steel sheet.
The result is pretty awesome for a low-cost DIY contraption..
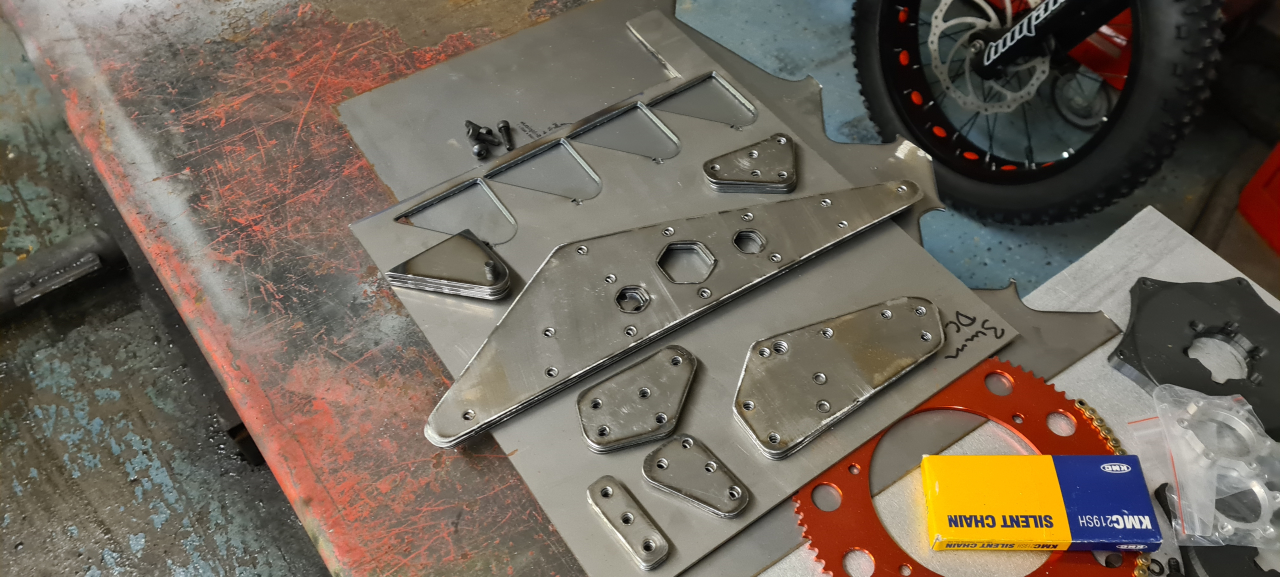
After a little bit of polishing with the grinder the final result is more than good enough.
Unfortunately the 20×20 square tube mounted on the side of the frame interfere with the rear shock, the way I were planning on mounting it so I needed to come up with a new bracket.
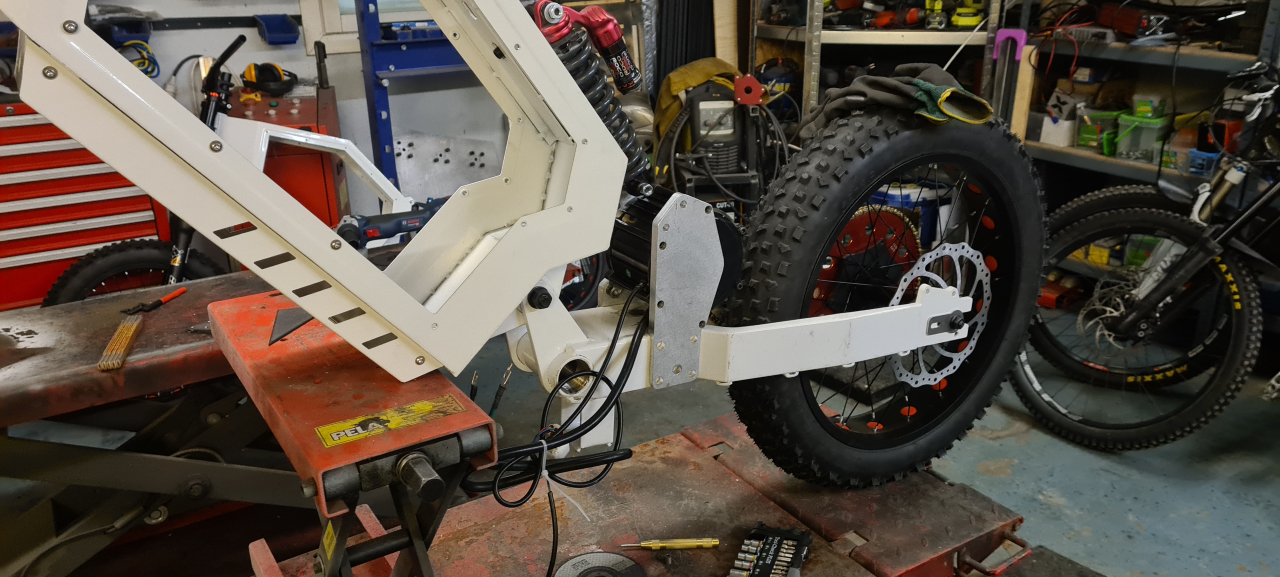
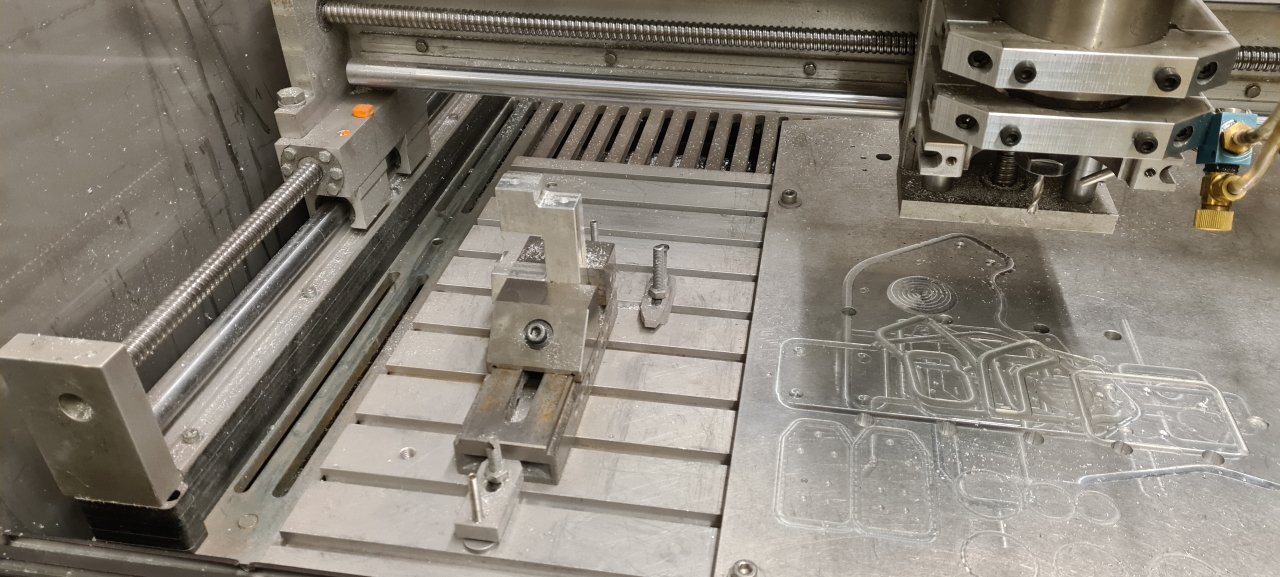
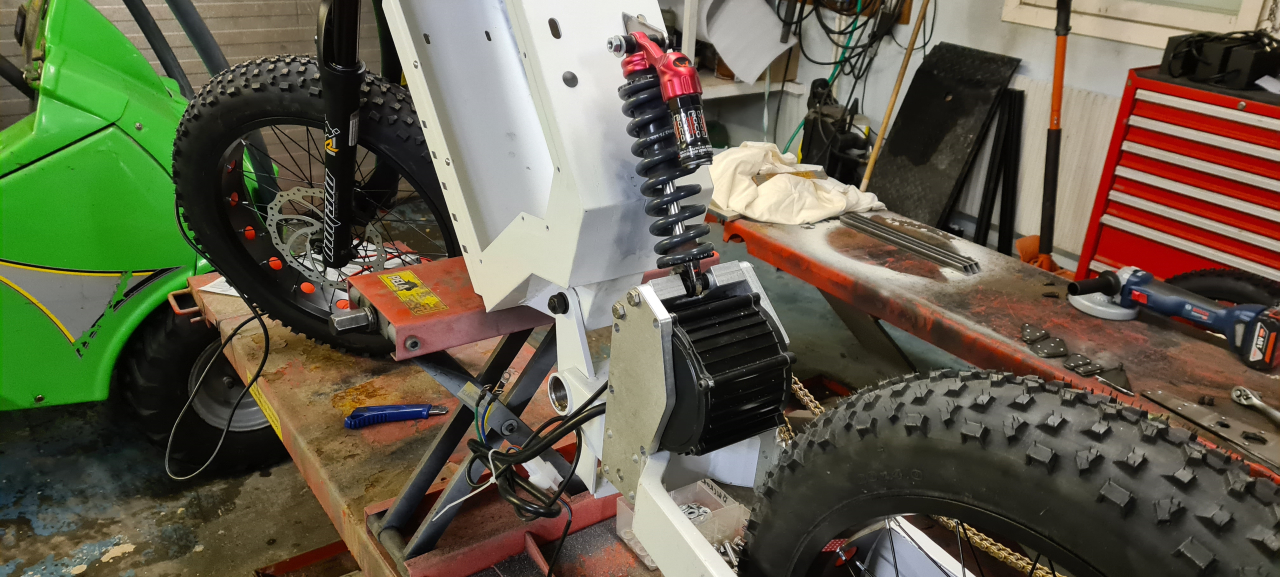
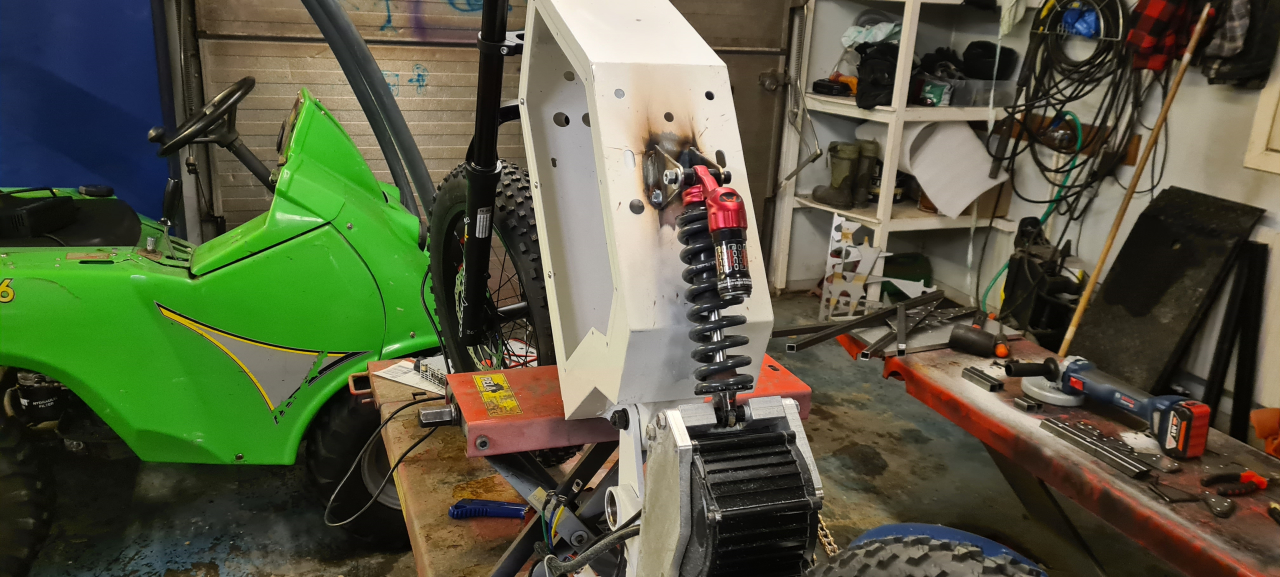
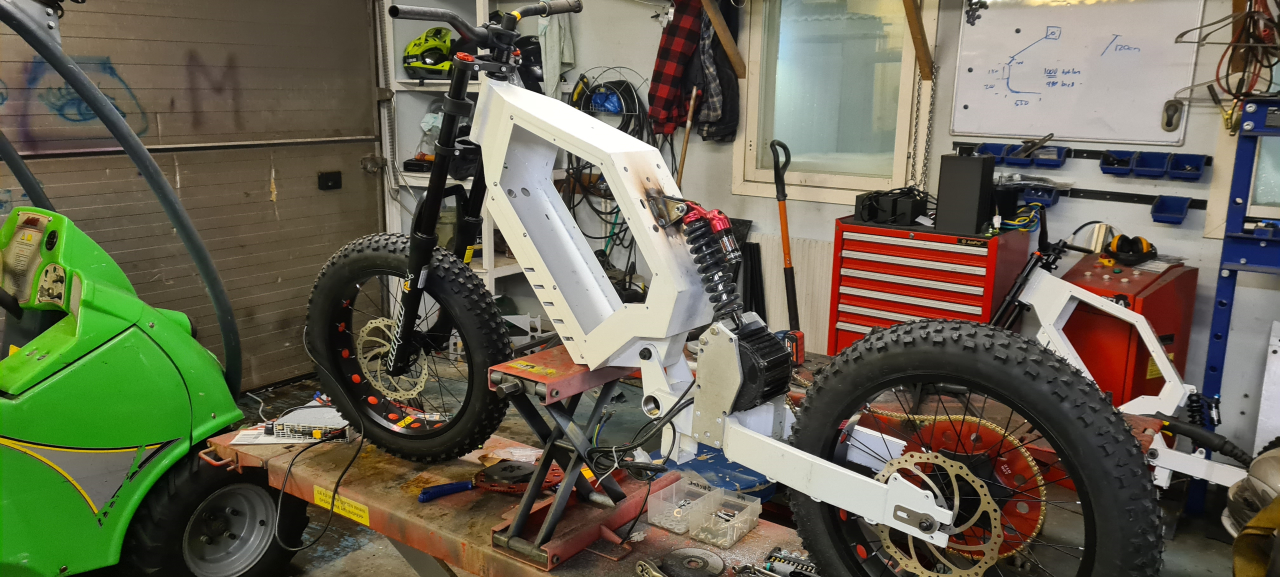
So I cut a couple of ”ears” from 3mm steel sheet and welded the upper shock mount onto the frame. Now the stance of the bike is decided and it feels pretty OK.
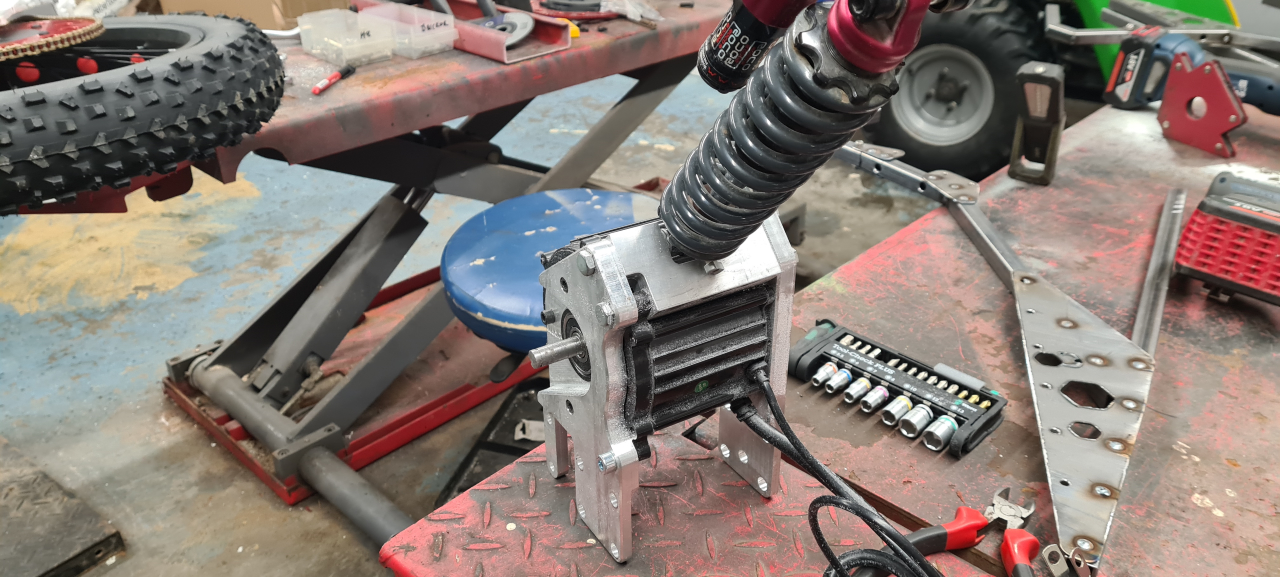
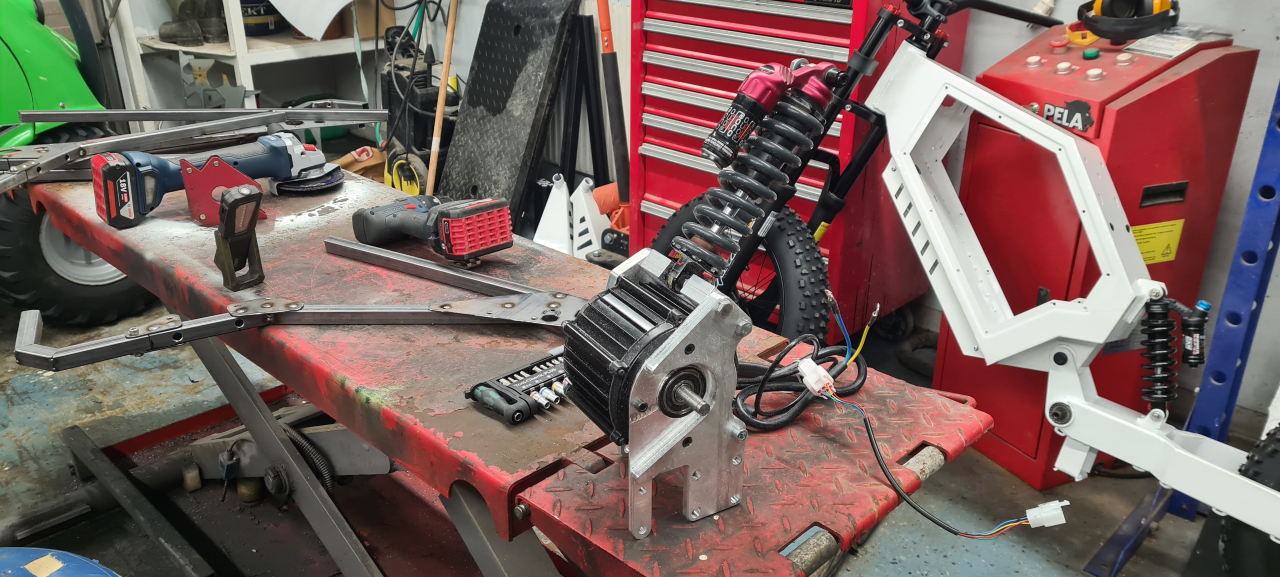
The motor/shock mount is easily removed from the bike with just 9 M8 bolts. This is great for service and painting later on. If I may say so myself it looks frekkin’ awesome! 😀
Making the subframe
I decided to make the subframe from 20×20 square tubing as it’s strong enough, not too heavy, cheap and easy to get.
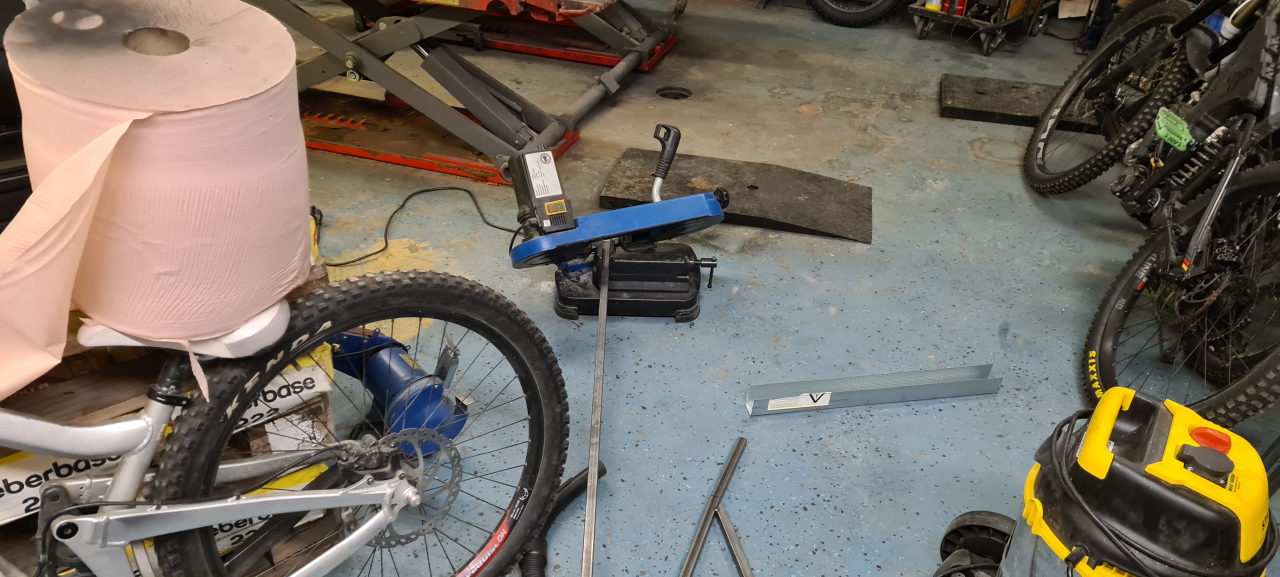
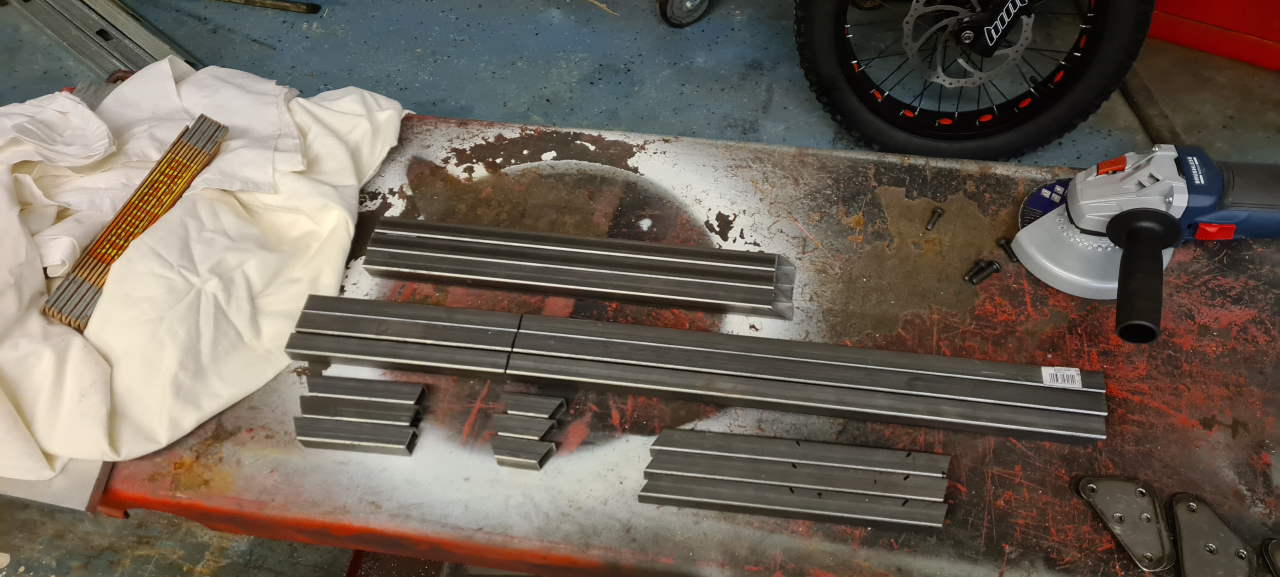
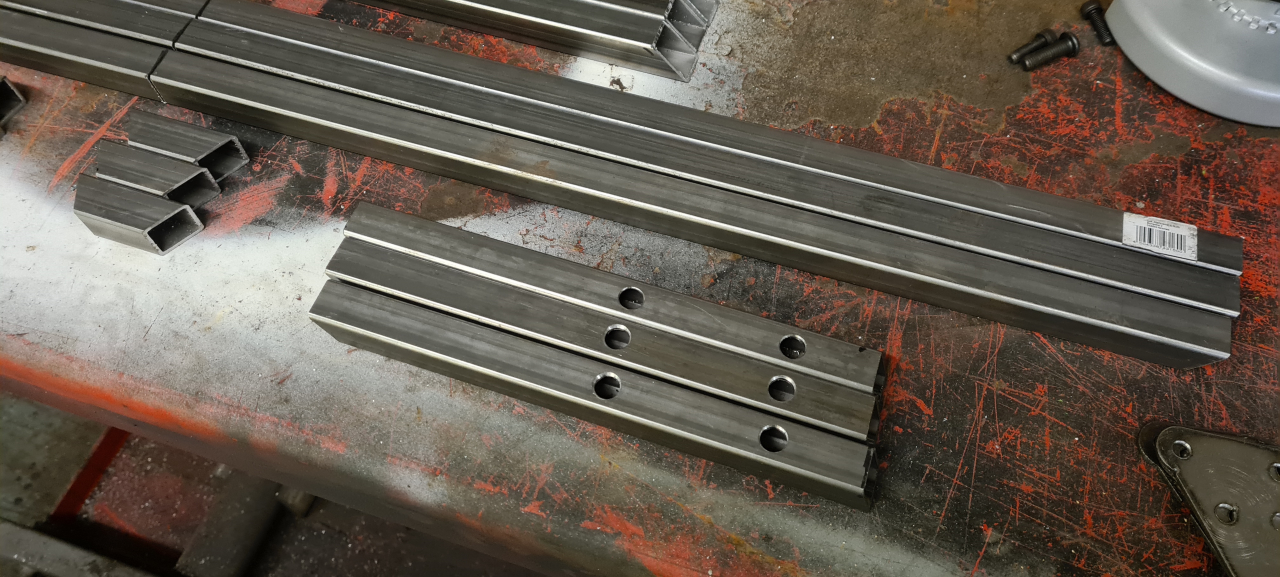
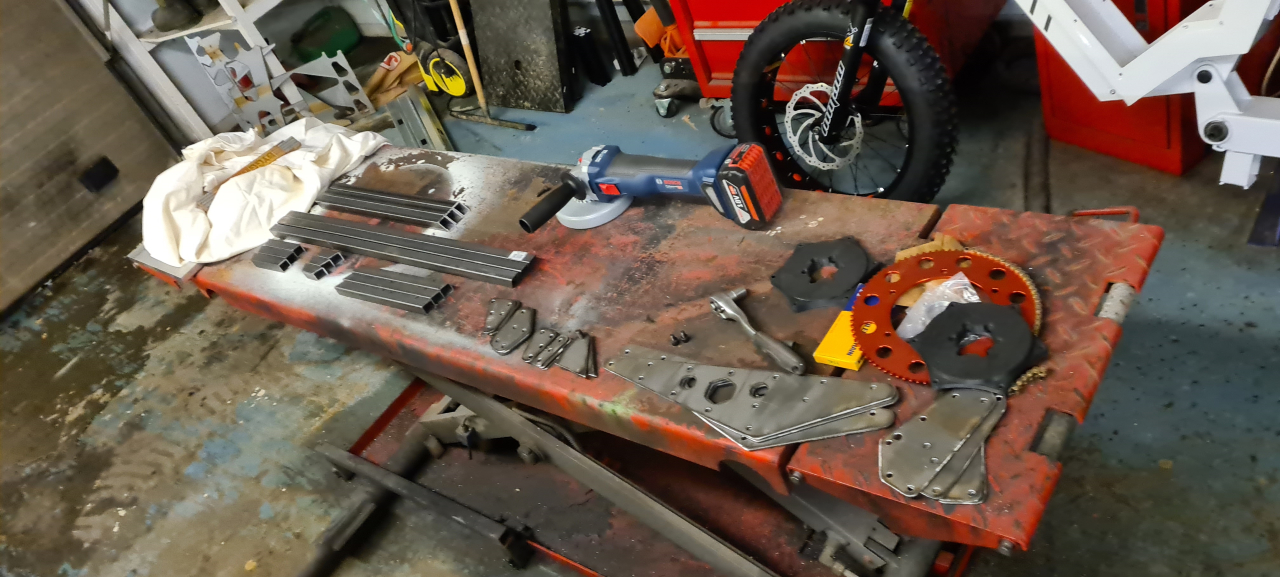
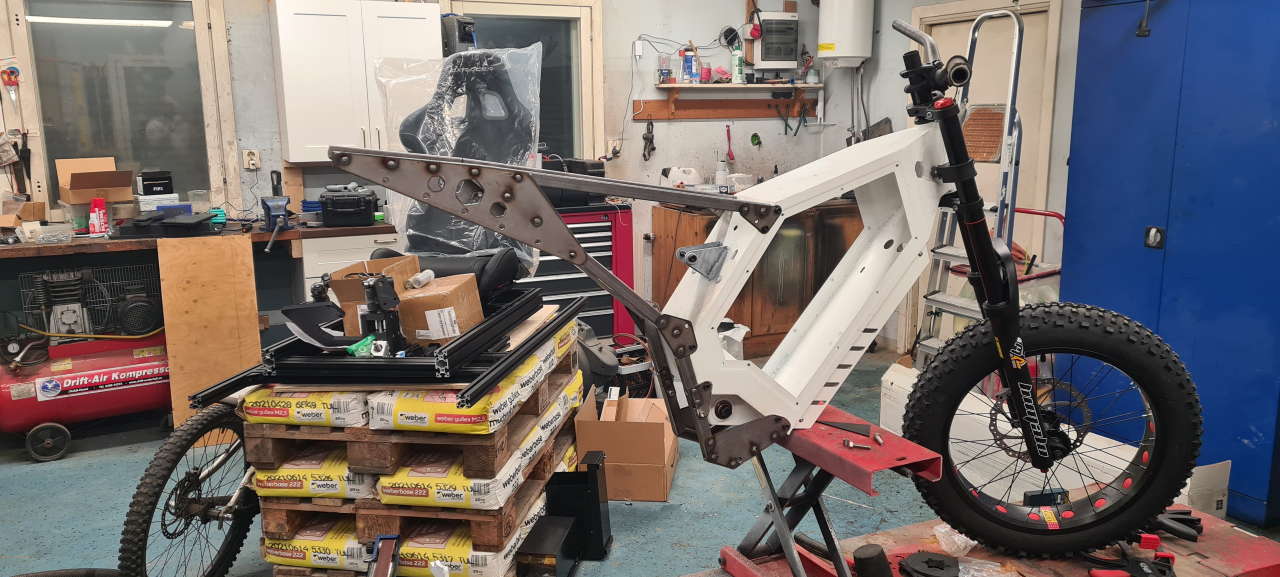
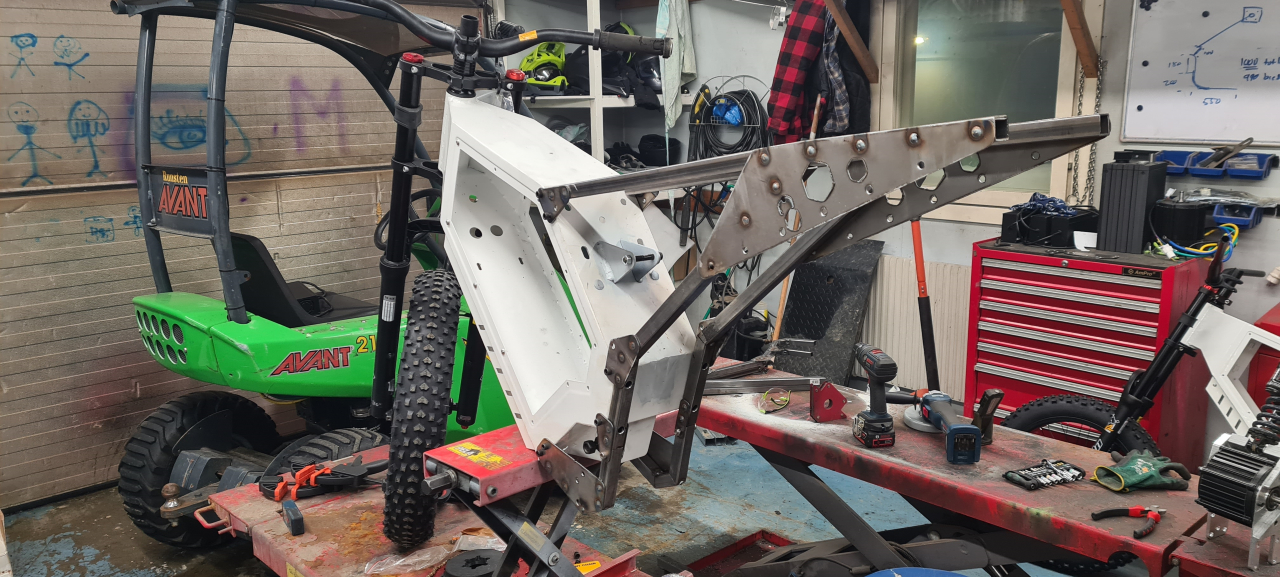
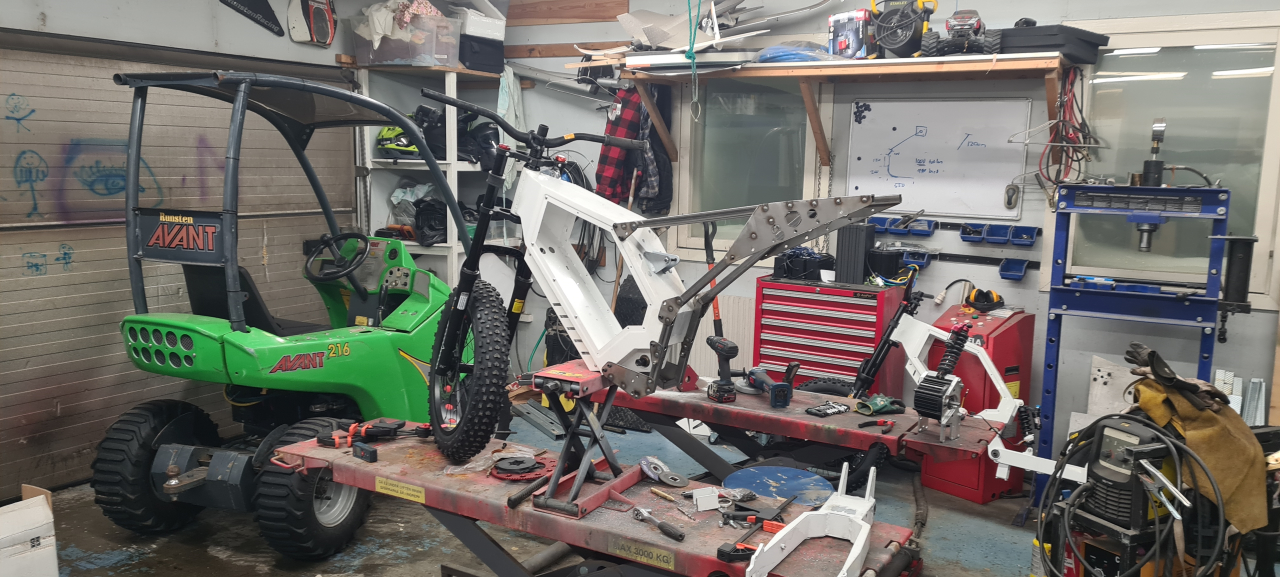
When this was done I just had to quickly weld everything together, drill and tap the mounting holes on the frame and make the joining parts for the subfrtame. The subframe goes under the bottom of the frame to be able to fit the footpegs.
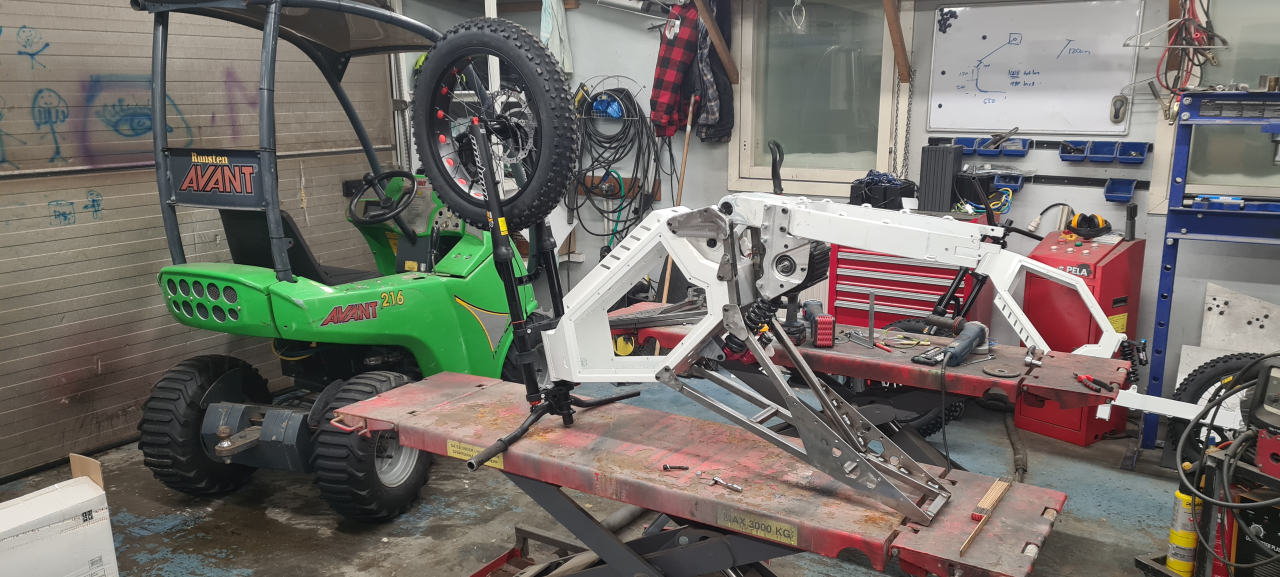
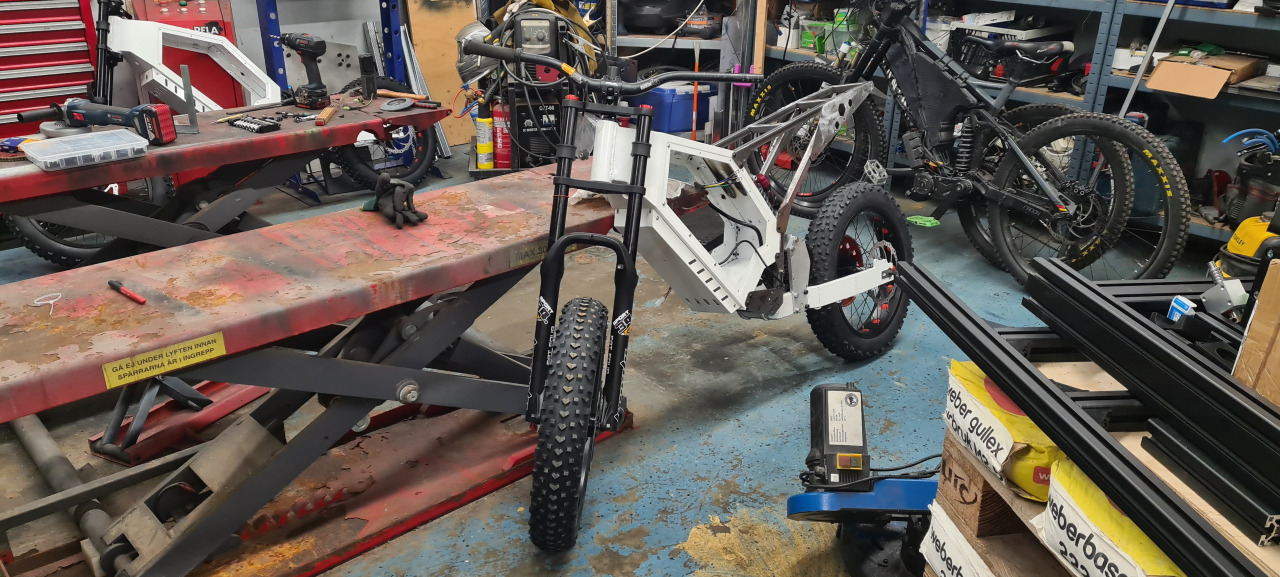
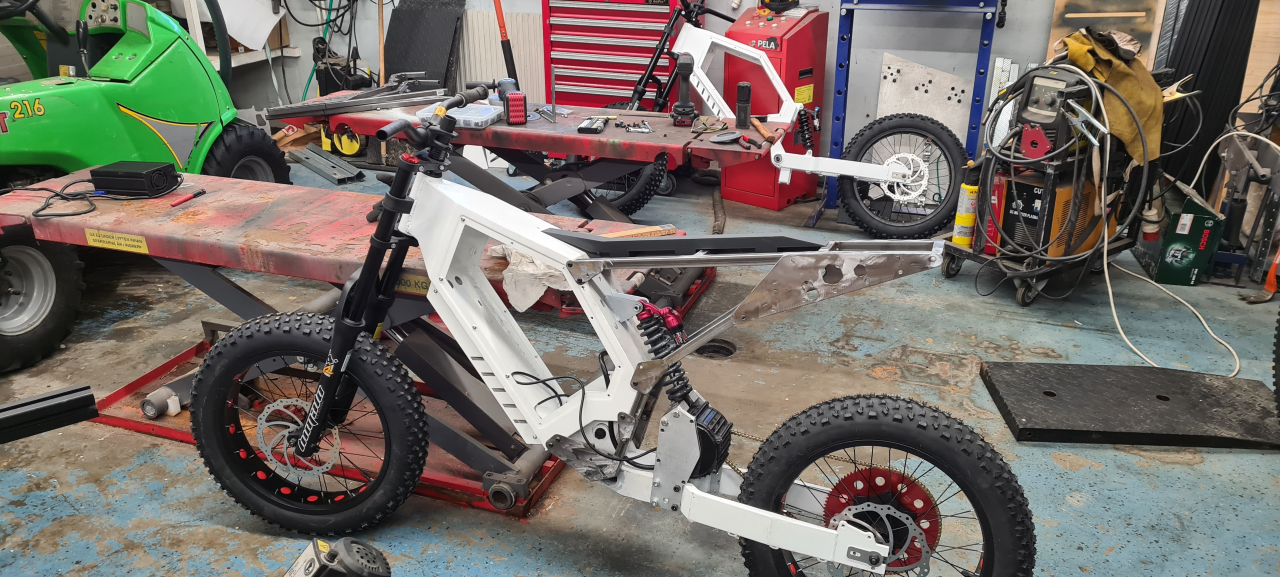
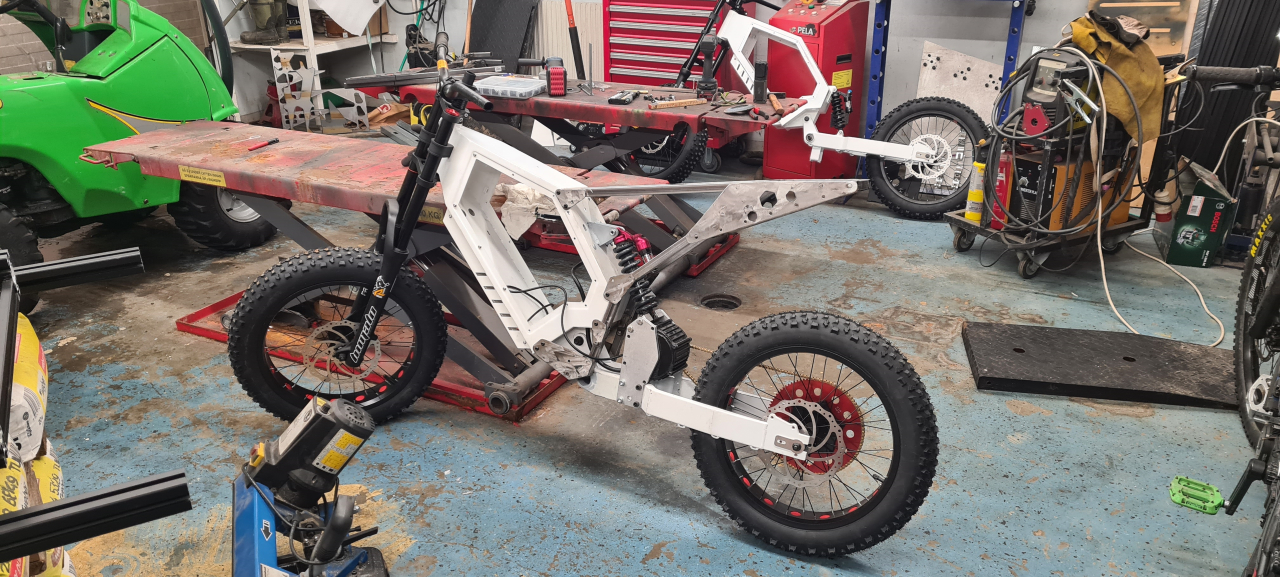
Battery and seat
So, that’s about where we are for now. What’s left is a few fairings, the seat, battery and electrics.. (And the brakes of course)
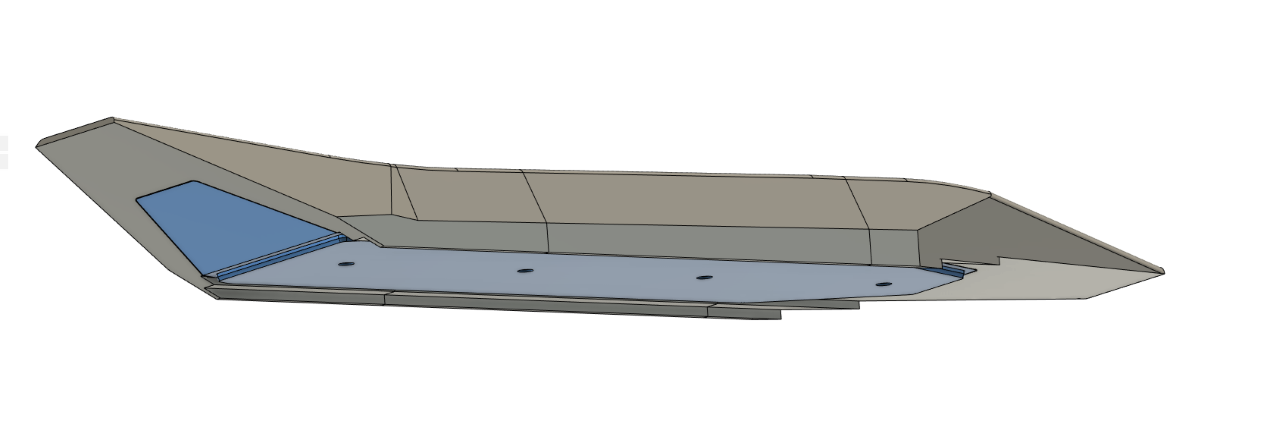
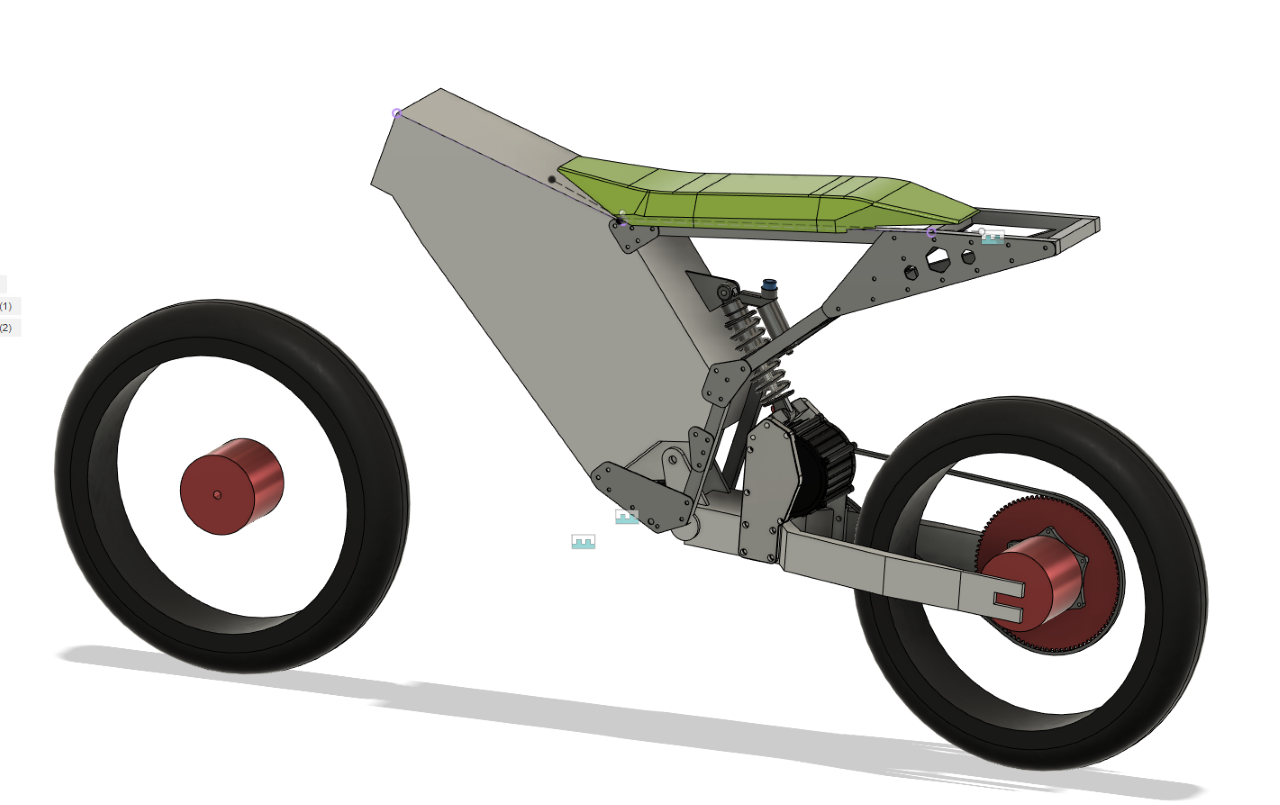
While the 3D-printer is making seat parts I’m finishing up the battery.
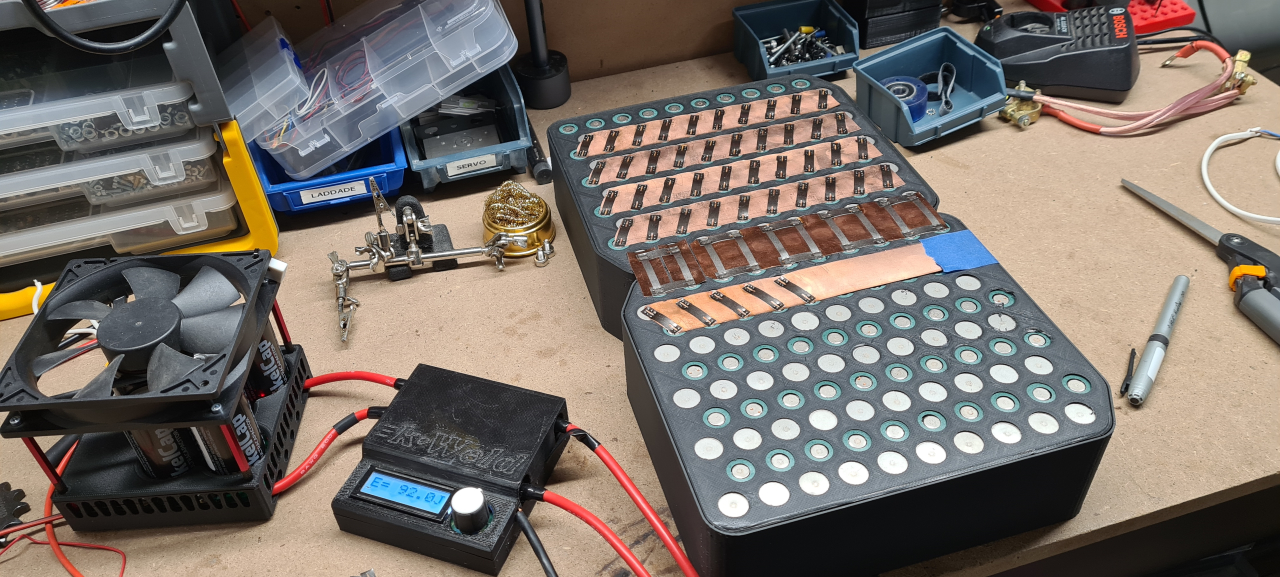
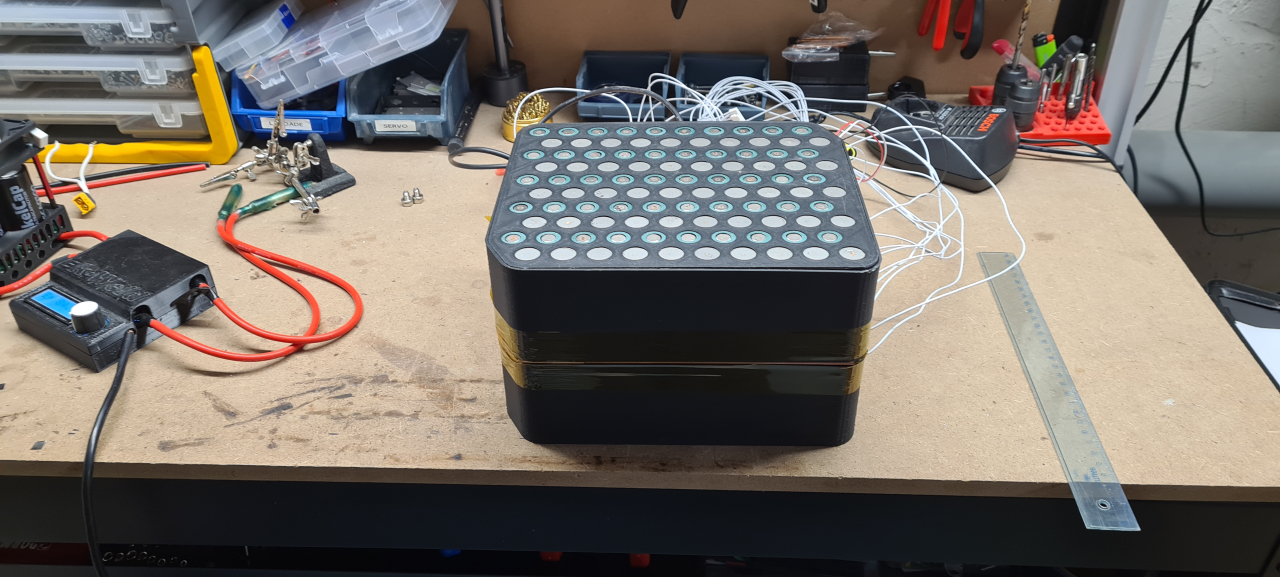
Well, that’s all for now. To be continued.