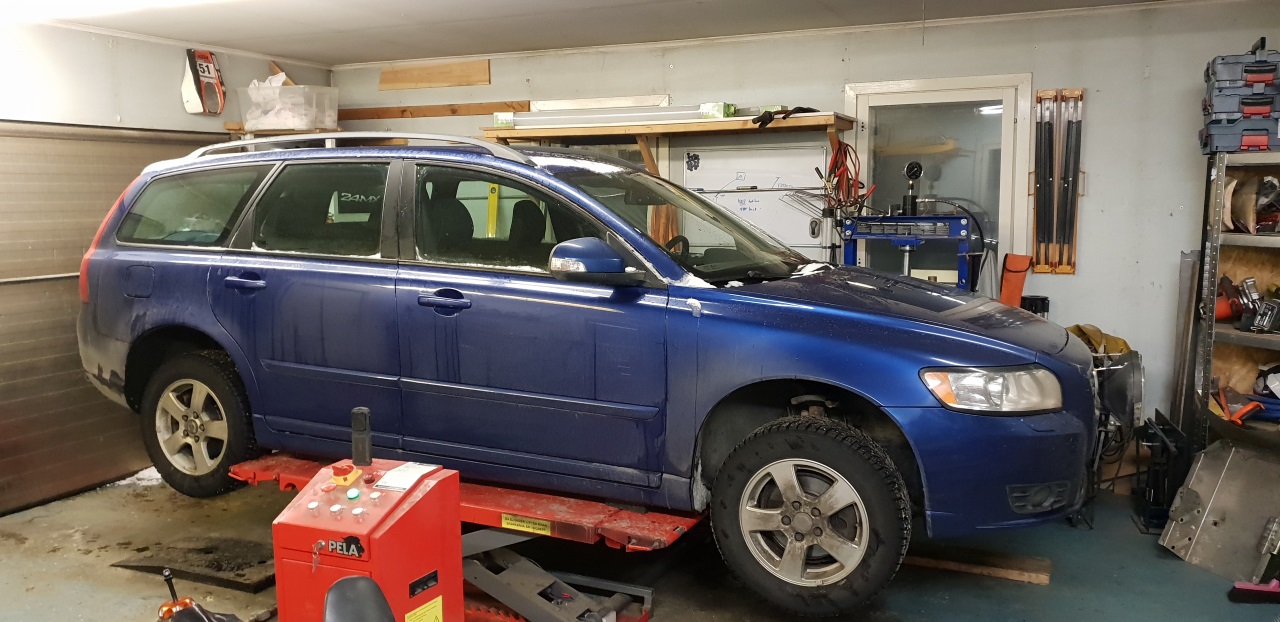
Volvo V50 drive #pålyften
Så var det dags, jag har börjat få felmeddelandet alla volvoägare fruktar, Partikelfälla igensatt. Bilen kan inte längre regenerera partikelfiltret och motorn vägrar varva mer än 3000rpm. Dessutom känns den mer kraftlös än vanligt – det är ju inget prestandamonster ens när allt är som det ska..
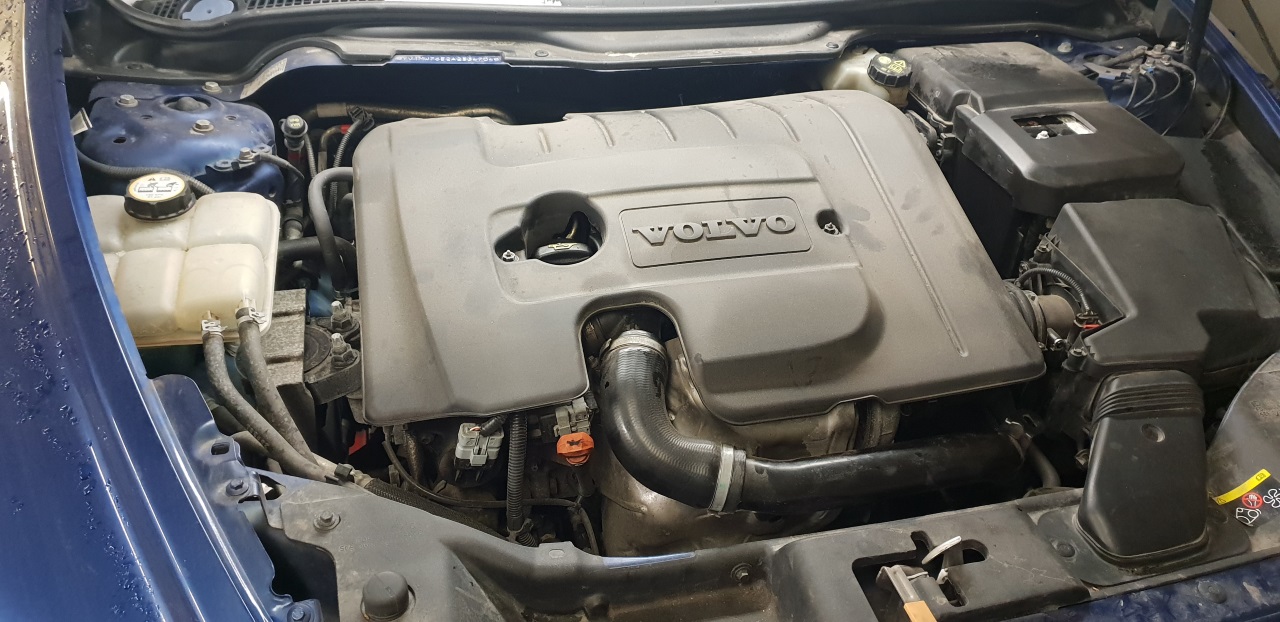
1.6 drive dieselmotor
Så vad gör man när man är för snål för att punga ut med de 16000kr verkstaden vill ha för att byta partikelfiltret, och även är för snål för att köpa ett nytt filter för 6500kr plus moms hos Meca?
– Man googlar, googlar, googlar och kollar lite youtubevideos.. och hittar en lösning som rent teoretiskt skulle kunna fungera, och sen börjar man riva bilen.

Avklädd..
Först avlägsnar man den plastkåpa som täcker motorn och som sitter med 2st 10mm muttrar.
Partikelfiltret är inklätt i en värmesköld som är den silverfärgade klumpen mitt i hopen av alla slangar och turboaggregat och spänner hela höjden av motorutrymmet vertikalt. Den behöver vi plocka ut, så det är bara till att börja öppna slangklammer och lossa luftkanaler..

Luftrör..
Började med att plocka loss alla rör som ligger ovanpå partikelfiltret, men det räckte inte för att komma åt alla fästpunkter och kunna öppna klämman som håller filtret på plats mot turbon..
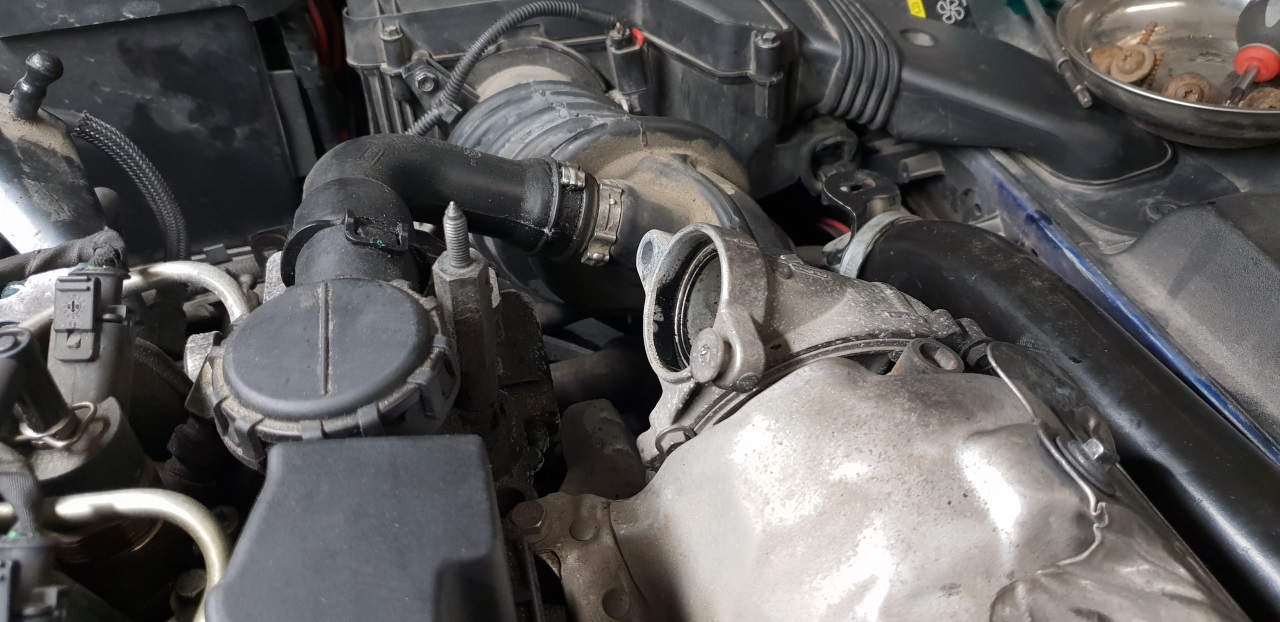
Knepigt montage..
Spenderade lite tid med att lossa plaströret som ligger bakom turboaggregatet. Röret sitter med ett par slangklammer och en 8mm skruv. Sedan sitter där en skruv med insexskalle som är komplett omöjlig att komma åt utan att tillverka diverse specialverktyg, vilket jag inte kände för att göra. Men det visade sig att den bara agerar klämklack och inte behöver lossas. Lös med slangklammer och skruv, och sedan kan man vrida hela röret uppåt och haka loss det från insexskruven, och sedan är det bara att dra rätt ut.
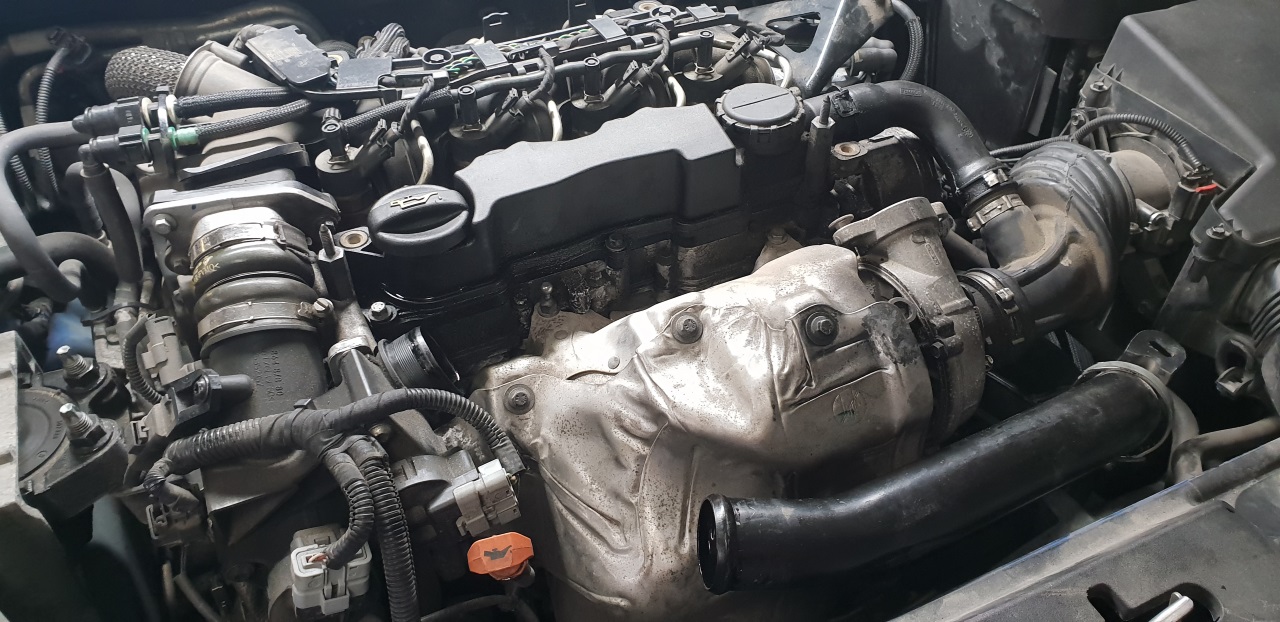
Nu är överdelen av paritkelfiltret frilagd, men för att kunna lossa och öppna värmeskölden för att kunna lossa den från turbon måste det svarta röret längst ner till höger i bild bort. Detta rör måste lossas varje gång man gör ett filterbyte på motorn, så den övre infästningspunkten är enkel att komma åt, men först efter att man avlägsnat luftröret som går mellan luftfilter och insugssida på turboaggregat.
Under motorn sitter metallröret fast i en slang som går från intercoolern, ett klammer som håller en kylarledning och ännu en 10mm hexskruv. Men när man lossat det är det inga problem att lyfta av röret.
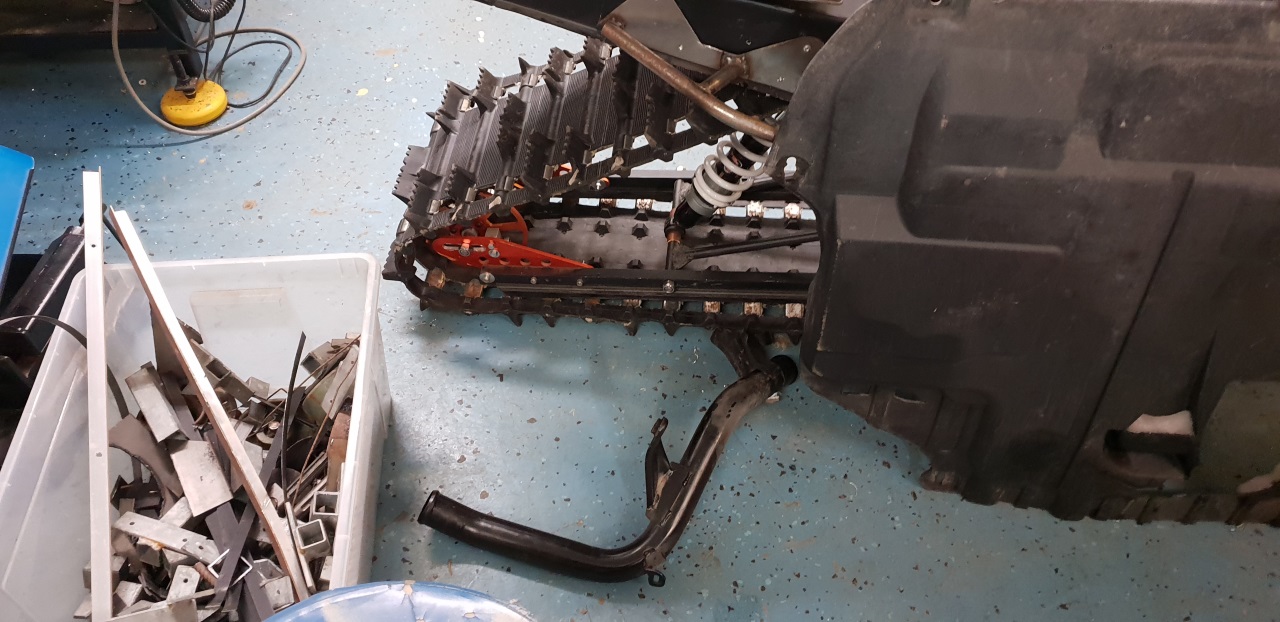
När röret är väck kan man öppna värmeskölden till partikelfiltret..
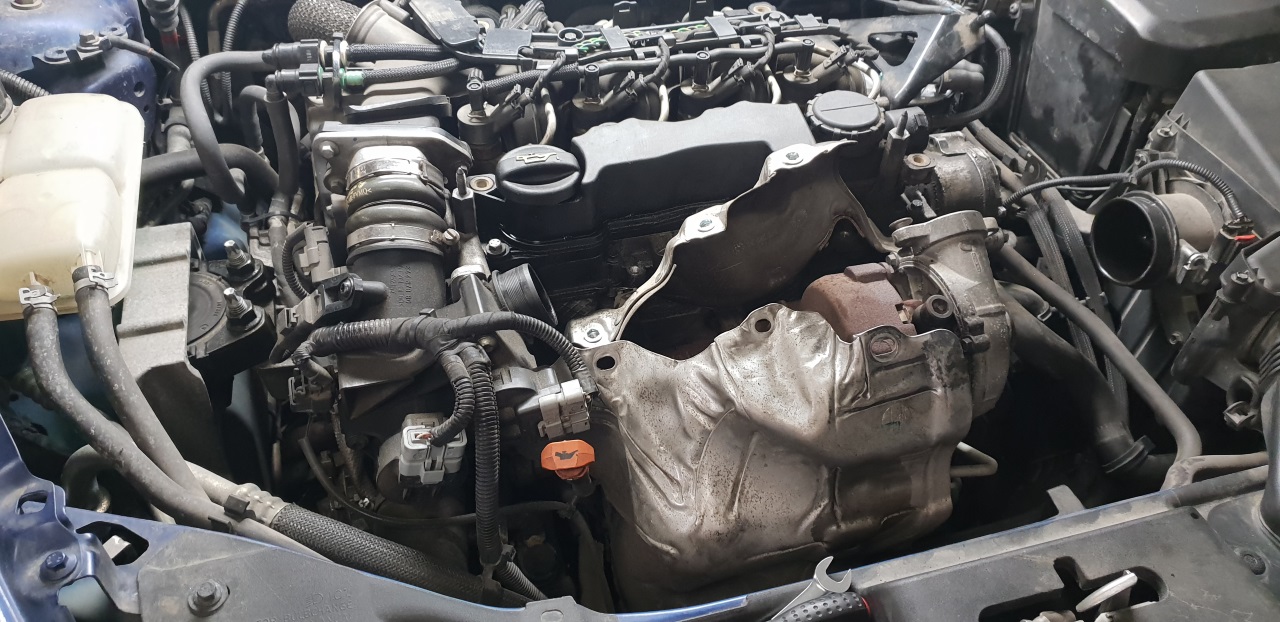
Tre 8mm hexskruvar senare går det att bryta upp värmeskölden tillräckligt för att få tillgång till fästringen som håller filtret på plats..
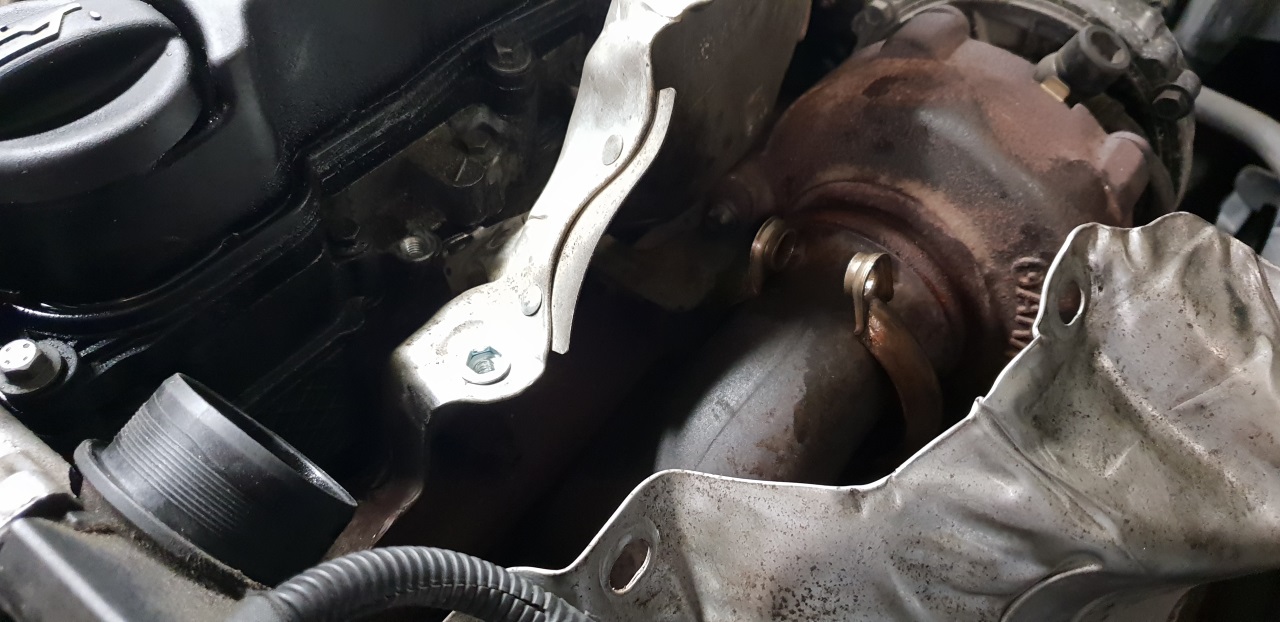
Fästringen sitter i en rätt skum vinkel från fabrik, egentligen helt utan mening. Med en fast 16mm nyckel kan man komma åt att lirka loss den, den ska inte sitta särskilt hårt, och sedan kan man vrida till den så att man får en vettigare vinkel att lossa den från. Efter att ha lossat klämringen och bänt den över flänsen så att den inte längre håller filtret på plats så är det dags att se till att alla anslutningar till filtret hänger med ut.
Jag testade att lossa tempgivaren från filtret, men den satt stenhårt, så istället kopplade jag ur givaren ur motorn och lät den följa med filtret ut..

Urkopplad tempgivare för partikelfiltret
Utöver tempgivaren är filtret anslutet till en difftrycksgivare som sitter monterad på sidan av batterihållaren.
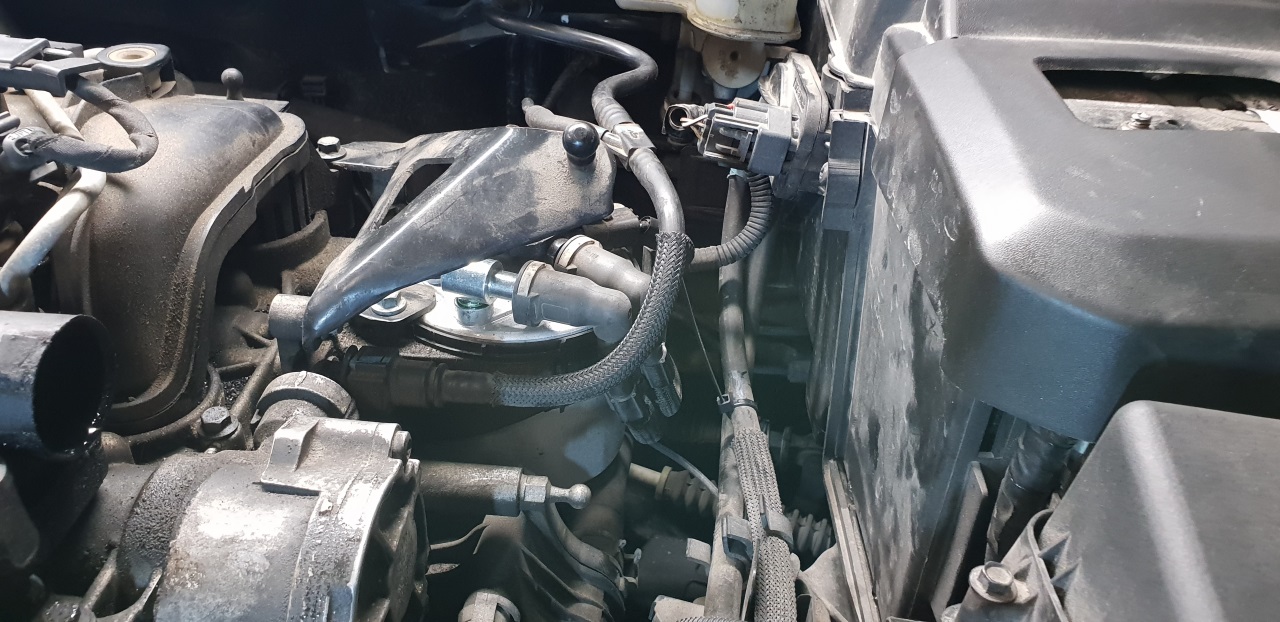
Hela givaren sitter fast med en Torx-skruv och det är mycket enklare att lossa tryckslangarna från givaren om man plockar loss hela givaren från sitt fäste. Först lossar vi kontakten så att vi inte har någonting som håller givaren på plats.
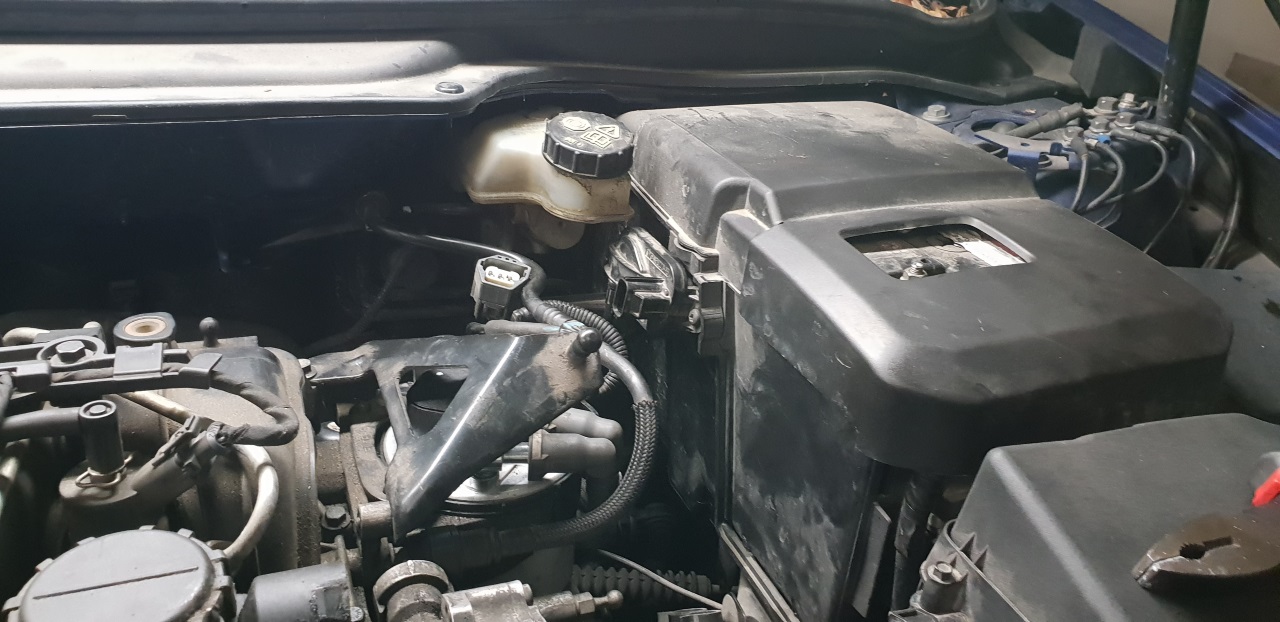
Givare losskopplad
För enkelhets skull hängde jag tillbaka givaren när slangarna var frånkopplade, så slipper man hålla reda på den. Jag märkte upp slangarna för att minnas vilken slang som gick var på givaren, men slangarna är faktiskt av olika diameter så de passar bara på ett sätt.
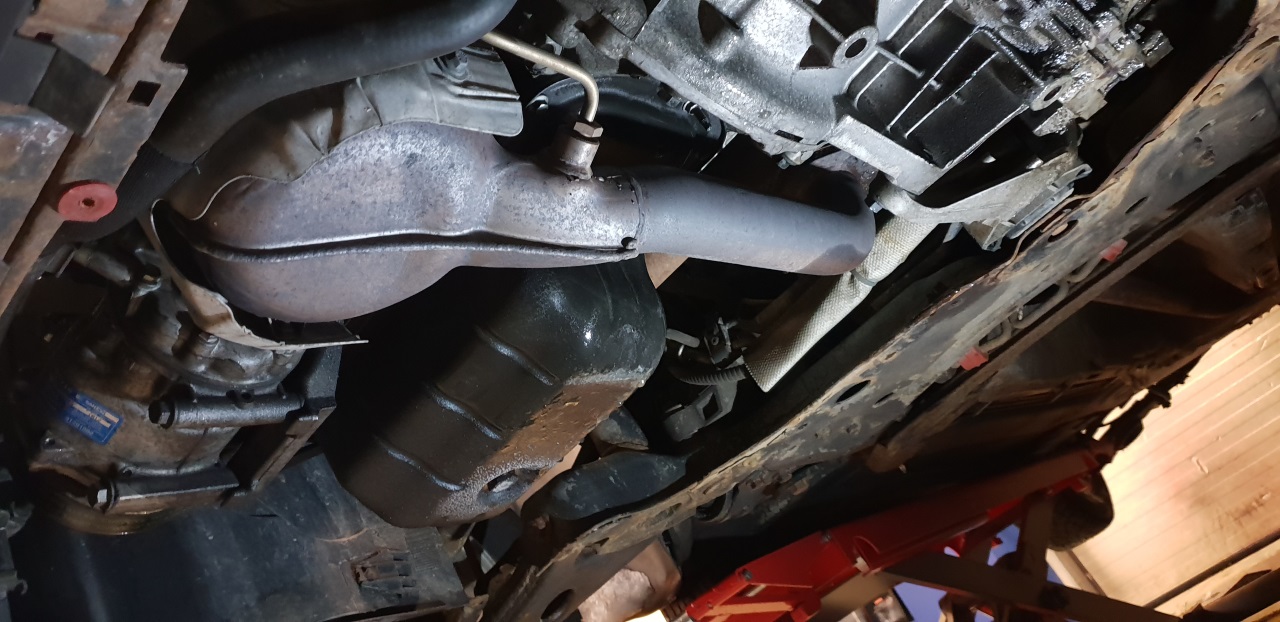
Undermotorn
Då återstår bara den nedre infästningen av partikelfiltret, längst bort i bild, där det sitter fast i avgasröret. Eftersom att vi snackar avgas så kärvar det ju en del, men mutterpicka och 5-56 löser alla dylika problem. När bakre fästet är bortskruvat får man knyckla till värmeskölden lite i överkanten så att den ska kunna följa med filtret ut under bilen utan att haka i allt möjligt på vägen ner.. men skölden är mjuk och enkel att återställa sen, så knyckla på bara.
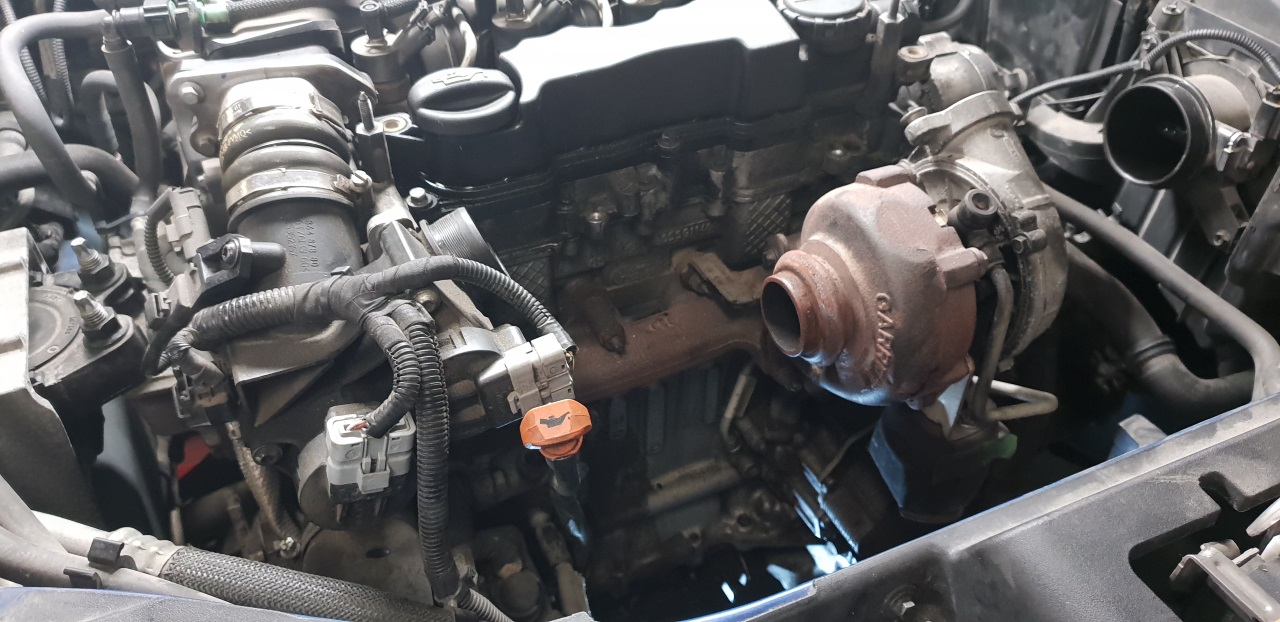
Heureka
Och då var den knepiga delen av arbetet utfört, partikelfiltret finns inte längre i bilen utan..
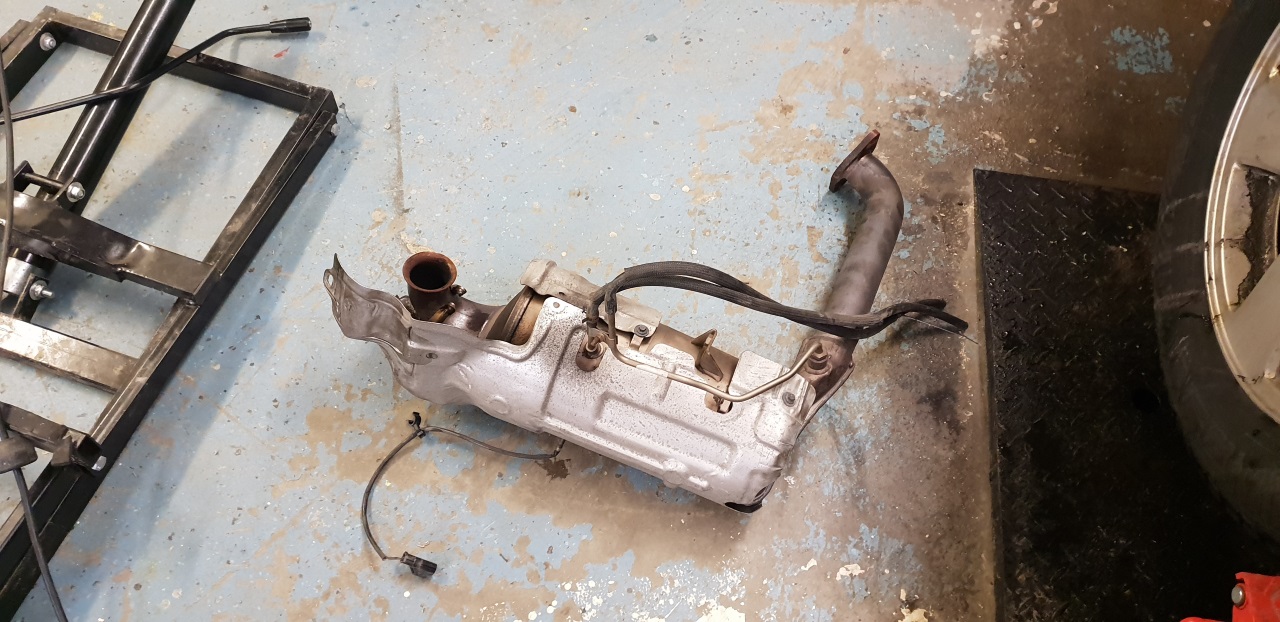
.. ligger löst på golvet. Nu kan man ju tänka att – när man lika gjort allt detta jobbet så kan man ju slänga i ett nytt filter och glömma problemet, men så långt har jobbet bara tagit ett par timmar och jag känner att jag iallafall vill försöka spara lite pengar, även om det innebär att göra om allt detta – vilket ju alltid är enklare andra gången ändå.. Så vi kör på!
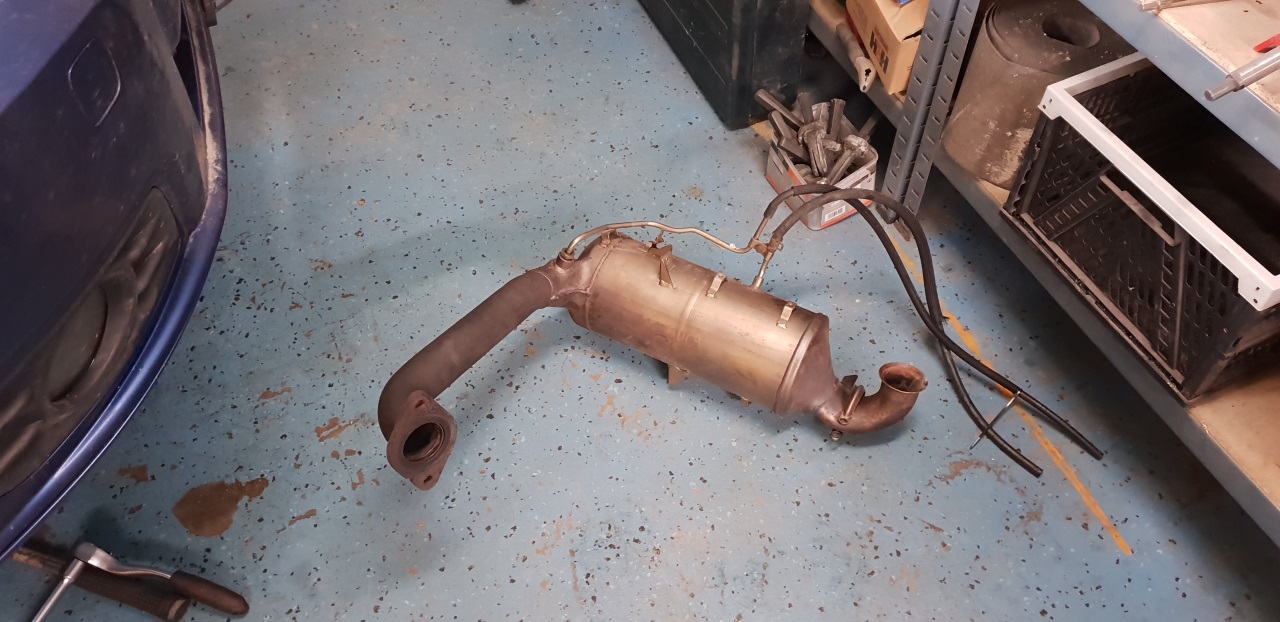
För att göra arbetet med filtret enklare skruvade jag loss hela värmeskölden, det är bara 4 skruvar till eller nåt sånt så det går fort. Jag plockade även lös tempgivaren. Sedan började experimenten..
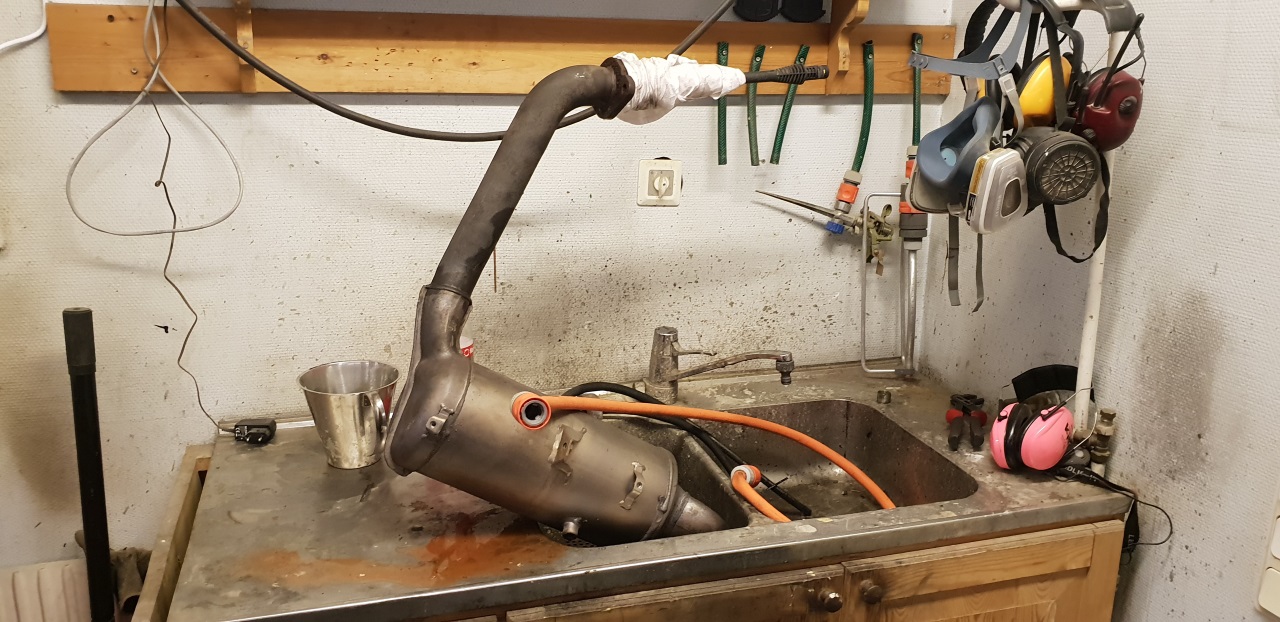
DPF cleaning DIY
Jag började med att skölja ur filtret med en vattenkanna. Vattnet rann knappt genom, och det som kom ut var inte vackert.. En brunsvart sörja som såg väldigt kletig ut. Så jag hällde i en liter T-röd och väntade en stund för att spriten skulle få göra sitt jobb. När man gör detta så häll alltid vätska bakifrån i systemet, dvs häll i på avgassidan och ur på turbosidan. Då trycker man ut sotet kortaste vägen istället för att försöka trycka allt genom filtret.. kanske inte spelar någon roll, men så tänkte jag.
Efter att jag hällt ur spriten kopplade jag in partikelfiltret på högtryckstvätten enligt bilden ovan, och spolade och spolade.. Det gick väldigt tungt, och det är inte lätt att utsätta själva filtret för någon kraft såhär, så jag kopplade på kompressorn på tryckgivarslangen som sitter på samma sida av filtret som avgaset och körde på 10 bar lufttryck.. nu började det hända saker. Kombinationen vattenfyllt filter och 10 bar övertryck fullkomligen spottade sotvatten ur filtrets inlopp.
Jag upprepade proceduren att vattenfylla filtret och trycka ur med högtryck tills dess att vattnet som kom genom filtret var klart, och jag kunde hälla vatten genom filtret med mycket mindre motstånd än tidigare. När jag var färdig kunde jag täppa till utloppet med handflatan och trycksätta utloppssidan med kompressorn och få all luft att gå genom filtret och ut genom inloppet utan att luft smet förbi handen och genade. Stor skillnad mot från början alltså.
Jag slutade fylla på vatten och blåste filtret torrt tills det slutade rinna vatten när jag pustade luft genom, och sedan tog jag min mapgasbrännare och värmde upp filtret så att vattnet som var kvar ångade bort. Fick säkert inte bort allt, det är inte jätteviktigt, men jag gjorde så gott jag kunde.
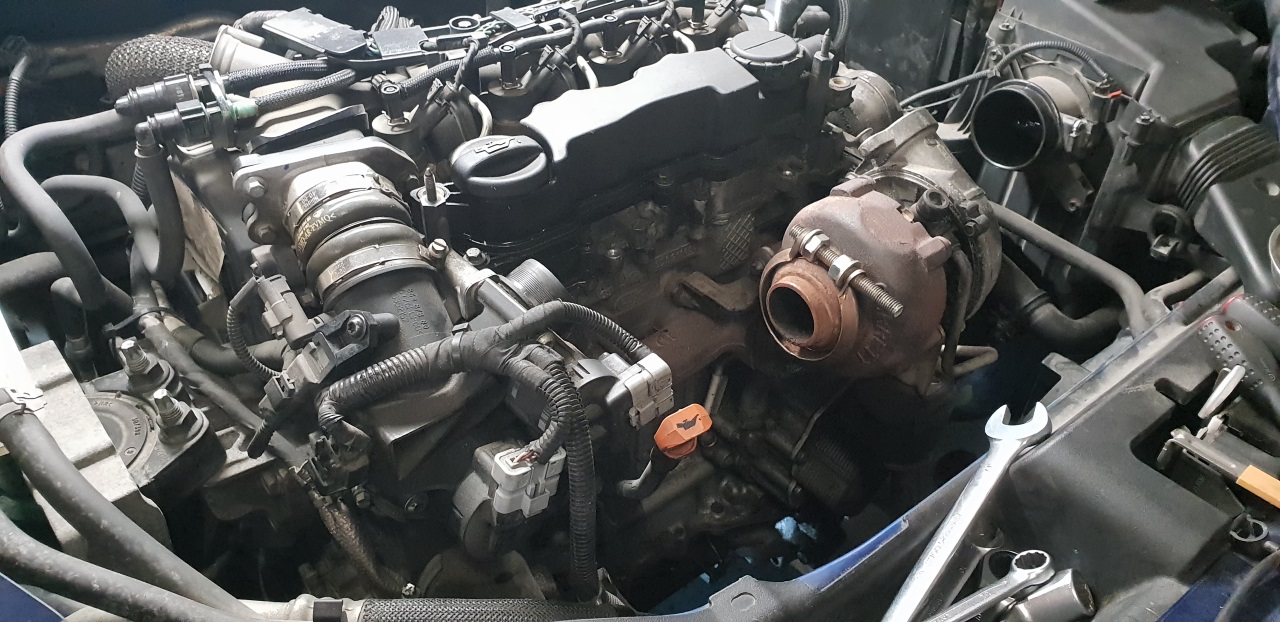
Efter detta rengjorde jag det jag kom åt på motorn när filtret var borta och påbörjade återmonteringen.
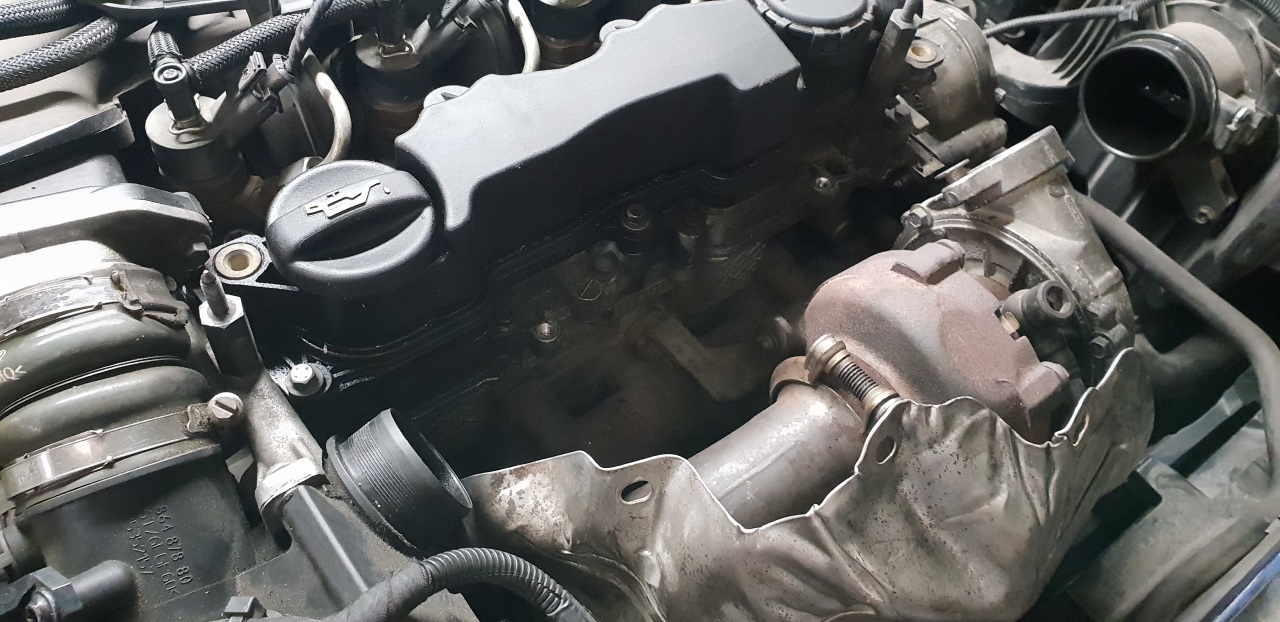
Det var inga problem alls att lyfta filtret på plats och jag bestämde mig för att lämna fästklämringen i den här vinkeln istället för den skumma vinkel den hade från början. Det är enklare att komma åt, och det är inte ivägen för någonting på det här viset, så varför inte.
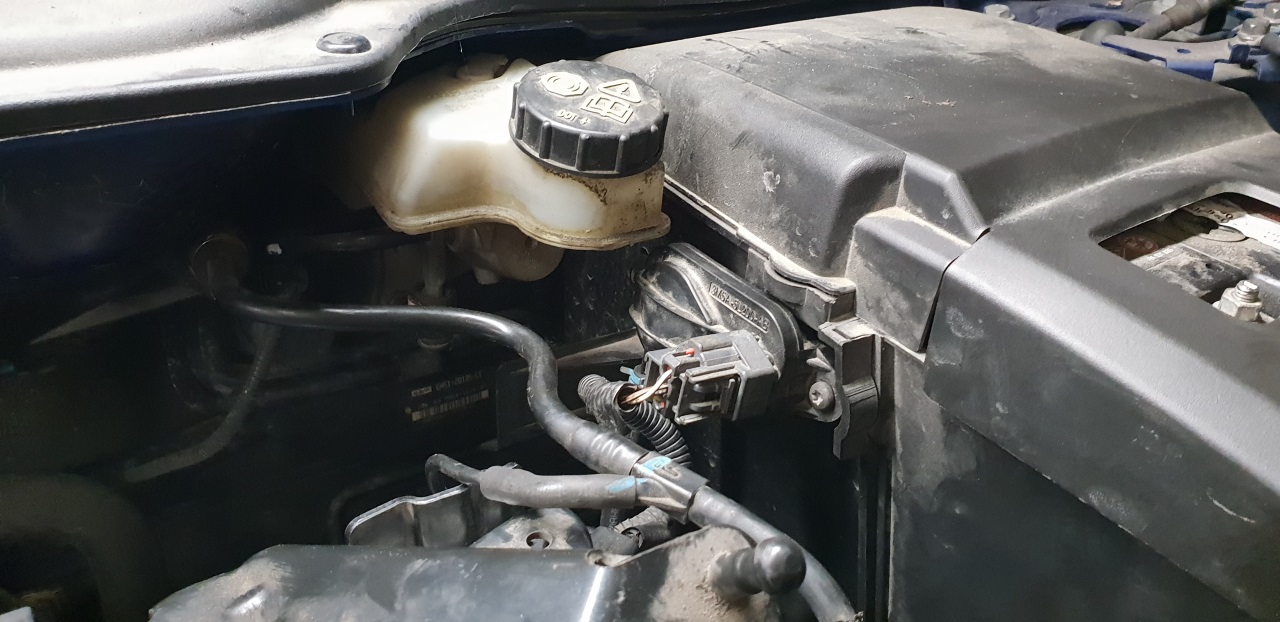
Kopplade i diftrycksgivaren, rätt slang på rätt plats, och skruvade fast den.
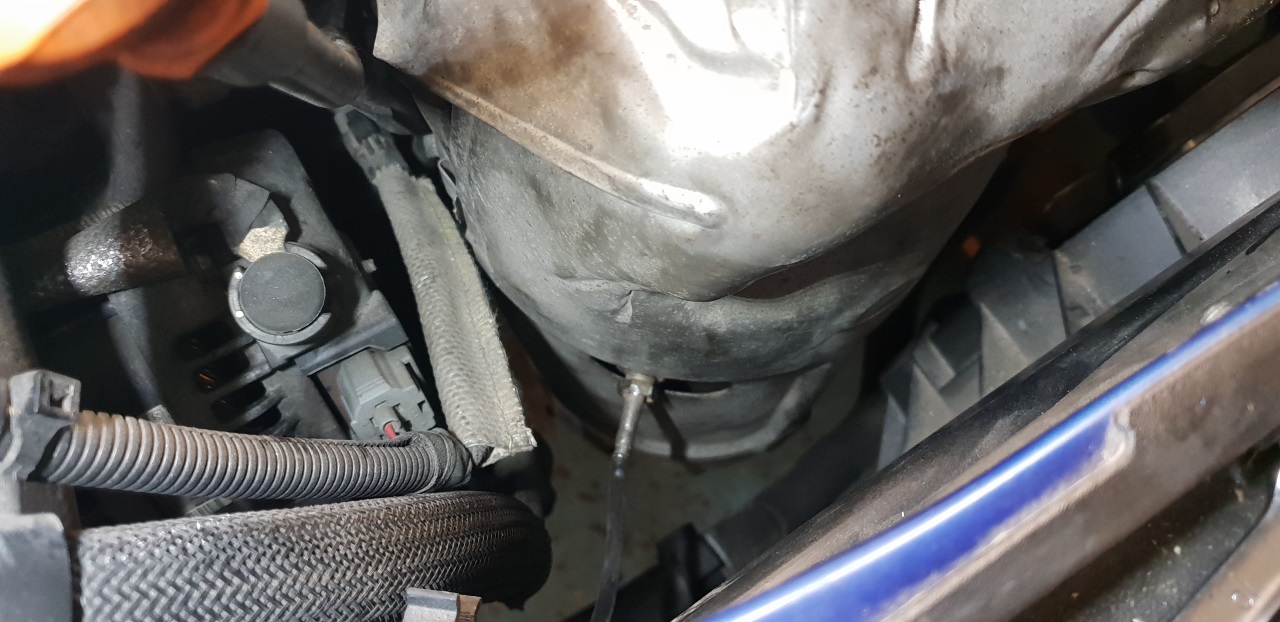
Avgastempgivaren plockade jag ur innan jag började vattenfylla filtret, och den återmonterades nu.
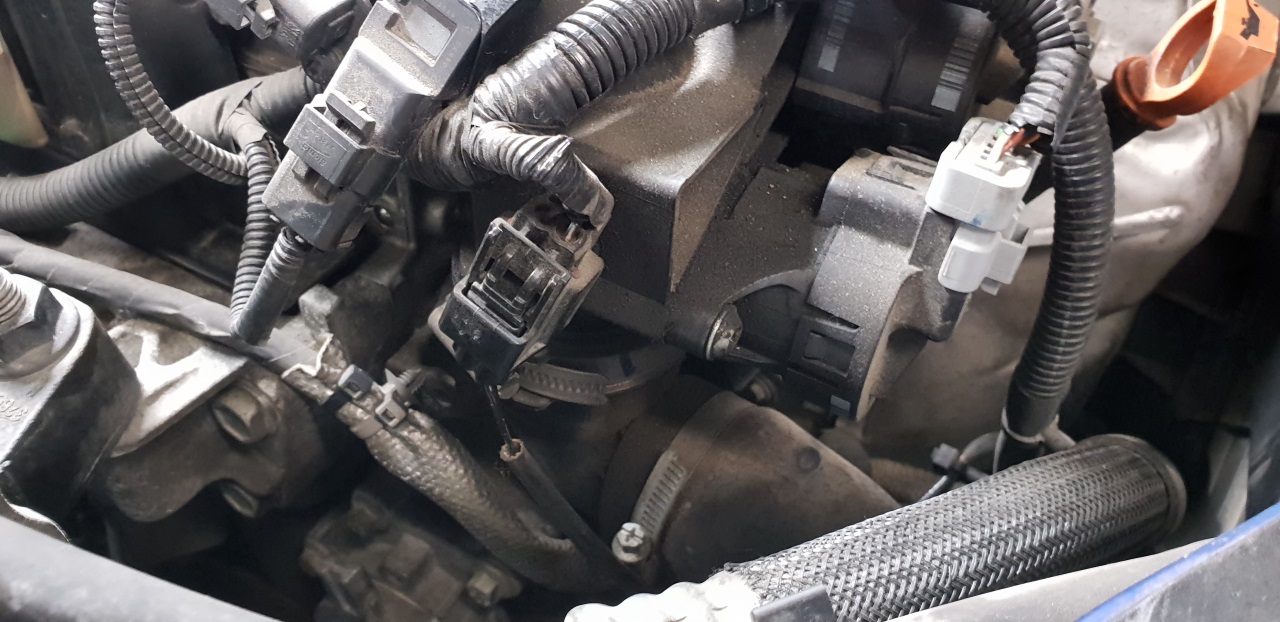
.. och kopplades in.
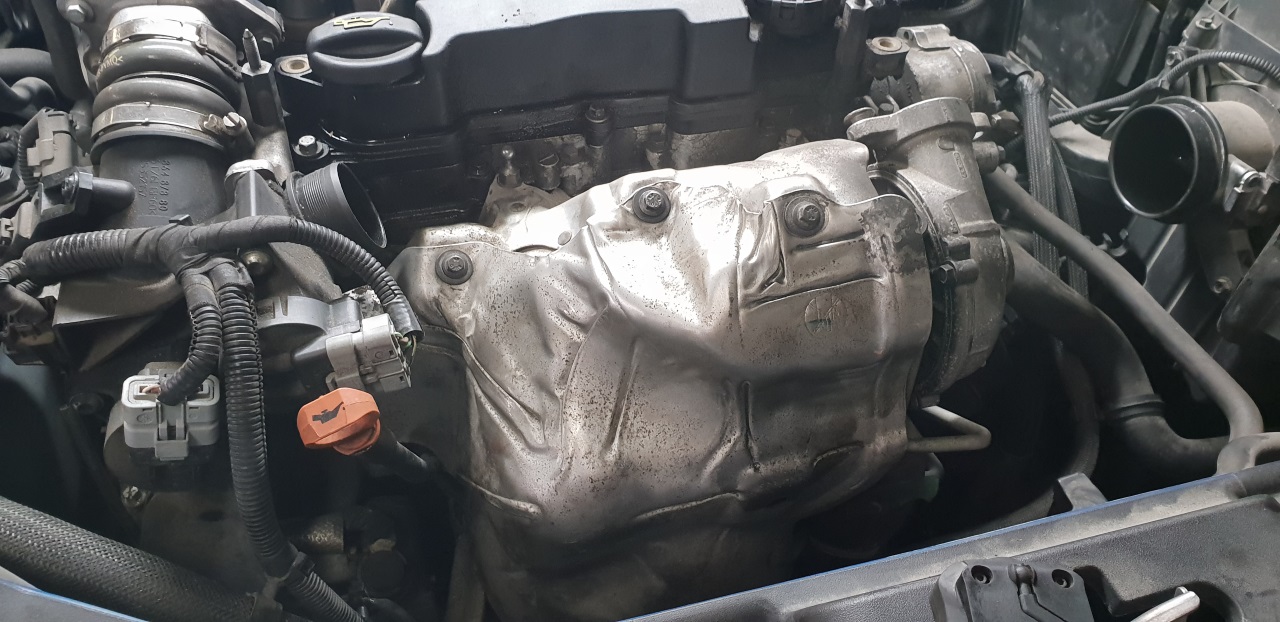
Återställde och skruvade ihop värmeskölden igen..
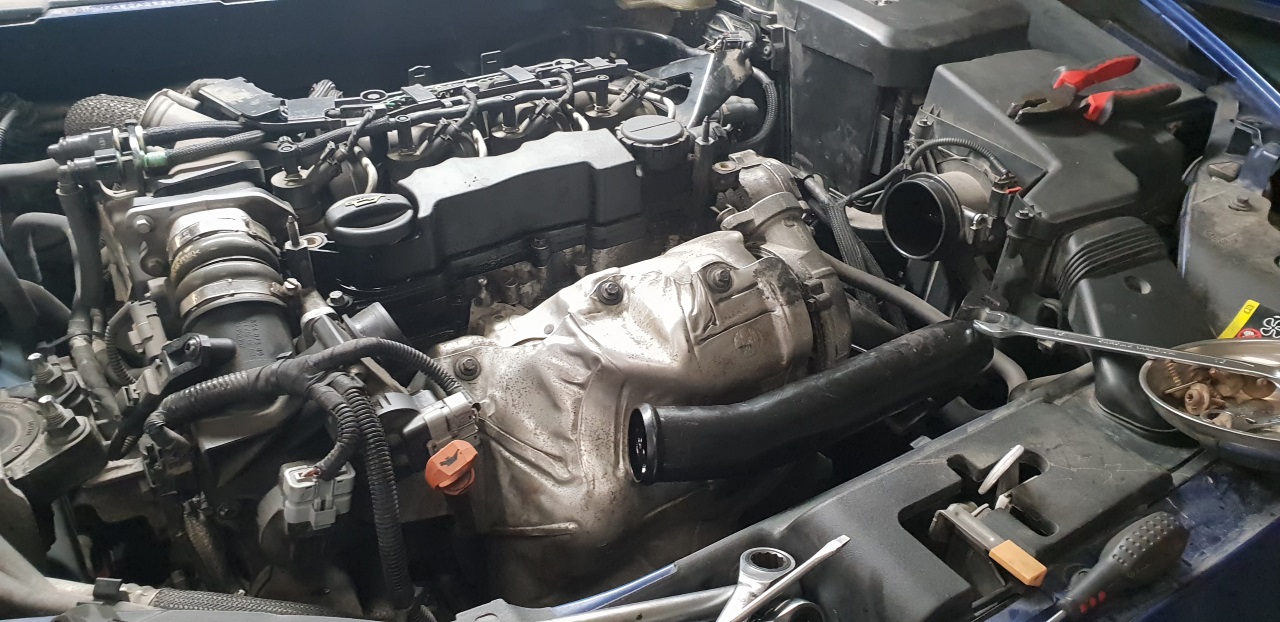
.. monterade metallröret för tryckluft, och sen missade jag att fota resten av slangarna som jag skruvade tillbaka.
Resultatet då?
– När jag startade upp bilen och kopplade upp Vida var samtliga tidigare partikelfilterlarm gröna. Jag rensade felkoder, nollstälde timräknaren för partikelfiltret, och helt plötsligt gick motorn bra igen. Tog ut bilen på en testtur, och den började larma för partikelfiltret igen och gick i limp-home läge.. men eftersom att jag troligen inte fått ut allt vatten ur filtret när jag rengjorde det körde jag vidare och varmkörde bilen ordentligt. Stannade och nollade felkoder och efter det återkom de inte. Nu har jag kört bilen ett par dagar efter detta och den går klockrent. Inga larm, inget begränsat läge och inga bekymmer.
Det kanske är för tidigt att dra några slutsatser ännu, men allt som allt tog detta 4 timmar att göra hemma i garaget. Jag kommer att uppdatera inlägget här ifall jag får några nya partikelfilterfelkoder, så vi får se vad som händer. Hittills har jag iallafall inte förlorat mer än en kväll i garaget på denna fix, och det har jag råd att gambla med. 🙂