Bilen börjar ha gått 24000 mil – och då är det enligt boken dags att byta kamrem. Har gruvat mig lite för detta men nu har bilen tjatat så länge att det måste ordnas.
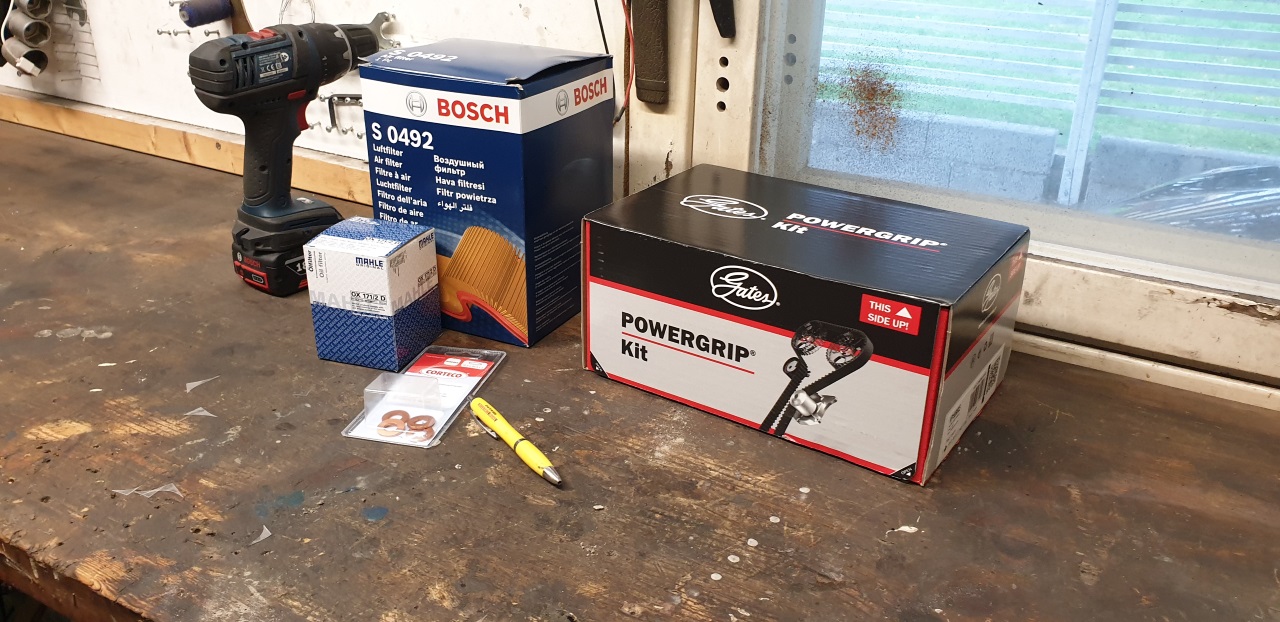
Beställde som vanligt alla delar från Meca i Skellefteå med sedvanlig snabb leverans och nu fanns det ingenting att skylla på längre, så in med bilen i garaget..
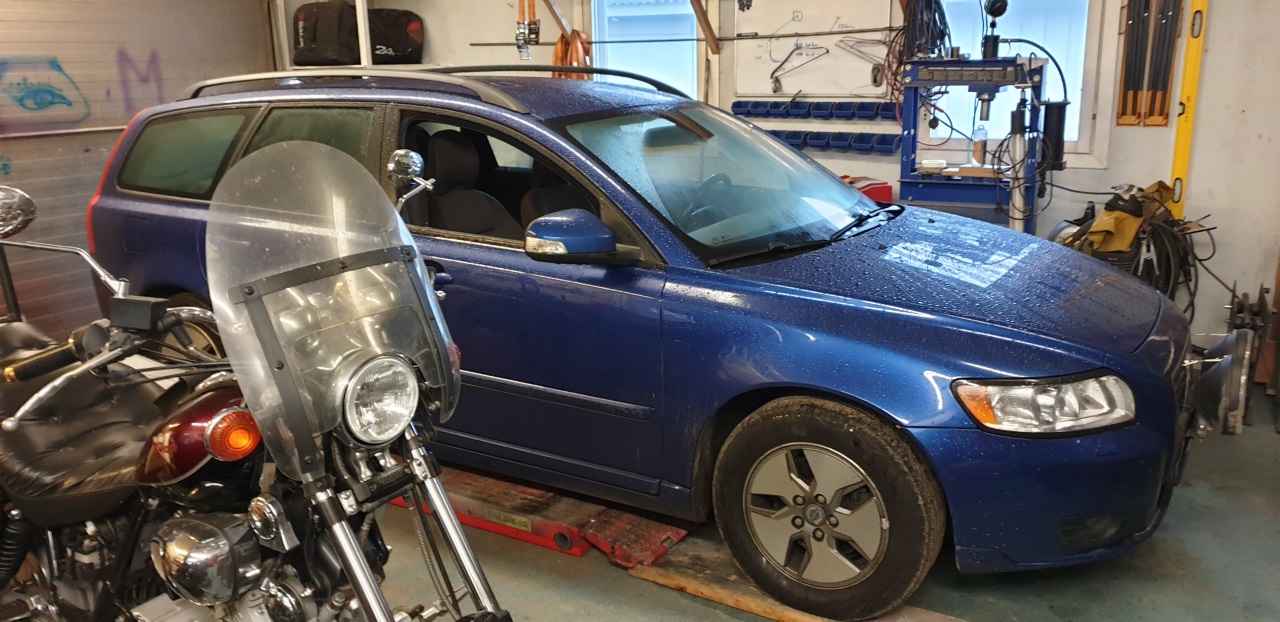
Den här gången tänkte jag göra’t ordentligt och demontera det som behöver demonteras innan jag börjar slita i remmar för att ha utrymme att arbeta i bilen. Förra gången jag bytte kamrem försökte jag gena och demontera så lite som möjligt, vilket gjorde det extremt bökigt att komma åt alla delar man måste byta och justera.
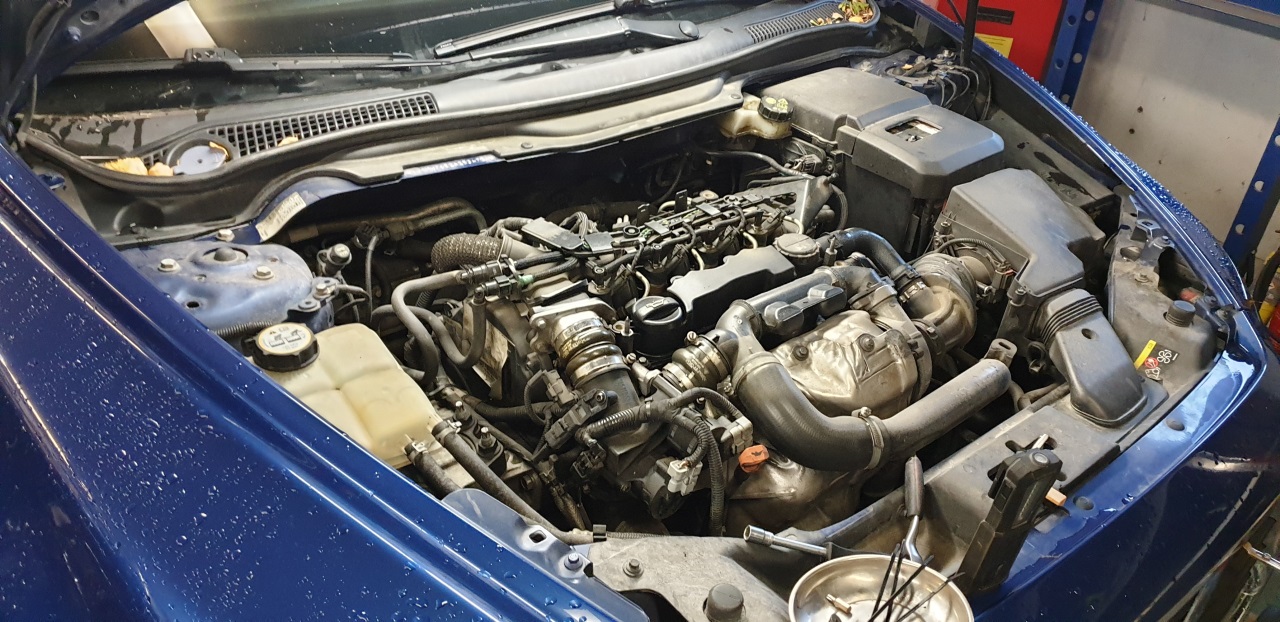
Först demonderade jag plastkåpan på motorn och hasplåten under.

Efter det demonterade jag innerskärmen, vilket bara var 2st 10mm plastmuttrar och ett antal torxskruvar, så det gick snabbt och enkelt. Den var förvånansvärt enkel att återmontera med.
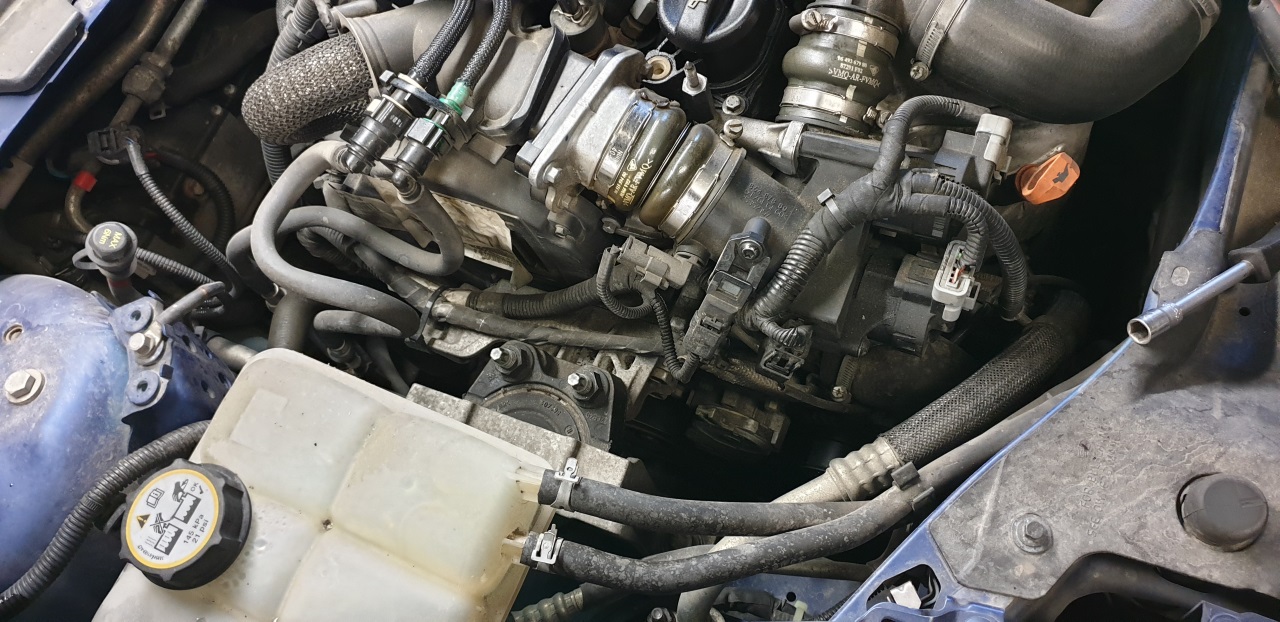
Här ser man vad vi har att arbeta med. En del prylar som behöver bort för att vi ska komma åt, men ändå inte så farligt.. så vi börjar uppifrån:
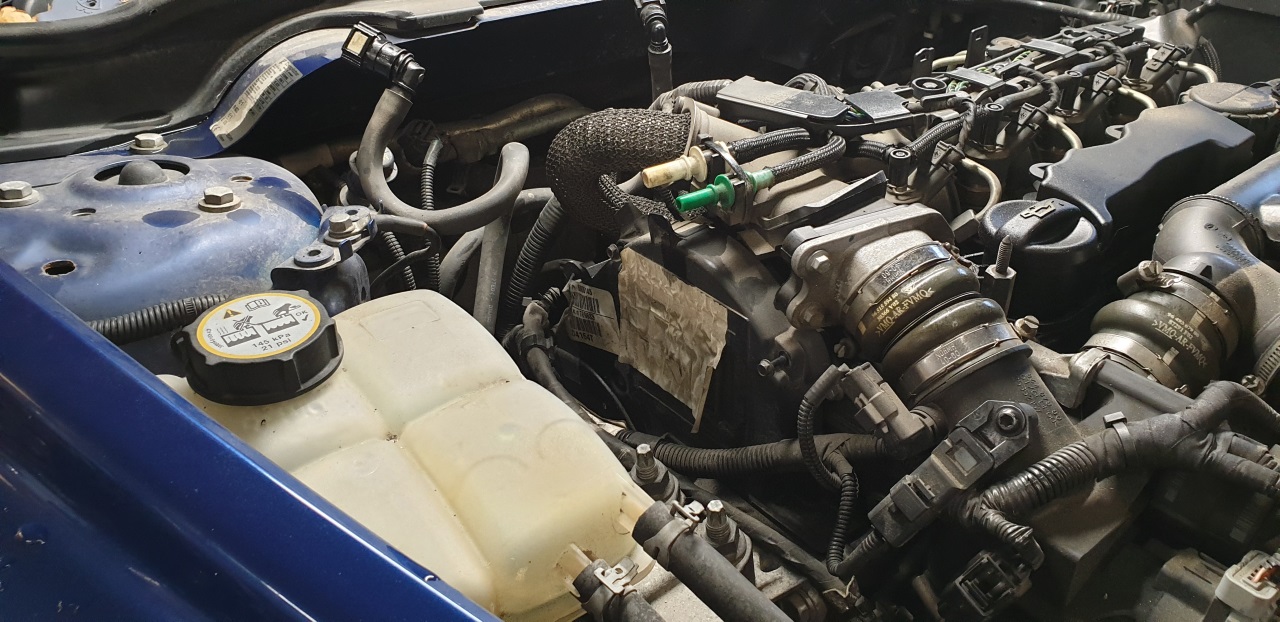
Hakar loss dieselledningarna och diverse elkablar som ligger ivägen. Bränsleledningarna går enkelt att lägga åt sidan, men elkablarna får vi jobba runt då det är för många kontakter att hålla reda på för att det ska vara värt att lossa dem.
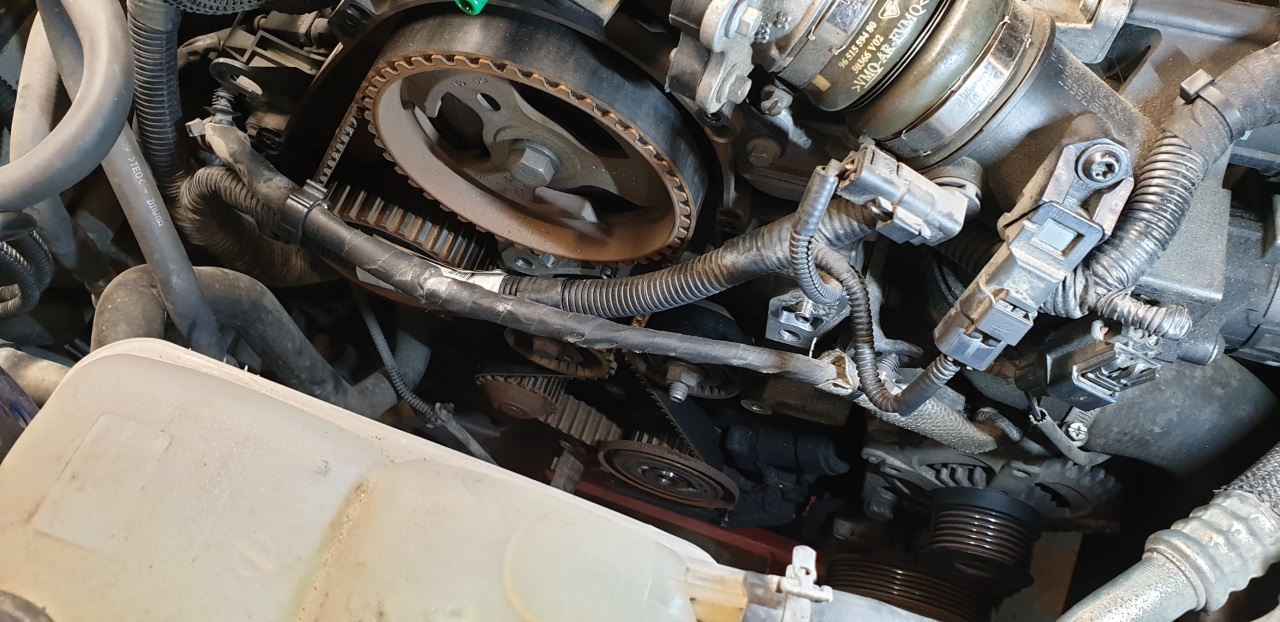
Bort med övre plastkåpan som sitter i ett antal 7mm hexskruvar. Pallar upp under motorn med en separat saxlyft och några lyftpuckar och lossar motorfästet, både från chassie och från motor. Kamremmen går runt detta fäste – så det måste bort. Efter det plockar vi bort den undre plastkåpan från sidan genom hjulhuset. För att komma åt den måste dock multiremmen och remhjulet till denna bort. För att lossa multiremmen lossade jag först remspännaren till den vilket gjorde det hela enkelt.

Här plockar vi bort kamremsstyrningen (en liten plastklack till höger under vevaxeln) och vevaxelspositionssensorn (??) för att kunna få loss kamremmen.
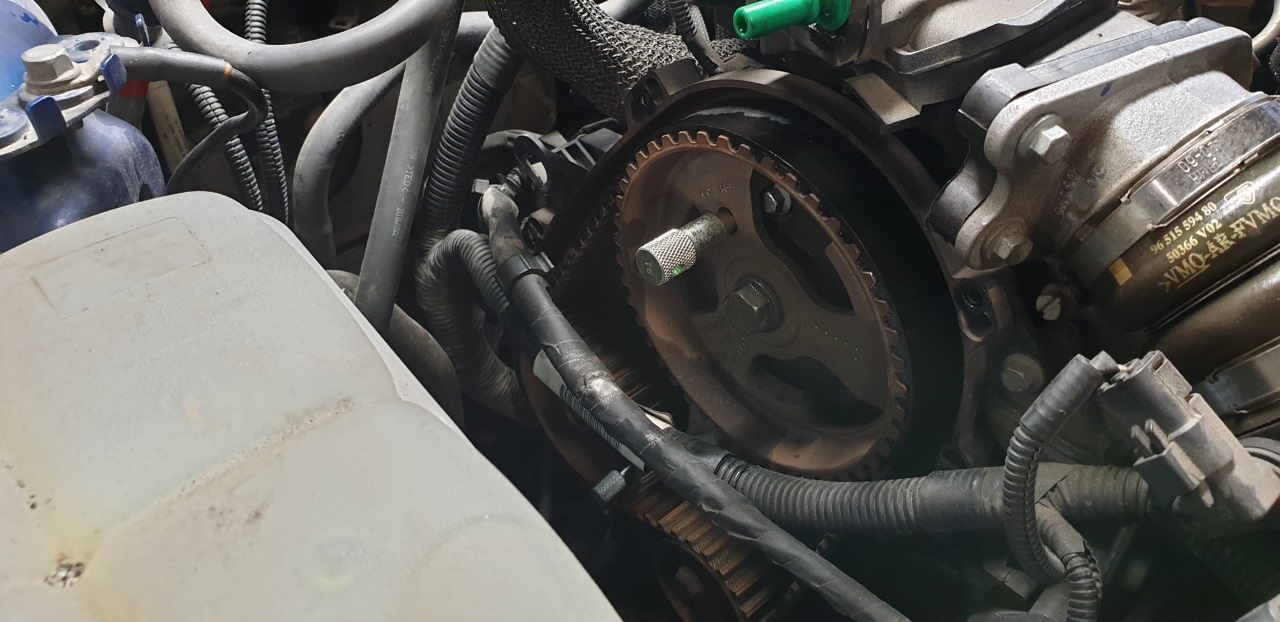
Använder en hylsnyckel för att vrida vevaxeln i motorns rotationsriktning tills vi når övre dödläge – där hålet i kamaxeldrevet linjerar hålet i motorblocket så att vi kan spärra kamaxeln med universalverktyget vi köpt tidigare. (Det fungerar med en vanlig insexnyckel med om man vill). Tricket här är att hitta det läge där hålen linjerar både i kamaxeldrevet, vevaxeldrevet och i högtryckspumpens remhjul. Detta sker en gång på 6 varv om jag inte tänkt fel, så det kan krävas en del vridande på vevaxeln..
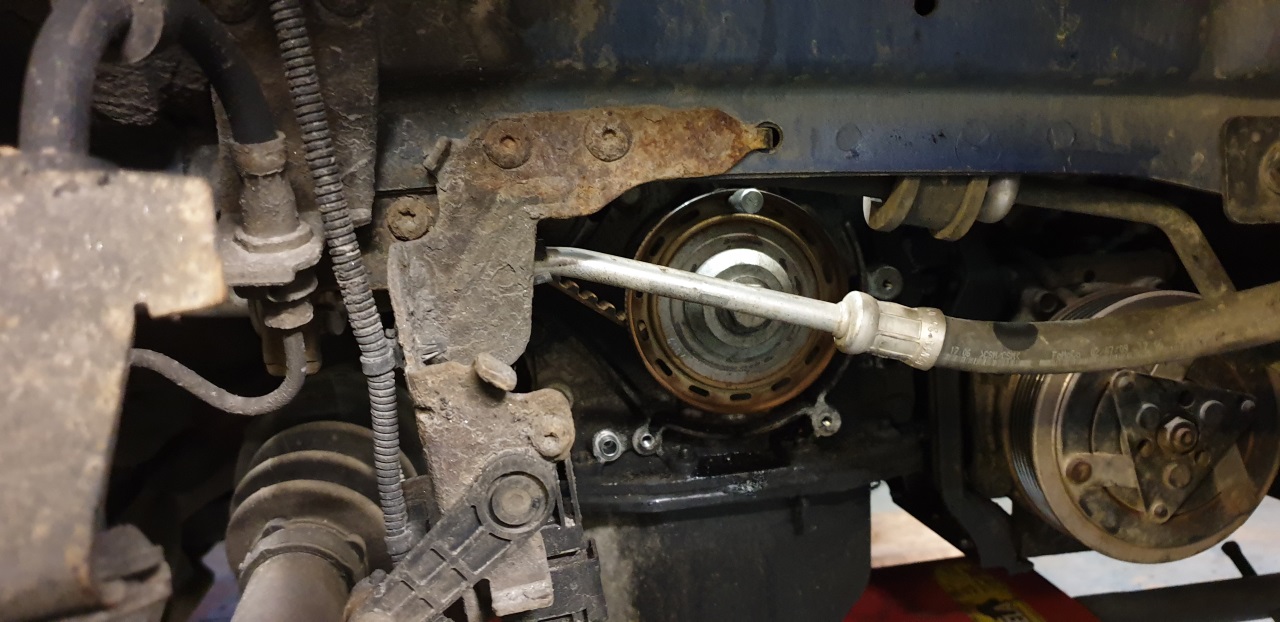
Jag hade dock inte riktigt koll på var linjeringshålet för högtryckspumpen satt och missade detta, men så länge remhjulen inte vrids på under processen är det ingen fara, dock rekommenderar jag att man hittar linjeringen även här för att vara 100% säker.
Efter detta är det bara att demontera kamremsspännaren och remmen.
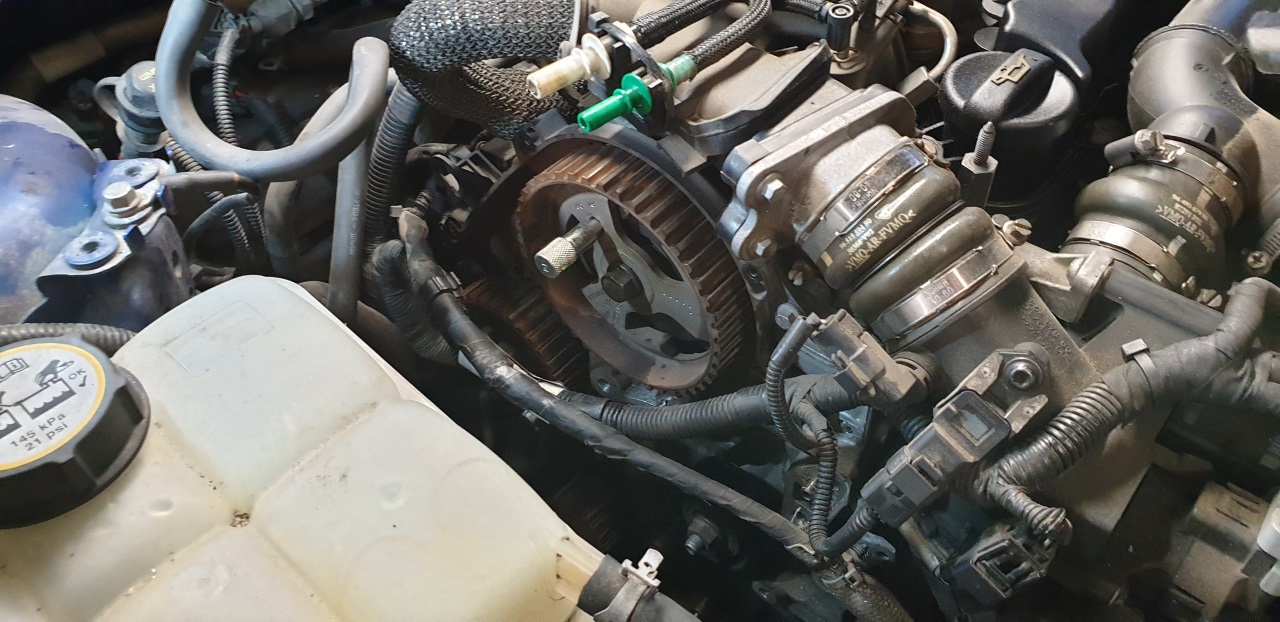
Efter detta plockar man bort löphjulet som följer med i den nya kamremssatsen och eftersom att vattenpumpen drivs av kamremmen på denna motor är det rekommenderat att byta vattenpump i samband med kamremsbyte. Det vore sjukt tråkigt med ett vattenpumpshaveri som raserar hela motorn. PSA-motorn i denna volvo är en motor där ventilen kan komma i kontakt med kolven om kamremmen inte monteras korrekt, vilket gör det än viktigare att göra allt rätt vid rembytet. Blir det fel har man troligen ett totalt toppras på sina händer och med det en hel del jobb och kostnad..
När man plockar loss vattenpumpen kommer all kylarvätska som ligger över pumpen att rinna ut så var beredd att samla upp denna. Egentligen ska man väl dränera systemet innan man lossar pumpen, men jag valde att dränera pumpvägen istället vilket går lika bra.
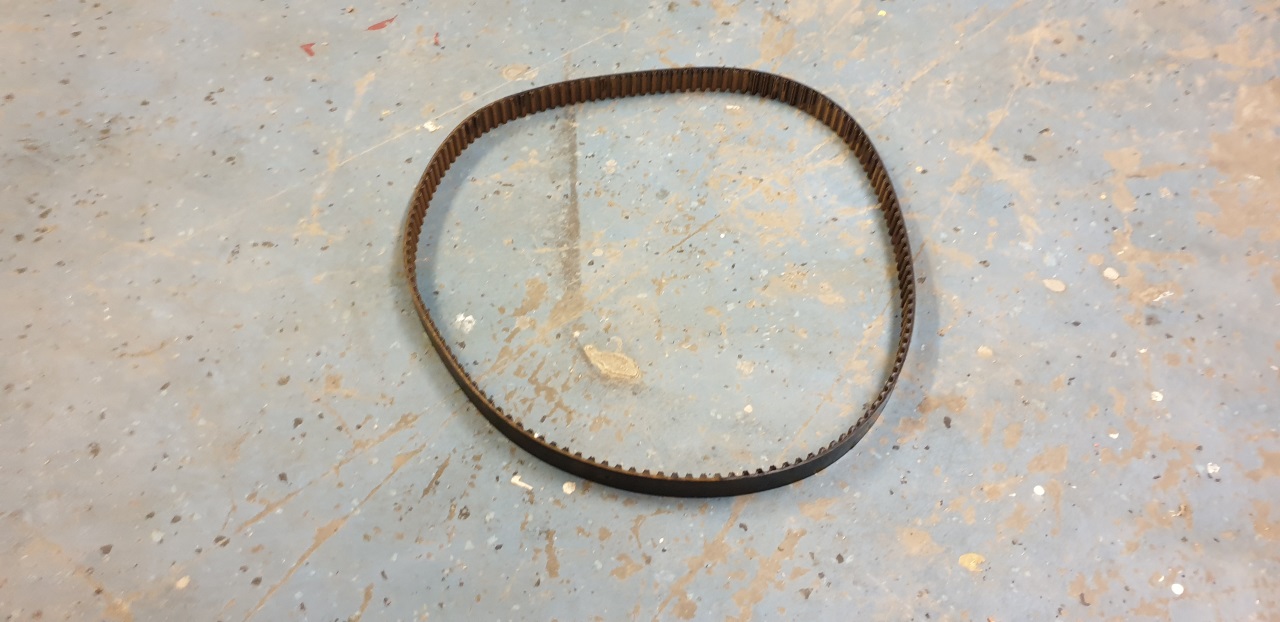
Kamremmen såg helt okej ut, vilket den ska göra när man byter. Värre var det med multiremmen som driver AC och generator. Den var spröd och bitar föll av när jag plockade loss den, så det blev att tvärt åka och köpa en ny sådan innan återmontering. Ett multiremsbrott är ingen katastrof, men det är lika bra att byta när man ändå skruvat loss allt då den kostar under 200:-.
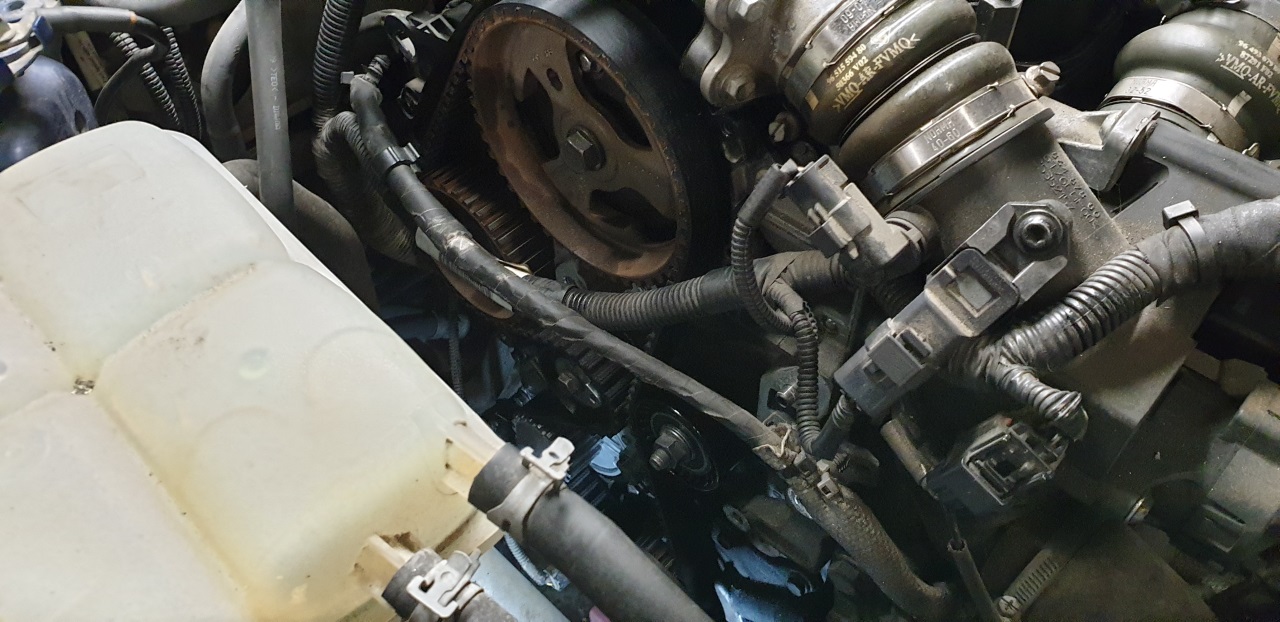
Efter att ha rengjort vattenpumpsfästet ordentligt och skrapat bort alla rester av den gamla packningen som satt kvar återmonterades vattenpump, löphjul och kamremsspännare – dock utan att spänna spännaren. Efter detta monterades den nya kamremmen enligt instruktionen, från vevaxel via löphjul, kamaxel, högryckspump, spännare och vattenpump. Det är viktigt att se till att remmen är spänd mellan vevaxel, löphjul och kamaxel eftersom att avståndet mellan vevaxel och kamaxel är det viktiga måttet vid kamremsbytet. Får man detta en kugg fel finns som sagt risk att motorn rasar.
När remmen är på plats är det dags att spänna. Med en insexnyckel i spännaren vrids denna runt så att markeringen ligger rätt:
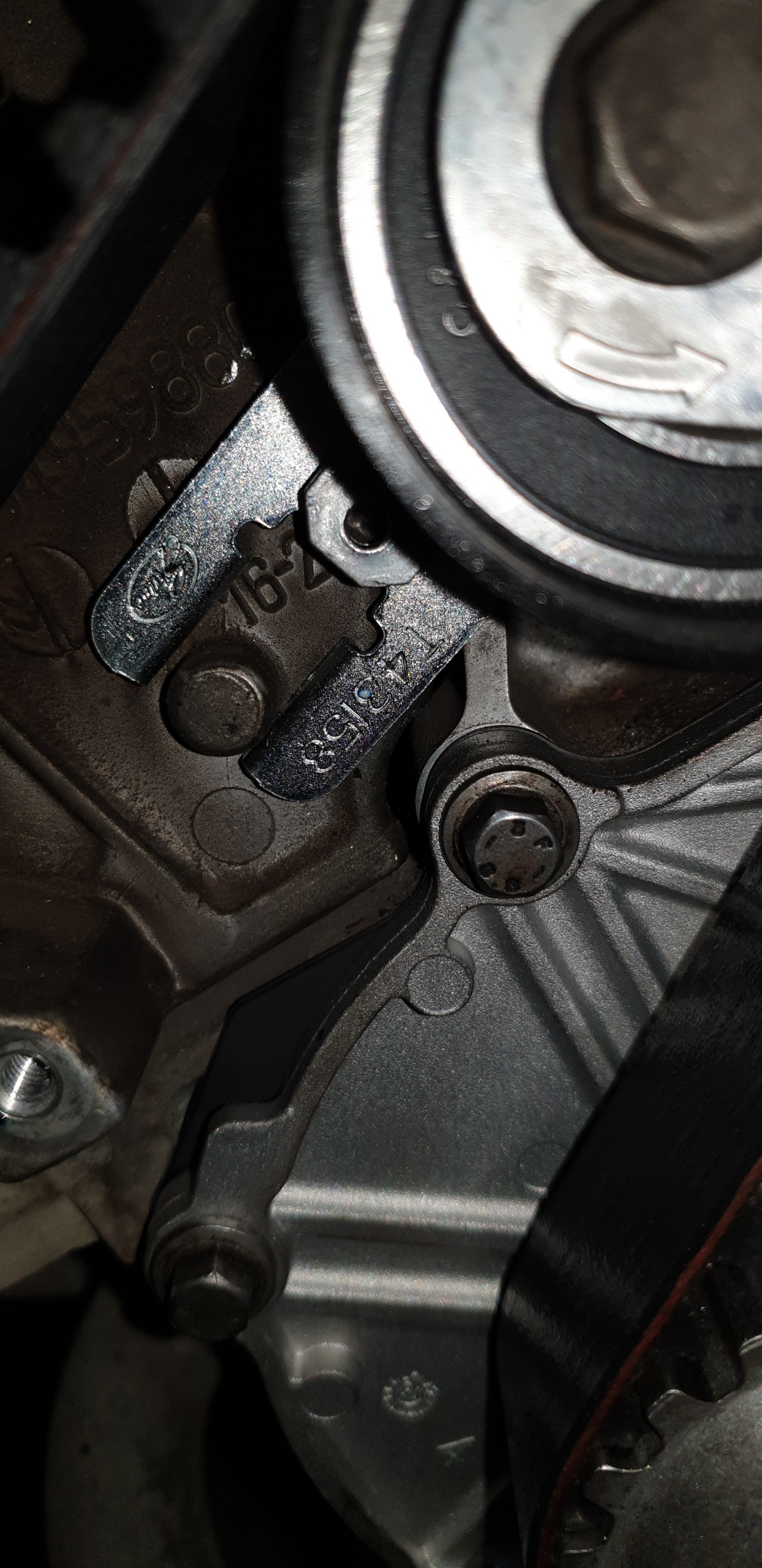
Detta är enklast att kolla med kameran på telefonen då det är lite svårt att se spännaren när den sitter monterad. Detta ser bra ut, så spännaren drogs åt enligt angivet moment.
När detta är gjort plockas låsverktygen bort från vevaxel, kamaxel och högtryckspump och motorn dras försiktigt runt 10-15 varv med hylsnyckel på vevaxeln. Detta för att se till att ingenting kärvar, att ingenting tar emot inuti motorn och att remspänningen är OK efteråt. Så – när detta är gjort inspekterar vi remspännaren igen och om den ändrats lossar vi och justerar om den.
Nu är det bara att återmontera resten i omvänd ordning från demonteringen: Remstyrare, vevaxelsensor, plastkåpa, remhjul, motorfäste, övre plastkåpa, multirem med spännare, el- och diselledningar. Sedan dit med innerskärm, hasplåt och plastkåpa på motorn och sedan är det bara provturen kvar efter påfyllning av kylarvätska. Med lite tur fungerar allt klockrent.
Passade på att göra en service och byta till vinterdäck när bilen ändå var i garaget, så nu är den fit for fight, förhoppningsvis för många mil framöver!